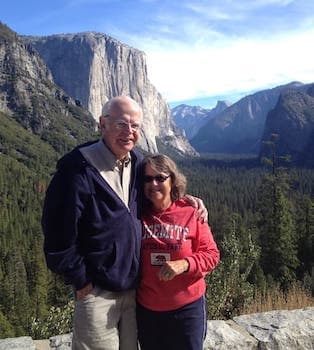
Curated with aloha by
Ted Mooney, P.E. RET
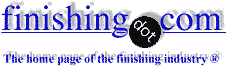
The authoritative public forum
for Metal Finishing 1989-2025
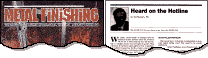
-----
Black anodizing problem - purple not black

May 15, 2022
Q. Hello,
My name is Joshua, and this is my first post here after reading forums for a few years.
I have a small anodising setup that I use to anodise telescope adapters that I make out of 6061 aluminum.
Usually I get results I am happy with, but I'm not liking what I have seen lately. I will describe my setup and process.
Type II LCD anodising. Off the machine, I bead blast the parts, but that was giving me a really matte finish and I was after more of a smooth shiny finish. So this time I polished the parts by hand on a buffing wheel with some white polish for aluminum. They turned out really smooth. I then washed them in the dishwasher with soap to clean them. I try to clean them as much as possible before etching so that I don't have to etch as much, as I find the etch gives a matte finish also.
I then etched them for 30 sec at 60 °C., then a double rinse. Then onto the de-smut bath for a few minutes. Then a dip in a bicarb soda solution to neutralise the acid. Then following this, they get a double rinse. I then use a bright dip bath at room temp, again, baking soda [in bulk on
eBay
or
Amazon [affil links]
afterwards, followed by double rinse.
Then to the anodising tub. This particular time was a new batch. 3:1 water to battery acid
⇦ this on
eBay
or
Amazon [affil links]
. (BTW, all my tubs including the rinse tubs use distilled water) The temp for this run was 18 °C. I anodised at 0.5 Amps/100cm2. I use CC mode and the voltage ramps slowly automatically. However this time, instead of setting full amps from the start, I ramped the amps manually to 5.7 Amps by hand, which only took about a minute to reach full amps. Peak voltage (15.8 volts) was reached about 30 min into the anodising, and I pulled the parts after a little under 50 min when I saw the voltage start to drop, at which point I believed I had reached PAR. The anodising tank and all the other 4 tanks are well agitated with compressed air entering via PVC tubing at the bottom. I checked, and I don't appear to have any oil from the compressor in the lines.
Then, I dipped the parts in the baking soda, then a double rinse before the die tank. The die tank is a good jet black die from a reputed supplier for hobby anodizing, light fastness of 8. The temp is 60 deg;C. They stay there for 15 to 20 min.
Then a double rinse before the sealer tank. I use a nickel acetate sealer, I haven't had problems with it; I don't get colour fading over time, and the die takes well to the parts. There is no black die in my sealer tank.
I seal at around 80 °C for 15 to 20 minutes. After sealing, the parts are rinsed and that's it.
Apart from the polishing on the buffing wheel, this is the procedure I usually follow, and this is the first time I have seen such colouration and shades of colour like this.
So now that I have given some background, would anyone know what is the contributing cause to this coulouring on the anodised part?
I have attached some photos, you can see the nice black ones, which were not from this run, and the ones that were from this run, that appear to have a coloured surface. Note, the parts are like this straight out of the last bath, they have not been exposed to any light.
Thank you for reading, and I hope I can get some help with this.
Regards
Joshua
- Western Australia
A. Hi Joshua. The short answer is that your anodizing is not thick enough for good black color. If all went well, your thickness is about 0.3 mil whereas most people think 0.5 mil is the minimum for black color, and anodizing to 0.8 mil is not uncommon.
On a matte surface you possibly may have got by with it because the light bounced around a bit in the peaks and valleys and got absorbed before being reflected, but even then 0.3 is not thick enough. I am also not convinced that the parts were fully clean; you might try a scrub brush ⇦ this on eBay or Amazon [affil links] and powdered pumice ⇦ this on eBay or Amazon [affil links] .
Luck & Regards,
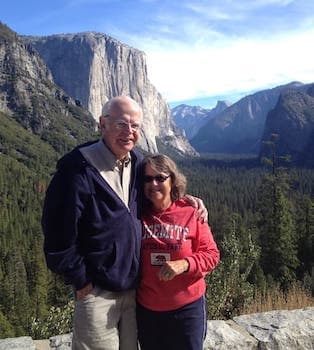
Ted Mooney, P.E. RET
Striving to live Aloha
finishing.com - Pine Beach, New Jersey
May 2022
Hello Ted,
Thank you for your fast reply.
