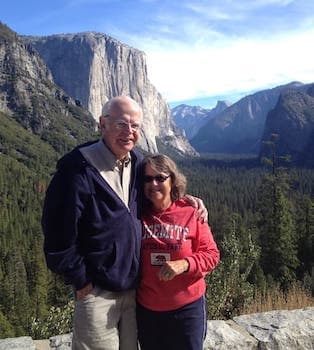
Curated with aloha by
Ted Mooney, P.E. RET
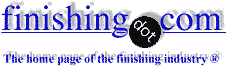
The authoritative public forum
for Metal Finishing 1989-2025
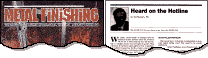
-----
What is the Corrosion Life of Nickel Plated Components?

Q. I am having some banjo parts re-plated. From the factory (Gibson 1957) they were nickel finished. My plater says nickel won't last long, it needs a protective layer.
I see similar banjos of that Era have lost their shine, but my plater is telling me they won't last more than a few weeks before corrosion begins.
What is the deal, and what can I do to protect the finish?
- California
February 3, 2023
A. Hi David. These days decorative objects are usually plated with nickel followed by a coating of chrome plating; and, yes, the nickel-chrome does significantly improve both the tarnish resistance and the corrosion resistance over nickel-only. But that does not mean that nickel plating will be unsatisfactory for banjo parts as long as it is not too thin. At somewhere around 0.001" or more it should be fine and last for years if not abused.
Exactly why your plater is reluctant is hard to say. It could be because he is not used to plating the nickel thick enough, or because he is thinking your banjo will be out in the rain or abused and he's watching out for you, or it could be that he just isn't well set up to plate nickel-only at a proper thickness.
Luck & Regards,
Ted Mooney, P.E. RET
Striving to live Aloha
finishing.com - Pine Beach, New Jersey
⇩ Related postings, oldest first ⇩
Q. We are doing Nickel plating of our product (chains) with a coating thickness of 0.007 mm [ed. note: 7 microns]. We want to know the specification for Salt spray life (no of hrs min) when tested as per ASTM B117.
V.Sudharsan- CHENNAI, TAMIL NADU, INDIA
2002
A. ASTM B117 does not give a requirement for the time duration of the salt spray test. It only tells you how to setup the test. You need to ask why you are performing the salt spray test and if it is a requirement to a standard your components are designed to. Typically product specific codes will indicate the time required for salt spray testing if it requires salt spray testing. If you don't know the applicable material/product design standard then it may be difficult to estimate a testing duration. Typical tests can run for 96 hours or 48 hours.
M Hogan- Melbourne, Australia
Q. Hi M Hogan,
Nickel plating SST life is 48 or 96 hours for white rust. What is the difference between Ni-Cr and Bright Nickel plating? Izhar
Mohammed.Izhar-ul-haq- Singapore
2004
A. Bright nickel plating means the final plating step is bright nickel. In nickel-chrome plating the part is plated with bright nickel and is subsequently plated with a very thin layer of chrome. This discourages the nickel from tarnishing and symbiotically contributes to the corrosion resistance.
But nickel and nickel-chrome plating can be done outstandingly well and last decades on a truck bumper, or be done so badly that rusting has started before the items even reach the consumer.
Chrome & glass bathroom vanity for sale at a big box store, with plating perforated and rusting already in progress
Perhaps the single most important question is whether the nickel plating is thick enough to ensure freedom from porosity. Unfortunately, this will depend on the shape of the part, the smoothness of the finish, and the reliability of the pre-treatment cycle -- so it isn't real easy. But the MFSA Quality Metal Finishing Guide for Nickel-Chromium Coatings suggests 10 microns of nickel and 0.1 microns of chromium for mild service conditions (which does not include kitchens and bathrooms), and 15-20 microns nickel plus 0.3 to 0.8 microns of chrome for moderate conditions. It anticipates that items plated for mild conditions will survive 8 hours in ASTM B287 "Acetic Salt Spray" (this is a withdrawn spec replaced by ASTM G85 annex A1), while those plated for moderate conditions will last 24 hours in B287 or 4 hours in ASTM B368 "CASS" or ASTM B380 "Corrodkote". Good luck.
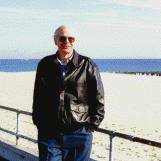
Ted Mooney, P.E.
