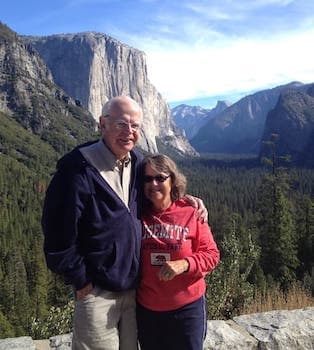
Curated with aloha by
Ted Mooney, P.E. RET
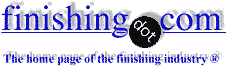
The authoritative public forum
for Metal Finishing 1989-2025
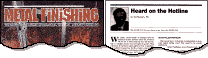
-----
Protection of metal parts against corrosion working on direct flame
2002
We have some parts made of Stainless Steel which serve only as fixtures with no mechanical stress action during process. These parts are all day working on open flame of natural gas (some content of sulfur, maybe 1%) and temperature should be around 800 Centigrade (1450 F). Stainless Steel is 304 although recommended is 310. However when using any of this, the parts last only from 3 to 4 months in use. They are like consumed from the upper edge. The parts are small tubes of 3/8" with a simple fixture on top and the flame is directed to the edge where the fixture is. We would like to increase the life of such parts and if possible using a material easier to machine like cold rolled. We already tried with cold rolled and sputtered with S.Steel 330 and on top another layer of Hastelloy C276, but result was not successful. Is there a solution for this? I have equipment for sputtering and I would like to try a solution with it. I prefer also to use the parts in iron instead of actual S.Steel 304 because I would reduce production costs.
Thanks,
Julio Salinas- Mexico City, Mexico
Many years ago, when I was in my first job as an engineer I was very surprised when an old experienced foreman said to me that cast iron couldn't be melt with an acetylene torch. I couldn't believe him until he proved it. Cheap, simple and old but frequently forgotten alternative. Certainly not everlasting but it used to work fine for burners in old boilers and "calentones". Another alternative could be the coating with vitrified enamel or porcelain.
Guillermo MarrufoMonterrey, NL, Mexico
2002
The damage is caused by H2S-containing gas corrosion. To combat the process one should use high Cr or/and Al steels ar cast iron. I would recommend you also to apply the following procedure: sputter Ni-Cr layer for 20-40 mkm firstly and than second layer- Al spraying for 80-150 mkm. Annealing for about 900-1000 deg.C is highly recommended. The purpose of the second layer is to produce Al2O3 shielding layer and the former is to prevent the layer from diffusion during exposure to flame.
Andrey Igolkin- St.Petersburg, Russia
2002
Q, A, or Comment on THIS thread -or- Start a NEW Thread