Both of your solutions were a concern of mine.
In regards to the thickness not being enough. I have been hesitant to leave them in the anodising solution for longer than 50 min because, at this point, and sometimes even earlier, I start seeing the voltage drop on my power supply, which I see as the parts reaching PAR, and thereafter the anodising layer is being corroded away. Are you suggesting to leave the parts in the solution for longer, even if the voltage is dropping? Note, it only drops by a half a volt or so from peak voltage.
In regards to the parts not being clean enough, this could also be the case. I only gave 30 sec in the etch tub, but they did pass the water break test. The reason for such a shirt time is I am after a shinier finish, and as I understand it, and from experience, a longer etch gives a more Matte finish. I will see what I can do there.
Thanks again.
- western Australia
May 15, 2022
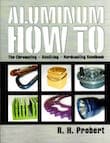
Aluminum How-To
"Chromating - Anodizing - Hardcoating"
by Robert Probert
Also available in Spanish
You'll love this book. Finishing.com has sold almost a thousand copies without a single return request :-)
A. Hi. I confess to being largely unfamiliar with hobby anodizing, and low current density anodizing. I've never even heard the term "PAR" (peak anodizing resistance) and had to look it up on a hobby anodizing site.
But it is true that at a given temperature the acid can dissolve the anodizing as rapidly as it forms at a given voltage; so it may be the case, although I'm not claiming that it is, that you can't get over 0.3 mils with LCD. But hard anodizing up to 2 mils is possible at higher current and voltage on "easy" substrates like type 6061. Are you sure the temperature hadn't risen and was still 18 °C at the end of your run?
Luck & Regards,
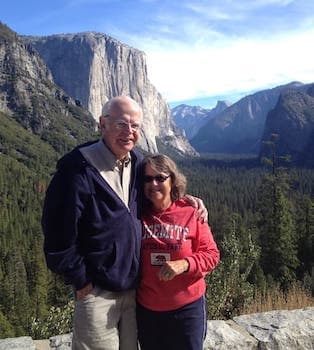
Ted Mooney, P.E. RET
Striving to live Aloha
finishing.com - Pine Beach, New Jersey
May 2022
Q. Hi Ted,
Yes, the temperature was still 18 deg at the end of the run. It's quite a large tank for the volume of parts, and it was a cold day, only 13 deg.
- Western Australia [returning]
May 15, 2022
A. Try direct chemical coloring of aluminium (no need for anodizing).
Black for aluminum:
use boiling solution of 20 g ammonium molybdate and 5 g of sodium thiosulphate
⇦ this on
eBay
or
Amazon [affil links]
in a liter of water, immerse the objects, rinse, dry, wax or lacquer after the development of color.
According to Wikipedia article on chemical coloring of metals:
https://en.wikipedia.org/wiki/Chemical_coloring_of_metals#Examples
Hope it helps and good luck!
- Cerovski vrh
May 16, 2022
⇩ Related postings, oldest first ⇩
Q. In our Black Anodizing process, lately our parts are coming out with a purplish sheen to them, instead of the dull black matte finish. Any suggestions on what the problem might be?
Christi Blackley- South Fulton, Tennessee, USA
2002
2002
A. If nothing has changed elsewhere (and you are dyeing to saturation), the dyeing problem could be due to: weak solution, improper pH, impurities clogging pores (e.g., high sulphates), high temperature causing premature sealing, or imbalance in a multi-component dye. Send a sample to your dye supplier for analysis; I know of a case where a gold dye addition was recommended to cancel a blue-ish tinge in a black dye (and it worked!).
Ken Vlach [deceased]- Goleta, California

Rest in peace, Ken. Thank you for your hard work which the finishing world, and we at finishing.com, continue to benefit from.
A. This is a very common problem.
When the anodizing thickness is low the blue components of the black dye are absorbed preferentially. So just increase your thickness.
Also common, is the fact that people who use so-called computerized controls do not understand that you must have the correct surface area for the computer to apply enough amperage.
If you are doing a 2000 series alloy, you MUST have 21 volts (plus 1 more if titanium racks) to get 12 amps per square foot. So override the computer and raise the voltage to 22, then all the components of the black dye will absorb.