Striving to live Aloha
finishing.com - Pine Beach, New Jersey
Q. We are doing nickel plating and after that a dip method TOP Coat Lacquer, but the problem is with consistency of the product corrosion life. Can you suggest something?
We are doing Trinickel layer of about 5 to 10 microns.
Also can you suggest proper material type (MS) for nickel plating.
plating shop. - Delhi, India
July 25, 2009
A. Hi, Praveen
Plain mild steel should be fine for nickel plating; no need to pick an exact carbon content or anything. I personally don't think 5-10 microns is quite sufficient nickel plating thickness. Remember that nickel plating is a "barrier layer" plating, not a plating that offers cathodic protection like zinc or cadmium plating. Although porosity or a pinhole in zinc plating would probably not be a problem, in nickel plating it will accelerate the rusting of the substrate.
What you seem to be doing is applying nickel plating for brightness and shine and then relying on a topcoat lacquer to provide most of the corrosion protection. If that is the case, then you need to blame the lacquer rather than the nickel plating for the lack of corrosion resistance :-)
Regards,
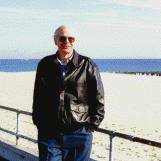
Ted Mooney, P.E.
Striving to live Aloha
finishing.com - Pine Beach, New Jersey
Corrosion rates for Chrome over Satin Nickel
Q. I am trying to help our QA Department.
Do you have access to any data that will give us an idea of how long it will take for parts to show corrosion after chrome has been applied to satin nickel?
I have found lots of information about the process and how chrome helps Nickel resist corrosion, but nothing on the time a chrome over satin nickel plated part will begin to show corrosion.
Thanks,
Julie
Plating Shop Lab Analyst - Houston, Texas USA
April 23, 2014
A. Hi Julie. Since satin nickel is often applied to kitchen and bath accessories ...
If we assume that that is the application, and refer to the earlier entries in this thread, a good starting point would be 4 hours CASS or Corrodkote.
Real life depends on the real life exposure conditions. What kind of lifetime would you like to see, and under what conditions? Good luck.
Regards,
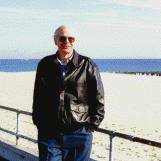
Ted Mooney, P.E.
Striving to live Aloha
finishing.com - Pine Beach, New Jersey
Is the small microcurrent imposed on our electrodes to blame for the copper-nickel-chrome plating corroding?
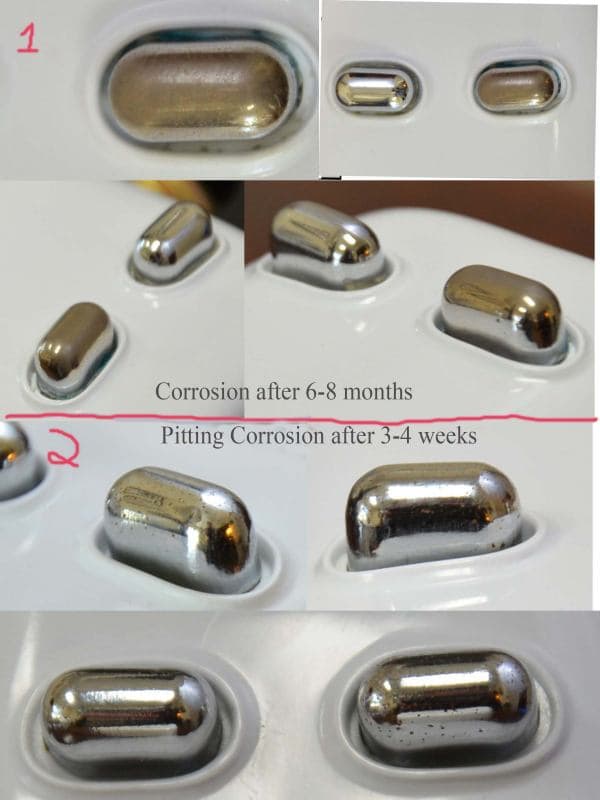
Q. My company has an electrode produced for a microcurrent device. Electrodes are H62 Brass triple plated with copper then nickel then chromium 0.25 µm thickness, so we are told (we received no COC to confirm this). A +DC microcurrent is sent from one electrode to the other with skin completing the circuit. Has anyone seen this and might know if the current could be causing the premature corrosion and pitting in the chrome or if the problem is more likely to be improper specification of plating thickness for conditions as Mr. Mooney described above. It only corrodes and pits on the + electrode, the - electrode is unaffected. Thank you very much for your expertise. I include a few picture for reference.
