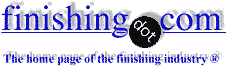
-----
Is it justified to invest in a plating line to service our products
2002
We have a tremendous problem in the Dallas, Texas area. We have a shortage of ZINC PLATERS who can handle large volumes, quick turn-around, and quality. We had the best plater in the area, but paperwork and environmental concerns with TNRCC have crippled this company. Rack plating is the major concern, our parts are 10'2" long. Most in the area cannot handle this length. We don't know if we have enough volume to justify investing in a zinc line to service our product. Can someone help direct me on this? We have been basically shut down and at the mercy of several platers trying to run our product. Our process before we plate is to punch hole patterns and weld tabs and connectors onto the metal. We would use galvanized metal but the problem is the welding and toxic fumes are a major concern. We have powder coated these, but the cost is very high.
Any suggestions or comments would help at this time. I thank you in advance for your professional advise.
Best regards,
Greg Langston- Dallas, Texas
Certainly you can bring zinc plating in house. Starting with the size of the pieces and the required production rate, a consultant would be happy to give you the floor space requirements and approximate capital and operational costs as a quick first phase of a project.
But do you really want "paperwork and environmental concerns with TNRCC" to "cripple" your company too? Over the last 25 years, nearly all American corporations who operated captive plating shops have closed them up and farmed their work out to plating jobshops because of the liability and uncertainty, and the fact that it is virtually mandatory these days to have on staff an environmental/safety engineer whose only job is staying on top of electroplating regulations and filing the necessary paperwork. If plating is not your only business, and if highly proprietary finishes are not part and parcel of your product, it's tough to staff the department the way you need to.
Also, in the event of labor strife, I can almost guarantee you that your union will have TNRCC knocking on your door faster than the picketers can raise their placards (because it almost always happens). The environment is such a "hot button" with the public that all the union has to do is fake an "anonymous tip", and the regulators will be climbing all around your plating shop daily.
Going into the plating business these days is an activity justifying a TV show "Extreme Entrepreneur" :-) So it is not a simple traditional "make or buy" calculation. If you are extreme entrepreneurs, go for it! If you are an established, relatively conservative business, you need a lot more incentive than a slim cost advantage to consider starting a plating shop and potentially turning your life upside down.
Good luck (but give powder coating a second look)!
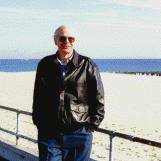
Ted Mooney, P.E.
Striving to live Aloha
finishing.com - Pine Beach, New Jersey
2002
In order to make a captive plating shop worthwhile for plating a low profit margin process such as zinc you should be sending out at least $600,000.00 of work yearly to jobs shops.
Todd Osmolski- Charlotte, North Carolina, USA
2002
You may want to look at cold rolled steel with proper pretreatment, and a good powder coating to service your product. This will reduce TNRCC involvement and have little effect on your welders health. You need to address your customers quality perception and decide if a new approach needed.
Steve Mossige- Dallas, Texas
2002
Thanks, Steve. I, too, advise Greg the same way -- that he should give strong consideration to powder coating. But I don't know quite what you mean by 'addressing your customers quality perception' though. I don't think either plating or powder coating has a "bad rep" for quality, whereas for any particular application one of the two approaches (plating vs. powder coating) is objectively better than the other. Please clarify, and thanks again.
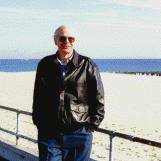
Ted Mooney, P.E.
Striving to live Aloha
finishing.com - Pine Beach, New Jersey
2002
2002
Consider switching to galvanized material, stripping the zinc from areas to be welded, cleaning the welds and adjacent areas, and then brush electroplating zinc. You could also plate edges of punched holes, attachments, etc. The stripping could be done either electrolytically by brush or by brute force with acid. Figure out the areas involved, then consult with a vendor (use the 'Chemicals' button, then search for 'brush plating'). The capital, space and amount of regulated chemicals will be far less than for a full-blown plating line.
Ken Vlach [deceased]- Goleta, California

Rest in peace, Ken. Thank you for your hard work which the finishing world, and we at finishing.com, continue to benefit from.
Q, A, or Comment on THIS thread -or- Start a NEW Thread