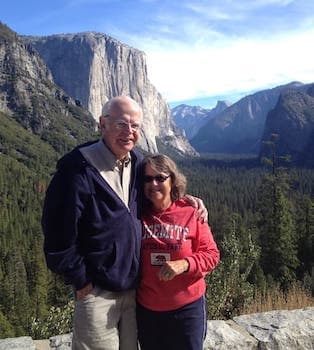
Curated with aloha by
Ted Mooney, P.E. RET
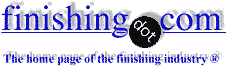
The authoritative public forum
for Metal Finishing 1989-2025
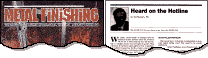
-----
Pitting in hard chrome plated steel
Q. Hello All,
Looking for some guidance on possible causes of some localized pitting I am seeing on hard chrome plated steel roll. The pitting in the photo was found after about six weeks of service (no pitting seen when the roll was installed). The roll is the bottom roll of a set that perform a press function in an abrasive web application (roofing). The pitting is just inside the wear area of the roll, and there are no other instances of pitting on this roll or the corresponding top roll. My finishing vendor has suggested a foreign object may have passed through, but my production dept. isn't buying that.
I am wondering what other causes there could be for what appears to be a distinct pattern? Looking for experienced and unbiased opinions. Thank you!
Reliability Engineer - Peachtree City, Georgia
October 15, 2021
A. My observation is dents/pits are pregrinding due to maybe localized rusting or prolonged storage.
Plating is observed in the pits; also the Radius edge of the pits are rounded and plating observed.
Technical Consultant for Hard Chrome Plating - Belgaum KARNATAKA INDIA
Q. Hello Sir.
I would like to ask you for some information.
I want chrome plate c45 steel or carbon steel 1045.
How you are activating this metal?
Is the activation different from other steels?
The pieces I have are directly from a CNC machine.
Thanks in advance....
Shop employee - Athens
November 17, 2021
by Robert K. Guffie
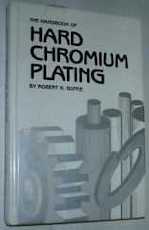
on AbeBooks
(rarely)
or eBay
(rarely)
or Amazon
(affil links)
A. Hi Konstantinos. When hard chrome plating, it seems more common for people to call the prep step an "etch" rather than an "activator". Guffie suggests 15-30 seconds in chromic acid.
If your chrome plating process is fluoride-free, the etch can be done with reverse current of 1 ASF in the plating tank, although some people feel that plating tanks should not be used as etch tanks.
Luck & Regards,
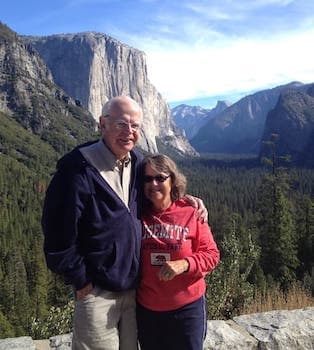
Ted Mooney, P.E. RET
Striving to live Aloha
finishing.com - Pine Beach, New Jersey
⇩ Related postings, oldest first ⇩
Q. Our customers have encountered pitting in hard chrome plated, medium carbon steel bars. Pits are scattered in a 1 1/4 to 1 1/2 inch band along a 2.5" round bar. Cross section of the defect shows it to be spherical, extending into the metal under the chrome. The pit is smaller at the top than in the body of the pit.
What could cause this? Porosity in the steel has been ruled out due to elongation from the rolling reduction.
St. Paul, Minnesota
1998
A. Sounds like a gas pit, from your description. Search (using the search engine at top of this page) these letters from www.finishing.com/letters under hard chrome or chrome to find references for troubleshooting of chromium plating solutions; search for Meng and Guffie, I believe.


Tom Pullizzi
Falls Township, Pennsylvania
A. After listening to a talk on substrate related defects by Atotech's Alan Jones a couple of times now, I lean towards thinking that the easiest to fix cause of pitting is dirty emery cloth. Throw every piece of sandpaper and sanding cloth on your machinist's desk away; buy fresh; and let us know what happens :-)
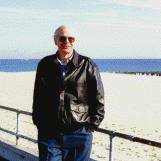
Ted Mooney, P.E.
Striving to live Aloha
finishing.com - Pine Beach, New Jersey
A. It sounds to me like the pits are due to corrosion. The undercut shape is the classic shape for pitting corrosion. Are the pits found immediately after plating or after some time in service. Pitting like this is often due to corrosion in aqueous chlorides. Pits can initiate at cracks and porosity in the chromium if there is no nickel plating under the chromium.
