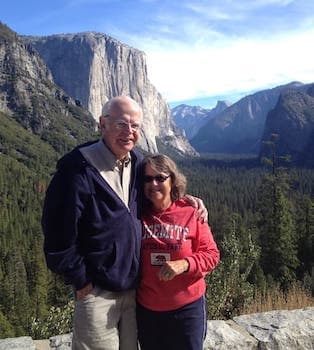
Curated with aloha by
Ted Mooney, P.E. RET
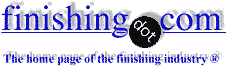
The authoritative public forum
for Metal Finishing 1989-2025
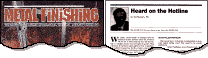
-----
Electrolytic action causing premature failure of BZP bolts
My company installs irrigation systems for golf courses. As part of these systems a bolt-on saddle clamp is used to provide a connection point for each sprinkler. At certain sites, we have experienced problems with the steel bolts securing the saddle clamps being eroded until they become so reduced in diameter that the pressure in the pipework causes the bolt to fail completely. The bolts concerned are of mild steel construction with an BZP (zinc plated) finish. This problem has only occurred at sites which appear to have aggressive soil types. It is my theory that the erosion has been caused by electrolytic action. This is based on the fact that the bolts are eroded away (sometimes to a 1/10 of original diameter!) as opposed to corroded. In an attempt to cure the problem, the bolts have been replaced with one made of 304 grade stainless steel. We have however experienced a further problem in that the stainless steel nuts frequently bind when the bolts are being tightened. I have been told that this is caused by 'galling'. What al! ternatives are available? One specialist suggested that using a stainless steel nut of a different grade to the bolt will prevent galling. Another has suggested using a BZP nut with the stainless bolt. I would welcome any comment as to my theory for the original failure and for any solution to the galling problem.
Adrian Abbott- Salisbury, Wiltshire, UK
2002
First of two simultaneous responses --
I certainly would not challenge the theory that some sites are more corrosive than others. But the theory about galvanic corrosion is probably weak. In fact, the zinc plating is intended to galvanically corrode to protect the underlying steel.
But the thing is, if the pipe is steel or iron (you didn't specify) or if the whole saddle is steel or iron, the small amount of zinc plated onto the bolt and nut can't survive long. If you specified galvanized hardware, the zinc would be several times thicker and would last much longer. You could also perhaps protect the pipe with zinc anodes.
The stainless hardware will not corrode. However, I would be concerned about it causing galvanic corrosion in the saddle areas immediately around it. Galling is a problem with stainless steel and the solutions are not always easy. Silver plating the nuts is one solution. Another possibility is nitronic stainless steel which is designed to not gall, but I don't know how corrosion resistant that is since I am not aware of applications where it is buried.
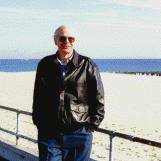
Ted Mooney, P.E.
Striving to live Aloha
finishing.com - Pine Beach, New Jersey
2002
Second of two simultaneous responses --
You are correct in believing that the problem is caused by electrolytic corrosion. The steel bolts must be in contact with a different metal. You did not mention what it is, but it must be a more noble metal. Electroless nickel plated bolts and nuts will not gall and will likely last a great deal longer.
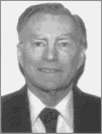
Don Baudrand
Consultant - Poulsbo, Washington
(Don is co-author of "Plating on Plastics" [on Amazon or AbeBooks affil links]
and "Plating ABS Plastics" [on Amazon or eBay or AbeBooks affil links])
2002
In addition to either galvanizing or E-nickel you may want to look into organic coatings. Today's organic coatings are often very competatively priced with most platings and offer greater corrosion resistance and many different lubricity levels that will counter-act the galling you are experiencing.
David J Wolf- Painesville, Ohio
2002
2003
WITH REFERENCE TO YOUR PROBLEMS WE HAVE 30 YEARS EXPERIENCE OF STAINLESS STEEL INSTALLATIONS.
OUR EXPERIENCE IS:
1 USE 304 A4 BOLTS WITH A2 NUTS
2 IF YOU USE NYLOCK NUTS THE GALLING BECOMES WORSE
3 IN ALL applicationS US A MOLY KOTE TYPE OR ANTI SCUFFING TYPE GREASE, (COMMON SUPPLIER ROCOL). ON ALL BOLTS BEFORE FITTING THE NUT AND TIGHTENING
4 DO NOT TRY TO PULL ITEMS TOGETHER WITH THE NUT ONLY TIGHTEN ITEMS TOGETHER
- GLASTOBURY, SOMERSET, ENGLAND
Q, A, or Comment on THIS thread -or- Start a NEW Thread