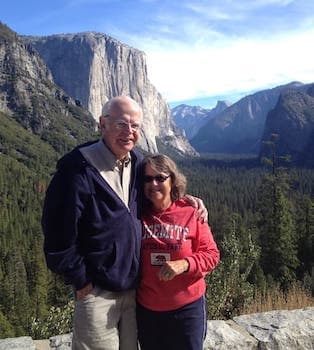
Curated with aloha by
Ted Mooney, P.E. RET
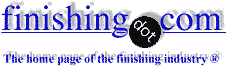
The authoritative public forum
for Metal Finishing 1989-2025
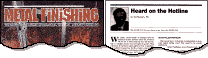
-----
Phosphate Free Pretreatment Process
My company is considering discontinuing the use of iron phosphating during the pretreatment process. We have a five stage cleaning process that consist of an alkaline cleaner (zone 1), iron phosphating (zone 3), alkaline sealer (zone 5), and two fresh water rinse stages (zone 2&4). We use an hybrid epoxy powder to coat our parts. Our substrate is cold rolled steel but we are also considering hot rolled steel. Are there any other companies that do not use any type of phosphating process before powder coating hot or cold rolled steel? If so, what kind of long term (10 yrs+) results have you received? How many salt spray hours do you test to and what are the results?
Lennie D. Moore- Stanley, N.C., USA
2002
I'm not sure why you want to eliminate the phosphate ($$?), but I think that you will see a marked decrease in adhesion and salt spray performance. The phosphate provides a couple of major advantages over bare steel.
1) It creates an amorphous surface finish that has more surface area for the coating to adhere to. This will bear out in a cross hatch test quite readily.
2) It creates a protective layer in/over the steel to resist the attack of the salt spray test (or real world exposure). In a scribe test, the creepage from the score lines in a bare test panel will grow much faster, because there will be no phosphate to retard the growth of corrosion.
Overall, I think maybe you should look at how your current vendor is satisfying your needs (and give him/her a chance to improve your process) and then look at other vendors if a suitable improvement program isn't found.
Dan Brewerchemical process supplier - Gurnee, Illinois
2002
In light of Dan's response. We are trying to reduce cost. We know from previous trials that we are able to coat parts and still exceed our salt spray expectations. We are only seeking information about some hands-on experience that someone may have with powder coating steels (preferably hot rolled), without utilizing a phosphating stage during the pretreatment process. We are quite satisfied with our present pretreatment and powder coating suppliers. We simply need more information to validate our results.
Lennie D. Moore- Stanley, North Carolina
2002
2004
There is a phosphate free conversion coating that, if used under the proper conditions, will out perform iron phosphate coatings.
It is a nano-ceramic coating that operates at ambient temperature. We have used it for over a year, and we are able to exceed our salt spray requirement of 500 hrs. We do not use a sealer with this product. The bath is at a concentration level of 2.5% - 5%, with a pH level of 4.5 - 5.2. There are a few drawbacks to the product:
1. It costs more than phosphate.
2. You need a Stainless Steel wetted system to use the product.
3. You will need to keep the bath temperature below 110 degrees.
4. The bath life ranges from 1 to 6 weeks, and then you will need to dump and replenish the tank. this is determined by how much square footage is processed.
5. The product requires a lot more attention than iron phosphate. You can't fill the tank and forget it for hours on end, as you can with phosphate.
But....If you need to get away from phosphate, this product will work. Any cost savings you realize from not heating the bath, and from not needing any waste treatment system (the product can be put directly to drain), will be spent on chemicals. I suspect as more suppliers offer the product, the costs will come down.
kelly hunter- Greenville, Michigan
2007
LARGEST AUTOMOBILE COMPANY HAVING 4 BIG PAINT SHOP AND USING ZINC PHOSPHATE PRETREATMENT BEFORE CATHODIC ELECTRODEPOSITION.
THE BY-PODUCT GENERATED THROUGH THE PHOSPHATE PROCESS IS SLUDGE WHICH IS ENVIRONMENTALLY HAZARDOUS WASTE.
IS THERE ANY PHOSPHATE-FREE PRETREATMENT WHICH WILL HAVE BETTER compatibILITY WITH CATHODIC ELECTRODEPOSITED PRIMERS.
pL BRIEF THE ADVANTAGES OF USING THIS SYSTEM
- PUNE, MAHARASHTRA, INDIA
Q, A, or Comment on THIS thread -or- Start a NEW Thread