If the band is longitudinal, it could be corrosion along the bottom of the bar while laying on a wet surface. Further analysis, such as SEM/EDS, to see what chemical contamination may be inside the pits may help to find the root cause.
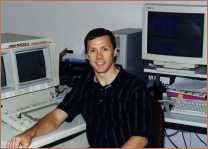
Larry Hanke
Minneapolis, Minnesota
Pitting is only on top surface of chrome plated parts
Q. I had previously posted a message about pitting on hard chrome plated C1045 carbon steel. I have recently learned that the band of pits is always on the top of the bar as it would sit in the plating tank.
Does this suggest anything? Why would the top surface be more likely to pit in a commercial bath.
Thanks
steel, St. Paul, Minnesota
1998
A. Dear Dennis ,
I suggest that the most probable cause of the pitting is gas pits, and this is being caused by insufficient solution agitation around the workpiece , if you are running a proprietary bath you will find the suppliers have a mountain of recent information about filtration and its use in agitation of chrome baths and the dramatic effects this is having on both hard & decorative chrome solutions.
Best regards

John Tenison - Woods
- Victoria Australia
Steel bars can be chrome plated vertically despite sulfur stringers -- but not horizontally
Q. My company is UK producer of hard chrome plated steel bars for use in hydraulic cylinder ram rod production. Over the last 15 years we have plated bar in horizontal plane.
During this time we have encountered pitting along the top section of the bar for it's length. The pits are 0.01/0.05mm in diameter and are not through to the base material, they are plated to the bottom of the pit. The pit is smooth and the condition of the as plated bar is bright and very smooth. The deposit of HEEF 25 is .0008"-.0012". The solution balance is perfect in accordance with Atotech recommendations. There is low Trivalent and almost zero Iron. Total oxides are less than 5 g/l. chrome to sulphate ratio is 100:1. Micro cracking is good. Temperature is 54 - 58 °C.
Our material is polished to the highest possible standards achieving 0.07 Ra < 5 CLA. Polishing is carried out using 4-head linishing machine and final polishing with 800 grit silicon belts.
Cleaning and etching is carried out in special cleaning tanks and not in the plating solution.
Recently we have two batches of material from different suppliers (2-1/4" dia.) in a 20MnV6 material (modified EN14 or 1020 medium carbon with vanadium). One batch pitted while the other did not. Both batches were plated at the same time in the same tanks (20 tonnes over two days)
Our research has concluded that the pitting problem is due to material having sulfur stringers causing excessive gassing at the upper most surface. We have found this problem on several casts of material over the last 15 years and no chemical or mechanical changes in our process can overcome this problem. Atotech UK have worked with us over the years and are also unable to find a chemistry solution to the problem.
We are convinced that the problem cannot be overcome when the bars are plated in the horizontal plane but will be perfect in the vertical!
If anyone is able to suggest another cause or offer a practical solution I will be pleased to hear from you.
- UK
2000
Q. I use a dilute bath for hard chrome plating on Nickel, not iron or steel. 33 oz / gal of Chromium and .33 oz / per gallon catalyst (sulfuric acid). My own readings tell me I am close to where I should be. I am getting pitting on my chrome. Any suggestions?
Dave KiminkiPlating shop - Ft. Worth, Texas
March 31, 2011
Filtering hard chrome plating solution to stop pitting
Q. We have had some pitting problems in our Hard Chrome deposits which we feel are being caused by tiny pieces of sediment or other adhering to the surface of the the part during entry into the bath and creating a pit in the chrome plate. We are happy that our preplate procedure is correct and there are no defects on the surface before plating. Although we ensure that the surface of the bath is kept free of any floating material or other debris, is it possible that tiny particles could adhere to the part below solution level?
If this is the case, how might we filter the bath bearing in mind that it is a 10 foot deep 7000 litre plating solution?
The current being applied to these parts is 1500 Amps.
Aerospace - Ireland
May 15, 2014
A. This seems to be caused by Hydrogen gas.
Hydrogen gas is given off at the part being plated, as a result of the hydrolysis of water in the bath. As these hydrogen bubbles evolve, they must dislodge themselves from the plated surface. If they do not dislodge, the gas bubble serves as a barrier to plating, because chromium ions in solution cannot come in contact with the part. The shape of a pit can help to determine its cause. If the pit is shaped like a tear drop, hydrogen gas pitting is the likely cause. Increasing the electrolyte solution flow past the surface of the part may help to eliminate hydrogen gas pitting. In some situations, this can be accomplished by pumping solution.
