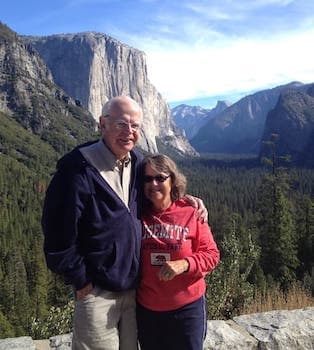
Curated with aloha by
Ted Mooney, P.E. RET
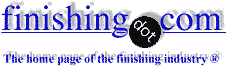
The authoritative public forum
for Metal Finishing 1989-2025
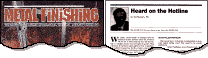
-----
Powder Coat Adhesion Problem - Steel Flanges/Tube
2002
I was hoping you could provide some advice on an issue we are having. I am a M.E. at a tube fabricator. We are currently manufacturing a new axle, which is a straight tube with two end flanges welded on the ends. After weld, we run through a standard phosphate system and then powder coat. Our bake time is 35-45 minutes at a temp. of 400 degrees. We perform an
MEK / methyl ethyl ketone rub and cross-hatch test. The only area that these tests fail are on the inside faces of both flanges. The paint adheres on the outside faces of the flanges, the tube, and the bracket and gusset welded on the tube. Yet, the paint is chipping and not adhering to the inside faces of the flanges. We have tried longer bake times, lighter coating (1-2 mils) and different pre-treat processes. Does anyone have any ideas on what we are doing wrong or what we can try to fix this problem?
Thanks,
- Oberlin, Ohio
Hi Keith,
Are your flanges water-break-free after cleaning? If not, then that is the likely cause of your adhesion problem. Are all of the pretreatment tanks being run within specification? Are the rinse tanks in the pretreatment line being overflowed adequately and being dumped regularly? Problems in these areas of the line can result in adhesion problems.
- Naperville, Illinois
2002
Hi Keith,
If the coating in these areas is failing a MEK test it is not curing.
What type of oven do you have? If you are curing in an IR oven the inside edges may be being shadowed from the IR hence not curing properly. I would suggest running a Datapac or similar oven temperature profile equipment through your oven, attaching probes all along the axle especially on the inside edges of your flanges.
Adhesion is also connected to cure but another possibility is the residue from the weld. You must ensure this is totally removed before phosphating and application.
Hope this helps,
- North Lincolnshire
2002
It seems that higher mass areas of the substrate are not curing, thus an infra-red booster may be advisable providing that your pretreatment is operating properly.
Synthetic lubricants may also cause problems proper temperature of the pretreatment process may be required (over 150F degrees) to provide a water break free surface.
- Dallas, Texas
2002
It would seem to me that you have "oil burn" which is common after welding. Standard phosphate will not usually remove this. While I understand that you may normally be running welded components which don't exhibit the same problems it may simply be that the area in question is "shielded" from your washer nozzles.
You could try washing these areas by hand to see if this works. The next step is to have the part pickled to remove the burnt in/hardened oil.
- Tupelo, Mississippi
2005
Q, A, or Comment on THIS thread -or- Start a NEW Thread