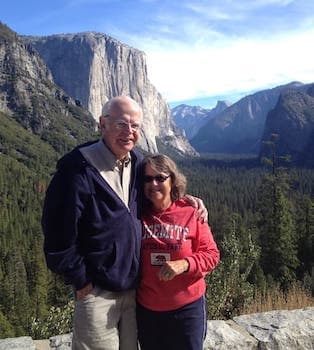
Curated with aloha by
Ted Mooney, P.E. RET
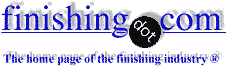
The authoritative public forum
for Metal Finishing 1989-2025
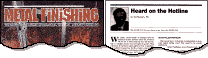
-----
TRD (Thermo-Reactive Diffusion) CARBIDE COATING
Q. I heard about TRD Carbide Coating onto tools in cold forging and hot forging I would like to know if anybody used it on steel and what was the outcome?
Thank you,
- Fort Worth, Texas
2002
A. You are asking if anyone put them on steel. For what purpose? Is the steel an end product or part of a die or part of a forging tool?
TRD coatings are Vanadium Carbide. I have heard of this coating being tried on die casting dies to increase the lifetime of the dies. The dies are typically made of H13 steel, so the coatings have been deposited on steel. If you are interested in this more I know that Dr. Rajiv Shivpuri in the Dept of Industrial and Systems Engineering, Ohio State University has done the testing of these coatings.
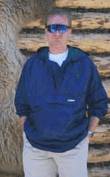
John Davis
- Berthoud, Colorado, USA
2002
A. My Company is a representative of the TRD Process. We have worked with this process since the early 1990's.
The process works very well on a carbide material as well as most tool steels and some hot, or cold roll. Like most coatings the better the substrate the better your tool.
This is an 1800 degree process so please keep in mind that there can be some drawback to the process.
Here is the short: TRD will not chip, peel, or rust; it is over twice the hardness of carbide -- ideal for fighting wear problems.
Tool & Die Supplier - Indianapolis, Indiana, USA
2005
A. I guess the TRD would be good if tolerance is not an issue. I have the treatment done on tool steels, stainless steel and carbide. Titanium is diffused into the substrate, bringing the surface hardness to 73-75 Rc, even on 316 SS. This is all accomplished on finished tools, this process is accomplished under tempering temperatures.
Terry Fry- Wheeling Illinois USA
February 23, 2011
Q, A, or Comment on THIS thread -or- Start a NEW Thread