KYB America's Corp "Production Engineering" - Franklin, Indiana
May 2, 2016
Q. We are experiencing a pit like appearance on hard chrome surface on piston cylinders after only a few weeks operation. The chrome layer was done in 3 layers with total 50 micron thickness, what is the probable cause for this defect?
Andfinnur Thordarson- RVK, Iceland
April 4, 2018
A. Could you describe the 3 layer process you are applying the hard chrome? I have a strong idea what this may be.
We had a cylinder that someone needed 200 µm on and originally thought to prevent cracks/deformation we would do it in runs of 4, but got similar results to what you are describing, our deduction was that this was something to do with hydrogen release after re-immersion. In that case we developed a special jigging system and agitator to get customer requirements. The job was far from a smooth finish but they were thrilled!
50 µm is hardly thick in hard chrome terms, have you considered leaving it in the bath? If not this has the part been pickled prior to plating?
- Bradford, West Yorkshire
A. Hi,
What I can see by the photo, it looks like the chrome has pinholes or pits which are going into the base material.
You need to check the pretreatment steps before chrome.
Maybe the chrome solution has iron and copper contamination. Also check the trivalent chrome.
Regards
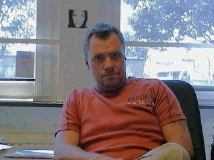
Anders Sundman
4th Generation Surface Engineering
Consultant - Arvika,
Sweden
Q. Thanks for your comments.
The cylinder was pickled prior to plating but the producer doesn't want to reveal the exact procedure. He claims that the reason is too thin Cr film. We have had quite good experience with 50 micron Cr film before at same conditions though.
The holes you see on the pictures are, strictly speaking, not holes. The surface is Cr but cracks are circular and the middle (which appears to be rust) is Cr film. The rust is apparently diffusing from these circular cracks up to the surface.
- Reykjavik, Iceland
? Hi Andfinnur. Just to be clear: The producer claims that this particular cylinder was plated to 50 microns, and you have checked and found that to be correct?
What environment have the cylinders been in for this few weeks of operation? For example, these cylinders are on earth moving equipment that you built and sold, or what? Thanks.
Regards,
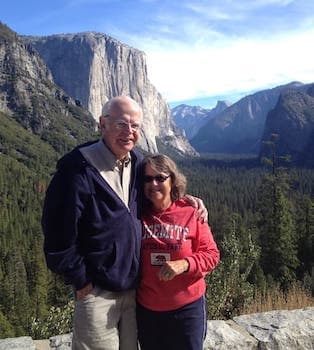
Ted Mooney, P.E. RET
Striving to live Aloha
finishing.com - Pine Beach, New Jersey
Q. Hi Ted
This occurred only after a few months in operation; the environment during that period was typically -5 to +5 °C (winter/autumn, wet dry season). The hard chromium is on stainless steel hydraulic cylinders. The Cr film was measured from 60-90 micrometers on a few cylinders where this occurred.
regards, Andfinnur
- Reykjavik, Iceland
A. Hi Andfinnur. Although you've told us the season, I am still not understanding the application. If it is earth moving equipment, for example, it sounds quite possible that it was used in environmental cleanup and exposed to acid fumes or liquids. It seems hard to believe that this was a chrome plated cylinder of conventional design exposed only to the natural environment for a few weeks or months (although chromium is slightly cathodic to some series 4xx stainless steels, so can cause rust blooms if there are pinholes, especially if used in salt water).
I don't have sufficient experience to suggest causes other than exposure to acid or pinholes plus saltwater. It may be just this photo, or prep you did for your analysis, but I'm also surprised with the general "matte" look to the chrome; usually hydraulic cylinder use leaves pistons lightly oiled and highly polished. The photo looks like the piston has a "flat" machined into it ... is that just an optical illusion from the lighting?
Hopefully, Oliver or Anders or another hands-on chrome plater will respond further.
Regards,
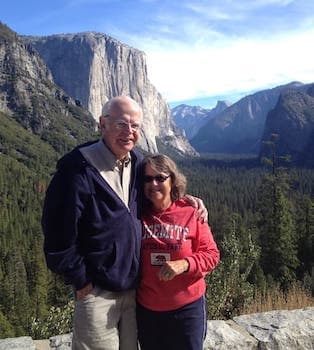
Ted Mooney, P.E. RET
Striving to live Aloha
finishing.com - Pine Beach, New Jersey
A. It is normal for rust to come thru thin porous chrome electroplate.
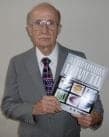
Robert H Probert
Robert H Probert Technical Services

Garner, North Carolina
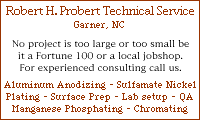
A. Hi Andfinnur,
I agree with Ted, this seems to be strange with that short period of time, and as you mentioned that the material is stainless steel, the rusting seems to be very high. We had that situation with a piston rod that used in a ship exposed directly to the salty water and sun, normal C45 material with 50 microns plating thickness. The rusting was only on the part that left outside, just below the shaft. The problem there was, they never oiled or protected the outer part. But that was a carbon material.