- Wilmington, North Carolina, USA
July 9, 2014
A. Hi Geoff. It's hard to argue with the facts, and they say that the microcurrent is accelerating the corrosion on the positive electrode. Although you haven't said what the voltage is, since both electrodes are of the same material, any voltage at all will shift the equilibrium and cause the positive electrode to gradually deplate.
If the imposed voltage were low enough, say 100 - 150 mV, it is perhaps possible that plating the positive electrode with semi-bright nickel and the negative with bright nickel would offset the imposed voltage; if the positive were plated with gold instead of chrome it would offset an imposed voltage of about 1.5V.
Despite this theory, the easiest fix may be to simply increase the plating thickness or (and I don't know if there is a medical reason precluding it) plating the electrodes with electroless nickel would probably give better durability than the copper-nickel-chrome plating. The contacts of most DC chargers, cordless phones, etc., are electroless nickel plated. Good luck.
Regards,
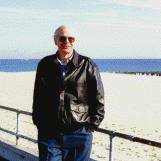
Ted Mooney, P.E.
Striving to live Aloha
finishing.com - Pine Beach, New Jersey
Q. Thank you Mr Mooney for your advice. I have spoken with a few other consultants that concur with your assessment. The max current is 480µA @ 20V so mitigation by imposed voltage compensation is probably out. However, electroless nickel plating sounds like a good solution and no medical reason exists not to use it that I know of. We also looked at increasing the chromium plating thickness by 2X-3X, however since it is anodizing the positive electrode, it seems that would only prolong the inevitable. Stainless steel was mentioned as well for the probes, but I am unsure if the increased electrical resistance of the metal would be significant enough to cause a noticeable decrease in efficacy.
I wanted to ask you about plating thickness. It seems that given the unit will be used in bathroom with a conductive gel that would constitute a moderate service condition and require "15-20 microns nickel plus 0.3 to 0.8 microns of chrome for moderate conditions" per your post. You mentioned increasing the plating thickness as a solution, would that be the nickel and chrome or just the chrome? Thank you
Looks like we have our work cut out for us... Thanks again.
Geoff Ring [returning]- wilmington, North Carolina, USA
A. Hi. At this point neither you or I know the nickel plating thickness, so it's hard to talk cogently. But to answer on the general level, yes, the nickel plating thickness must be increased or can be decreased based on service conditions. When you see deterioration like this and want to slow it down, regardless of what service classification we assign, you must increase the nickel plating thickness, not just the chrome. My best guess, but that's all it is, is that 40 microns (0.001") of electroless nickel will give you a satisfactory life and satisfactory performance if you go that way instead of the nickel-chrome plating.
If you can't wait several years for results from test parts, you may want to attempt an accelerated corrosion study. There are outfits who specialize in electrochemical testing for special situations of this sort. Corrosion Testing Labs in Newark, DE is one that I've worked with. Good luck.
Regards,
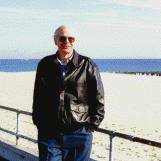
Ted Mooney, P.E.
Striving to live Aloha
finishing.com - Pine Beach, New Jersey
Q. How many hours is the standard Salt Spray Test duration for Nickel Plated item with 4-12 microns plating thickness?
Sien ColesPlating - Laguna, Philippines
March 13, 2019
A. Hi Sien. Please try to explain your situation rather than posting an abstract question so that we can try to answer you without a lot of lost motion. 4 microns is probably not ever satisfactory; 5 microns is the minimum on copper, and 10 microns on steel for mild exposure.
You might get 24 hours from 10 microns on steel if the base is well polished (in thread 51976 the inquirer cannot obtain 24 hours with 10-15 micron plating on a rough surface, but does achieve it with 20 microns). however.
Regards,
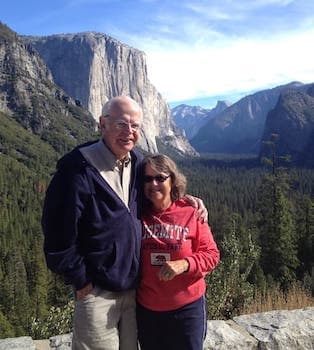
Ted Mooney, P.E. RET
Striving to live Aloha
finishing.com - Pine Beach, New Jersey
Q, A, or Comment on THIS thread -or- Start a NEW Thread