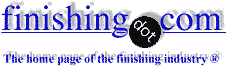
-----
Sigma phase and corrosion of a 309Mol buffer and 316L overlay
What would be the purpose of welding a 316L overlay to a 309Mol buffer weld which is then welded to carbon steel.
I understand why the 309Mol is welded to the carbon steel i.e less dissolution due to higher chromium but I do not understand why 316 would be required to be welded to the 309 Mol buffer. The chemistry is relatively the same and there is nothing to really go by on the ferrite content. Surely the corrosion resistance must be the same. Also does anybody know if sigma phase is more likely to form in a sample of 309Mol (higher chromium) than 316L?
Mat Hogen- Melbourne
2002
2002
The 316L overlay is less costly than the more alloyed 309. Also, while 309Mol may generally offer better corrosion resistance than 316, in specific applications, e.g., urea manufacture, it is less resistant due to its greater ferrite content [Lincoln Electric].
The 309Mol is necessary as a buffer between the carbon steel and the 316L in order to produce a weld metal with a Ferrite Number of at least 4-5 to avoid cracking. The FN for pure 309Mol and 316L are 23 and 3, respectively, using the program at http://engm01.ms.ornl.gov/FNPLots.HTML Diluting the Cr, Ni & Mo proportionally by welding to a plain carbon steel reduces the FN.
Finally, I don't believe that sigma phase is a problem given the high nickel concentration, but here is a source with a sophisticated program for a definitive answer: http://www.npl.co.uk/npl/cmmt/mtdata/demfal.html
Ken Vlach [deceased]- Goleta, California

Rest in peace, Ken. Thank you for your hard work which the finishing world, and we at finishing.com, continue to benefit from.
Q, A, or Comment on THIS thread -or- Start a NEW Thread