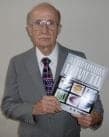
Robert H Probert
Robert H Probert Technical Services

Garner, North Carolina
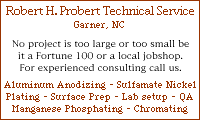
2002
A. The answers you have already received are accurate. One thing I would add other than the causes mentioned is the pH of the seal after the anodize and dye process. A lot of proprietary sealers have specific pH ranges. If the seal is not maintained within these parameters, I have seen it cause the condition you describe. Typically, manufacturers of the sealants recommend checking and adjusting pH on a daily basis as a means of control.
Peter Cox- Seabrook, New Hampshire USA
2002
Q. I have a batch of parts Anodised and they have come out with a blue tinge, it is critical that these parts are midnight black, we are using 6061 T6 for these components.
Should we be using another grade or is it a fault from the anodising process?
It isn't the first time this has happened with 6061 T6.
Engineering - Brisbane, Australia
2005
![]() |
2005 A. It sounds like either your black dye is weak or you didn't anodize the parts long enough. Check those two issues - they are the most likely causes. Compton, California, USA A. Black Dye "coming out blue" is very common when the anodic film thickness is too low or the pore size is too small from too low temperature. Increase your thickness. ![]() Robert H Probert Robert H Probert Technical Services ![]() Garner, North Carolina ![]() 2005 |
2005
A. 6061 should anodize nicely and have no problem with dyeing black. 3 thoughts come to mind.
#1. Inadequate coating thickness
#2. Weak dye concentration
#3. Dye Ph is out of spec.
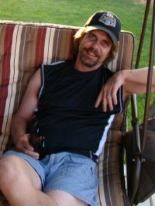
Marc Green
anodizer - Boise, Idaho
Q. Black Anodize Type II. We are seeing sporadic color variation at times (purple instead of black) on billet machined T6061 parts. Situation is not limited to a given customer or lot of parts. We primarily process 6061 material on our line. We will have some work bars which are completely uniform deep black and at times I will get a work bar which have some parts on rack of the work bar that appear to be shades of purples and not deep black. This can occur on the same rack (some parts on rack deep black, others not) while everything else on the work bar is fine. The initial thought was bad contact to where thickness may be inconsistent. However, after checking the lighter shade parts with a thickness gauge we are finding parts have adequate thickness (.007"^.0007") and are consistent with other parts with the same thickness that are deep black in color. There is no smut formation on the parts either. Our dye is air agitated, pH is verified and within spec. Not sure what else to look to understand what may be causing the issue.
- Whittier, California
March 12, 2018
A. Hi Mike. The only times I've personally seen this it was the result of the anodizing being too thin, as mentioned by Robert Probert. But in your case, with heavy thickness verified, and pH of the seal tank verified, I wonder about Ken Vlach's idea that the dye tank itself is causing partial sealing before the dye has been fully absorbed? Have you verified that the temperature is not too high?
If you search this site for "black anodize" you'll find a number of threads which might offer further ideas. Good luck.
Regards,
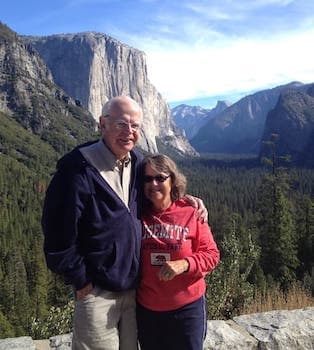
Ted Mooney, P.E. RET
Striving to live Aloha
finishing.com - Pine Beach, New Jersey
March 2018
A. Varying shades on the same rack has to be (1) contact reliability or (2) air agitation displacing solution (which again is thickness).
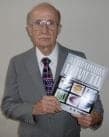
Robert H Probert
Robert H Probert Technical Services

Garner, North Carolina
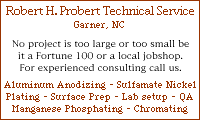
March 12, 2018
QUICKSTART:
Please forgive the typographical error, which Willie and then Mike called our attention to.
The heaviest anodizing, hardcoating, is about 0.002" thick. Anodizing thickness of 0.0007" is mentioned in some architectural specs and is about as thick as decorative anodizing gets. A lot of anodizing is significantly thinner, but thick anodizing means deeper pores for better absorption of dyes/full saturation of dark colors, so .0005" to .0007" is not unusual for black anodizing.
? Hi Robert. But if the problem is lack of thickness how do we account for Mike measuring it as .007"^.0007"?
