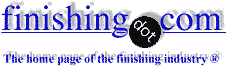
-----
Air agitation in water quenching
Q. I have a water tank used to cool aluminum parts that are around 700 °F. The parts are in the tank close to 20 seconds. The water temperature stays around 100 °F. The parts cool to around 200 °F after they are removed from the tank. Will air or mechanical agitation help cool the parts quicker? Also, which would work better air or mechanical agitation?
Thank you,
Bill Price- Shelby, North Carolina
2002
A. Hi Bill, my experience is with plating, and extrapolating to heat treating might be questionable, but I believe that air agitation is much more effective than mechanical agitation.
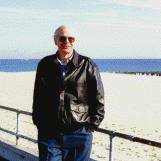
Ted Mooney, P.E.
Striving to live Aloha
finishing.com - Pine Beach, New Jersey
A. Hi Bill,
First off, ask yourself the question ... if I get perfect mechanical mixing versus perfect air mixing, won't the far colder (ambient, one hopes) air cause the tank temperature to fall much faster, eh? But will that have an effect on the parts? Would an 'overcool' cause stresses?
Perhaps go to the archives & have a gander at thread #9311.
It's all a matter of distribution AND cooling. Not knowing the tank size and the part sizing, I'm loath to make any suggestions. Heck, 20 seconds is a pretty short time. Why spend $ to gain a few parsecs?
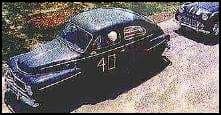
Freeman Newton [dec.]
R.I.P. old friend (It is our sad duty to
advise that Freeman passed away 4/21/12)
Ed. note: I think a typo slipped in there, Freeman -- you'll want to re-check how big a parsec is before poo-pooing 19.2 trillion miles :-)
A. Are you hardening the aluminum? If so, there is a rate of cooling that is important, i.e., the starting temp of the water is in a given range. I suspect that you are ending up with hot water because you do not have enough (a big enough heat sink). I also do not have a understanding for your need for speed. It appears to be a question that is possibly only a facet of the overall process and possibly out of context.
James Watts- Navarre, Florida
Aluminum: its forms, alloys, and tempers"
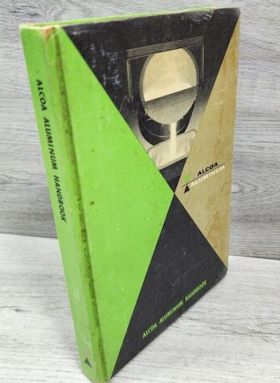
on eBay or Amazon
or AbeBooks
(affil link)
A. What alloy(s), what part(s) geometry, what fixturing, and what are you trying to accomplish? The 700 °F suggests an annealing, in which case cooling rate is relatively unimportant, and you are trying to ease handling and increase throughput. Increasing tank volume, overflowing cold water, pumping and proper fixturing will improve cooling. Air agitation will help if no air pockets and will also lower the water temperature by increasing evaporation. Like the other respondents, I don't understand limiting the cooling time to 20 seconds.
If solutionizing wrought alloys, an initial temperature of 830-970 °F (dependent upon alloy) and quenching in cold water is preferred (except for bulky/complex shapes subject to quenching stresses). The final temperature of 200 °F is excessive, especially for 7xxx alloys, as some precipitation hardening will occur prematurely. If solutionizing castings, an initial temperature 950-1000 °F is used, and the quenching is normally into 150-212 °F water to minimize stresses. If precipitation hardening ('aging') any alloy, the 700 °F is excessive. Information is from Alcoa Aluminum Handbook (1962) ⇨
but I expect it is valid for newer alloys except possibly Al-Li types.
- Goleta, California

Rest in peace, Ken. Thank you for your hard work which the finishing world, and we at finishing.com, continue to benefit from.
Q, A, or Comment on THIS thread -or- Start a NEW Thread