Regards,
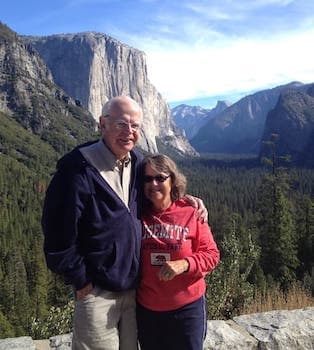
Ted Mooney, P.E. RET
Striving to live Aloha
finishing.com - Pine Beach, New Jersey
![]() |
A. I'm guessing Mike means .0007", not .007. - Green Mountain Falls, Colorado March 13, 2018 A. Hello Gents, - a sunlit rock in the Irish Sea March 13, 2018 Sorry, thickness was .0007". Ted, one thing you noted was dye temp. Our range is 120-140 °F per TDS. We are at the higher end of the range at 140°F. We decided to take it down to 130°F to see if that helps. Sent a sample to vendor for dye concentration about 3 weeks ago. TDS recommends 10g/l, our current concentration is 13 g/l. Dye is about 1.5 years old. We also have good air agitation. We will see what that does. Please let me know if there are any other recommendations. Thank you all for you help. Mike Jetter [returning]- Whittier, California March 13, 2018 |
A. Hi Mike,
If that black you're running is the ubiquitous Reliant HBL (specs sound about right), 1.5 years is fine if you've got your concentration kept up, since is a single-component dye and won't age-shift like a mixed dye in my experience, and anyway if you've got a mix of shades on one rack it's not a tank shifting issue. And anyway that dye is DEAD STABLE. The last time I changed my bath was in October of 2014- it's still black as night. I also run it stronger than recommended, but that's neither here nor there in terms of my response to your issue, which is that I'm wondering whether you've got good, even rinsing coming out of the ano tanks, and whether you precondition parts for dye with a nitric dip (about 5-6% vv from 42 °Baumé, not too long or they'll take on a scorched appearance, immersion time depends on concentration and circulation)? Do you find yourself having to run elevated buffer in your dye (this is totally fine per the manufacturer) or really keep beating the pH of the dye tank up constantly with ammonia? The theory here is that Sulfuric is way more 'sticky' than Nitric, and the post-anodize nitric dip will ensure that the parts are squeaky clean to accept dye, and minimize Sulfuric drag-in. It's also a lifesaver if you have issues with blind holes bleeding out after seal. Of course you still have to rinse the Nitric off really well before going into the dye, but it rinses MUCH cleaner, and with MUCH less effort!
If you're already doing this, then yeah I'm gonna go with lost contact :)
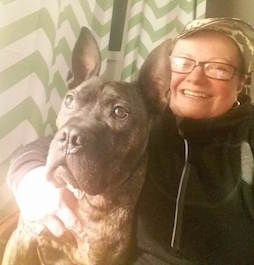
Rachel Mackintosh
lab rat - Greenfield, Vermont
May 2, 2018
A. Sorry, is that coloring bath electrolytic bath as tin bath or electroless coloring? Also if I were you I would share pics which describe the problem. I have some answers but let me know the electrolytic or electroless bath?
Sincerely
- turkey,sakarya
May 15, 2018
Mike,
When you mention varying shades of purple rather than black, is each piece the same color purple throughout the part, or is it a gradient with the middle of the affected parts being lighter than the ends? I have seen both of these cases on my line in the past.
If you have a gradient within each part, then I would highly recommend checking your connections on the racks themselves; including taking off the bolts/connectors and giving them a good scrub to make sure you're working with clean surfaces. If that were the case you would probably see a variation in film thickness within the part. Also make sure the connection from the work bar to the anodizer blocks is very solid and clean. A gradient would mean you're not getting enough power to your parts.
If every part is the same shade of light through the part then I would still recommend to service the rack to eliminate that as a potential source. Personally every single time I see this light black (purple) condition the part is always loose on the rack- regardless of the film thickness measurement. Every time. It does not make sense to me why the thickness is adequate even on a loose rack, but it is what it is.
Also of note, is the position of the light pieces on the work bar consistent? Or do they seem random? I have had instances where a poor rinse (when sprays do not penetrate the work load toward the inside of the rack) affects the colorability of the inside portion of the work load. If this is the case I would increase the immersion time of your pre-Dye DI rinse to give your spray rinses a helping hand. If you don't have spray rinses at all make sure your agitation does not have any dead spots in which gunk could hide in the pores and prevent dyeing.
Best of luck.
Aluminum Anodizer - Grand Rapids, Michigan, USA
June 12, 2018
Q, A, or Comment on THIS thread -or- Start a NEW Thread