This will be not likely, but is there a chance that they welded somewhere near the rod, and some welding burrs burned the chrome plating and rusted the area? There seems to be still some particles over the rod and on the second picture, rusting area on right-top, it seems like a welding burr. Just an opinion.
EKS Hard Chrome Plating - Istanbul, Turkey
Hard Chrome Plating Pits - Base Material Unaffected
Q. Hello, We are examining a shaft that is hard chrome plated and exhibiting pitting throughout. The chrome plating shows pitting where rubber seals attach to the shaft as the shaft moves back and forth, the most extensive pitting is where the seals settle when the shaft is not moving. Cross-sections show there is absolutely no damage to the base material and good adhesion of the plating to the substrate, the pits are purely in the plating. What could cause the chrome plating to be attacked but not the stainless steel below it? Or is this possibly a fretting situation where the seals are ripping parts of the chrome plating out?
The environment is crude oil and air at different times of service. Any help or advice would be greatly appreciated!
- Arizona
November 19, 2019
Pitting on hard chrome plated shaft
Q. We observed red and white spots on hard chrome plated shaft dia. 70 mm length 2 meters. These spots observed in cluster or only one spot. It's observed at one or two locations only and not on entire shaft. Material of shaft is En19 with hardness 28 HRC. We maintain grinding finish Ra0.4 max before plating. We carry out flash chrome plating of 20 microns.
Some analysis results are as follows.
In all the samples, the micro sectional images indicate the presence of cavity in the base surface underneath of the chrome layer.
The SEM-EDX spectrum at the defective portion indicates the presence of external elements other than Chromium(Cr) like Sodium, Calcium, Zinc, Magnesium and Chloride
shop employee - Mumbai, Maharashtra, India
December 9, 2019
A. Hi,
I think it's the Iron content in your chrome solution.
Check also the trivalent chromium by an analysis.
Regards,
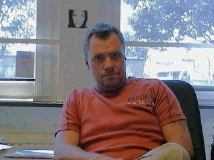
Anders Sundman
4th Generation Surface Engineering
Consultant - Arvika,
Sweden
Q. We have a Automatic Horizontal hard chrome plating unit for bar plating,
We use Atotech HEEF-25. Chemistry.
We are facing pitting ONLY ON THE TOP SURFACE. otherwise plating is good.
We have tried many combinations to solve this problem, our bath chemistry is well balanced, and maintained regularly.
We have degreasing done at 60 °C
Etching is done in separate chromic acid tank. We experimented with zero current for etching, still this issue in not sorted.
We plate around 25-35 microns thickness, our chromic acid @ 306 gms/lit.
Trivalent chrome @ 4.8 gms/lit
Catalyst @ 45.83 gms/litr.sulfuric acid @ 4.95 gms/litr. Fe @ 2487ppm.
- Belgaum Karnataka India
April 26, 2021
A. Hi Mahendra. Thank you the insightful help you have offered others in this forum. I'm sure we all would like to return the favor. However, what I am not understanding is how we can call something a "top surface" when you are doing horizontal plating of a shaft/roller which is presumably rotating during plating such that there is no "top" surface. What am I misunderstanding please?
Luck & Regards,
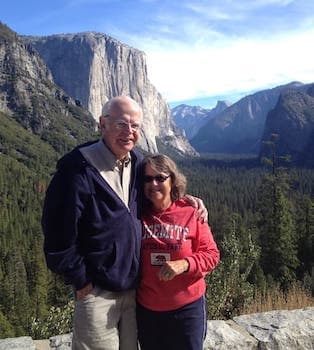
Ted Mooney, P.E. RET
Striving to live Aloha
finishing.com - Pine Beach, New Jersey
These bars do not rotate, they are pushed through
By a geared motor.
- Belgaum Karnataka India
A. If you are not rotating, as I interpret your message, then possibly the catalyst is settling out on the top surface and causing roughness or pitting.
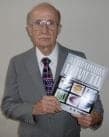
Robert H Probert
Robert H Probert Technical Services

Garner, North Carolina
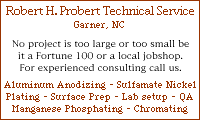
Thank you sir, for your inputs
We will try oil free air agitation.
- Belgaum Karnataka India [returning]
A. Hi, I have seen this shaft before which is used on car gear box. We are plating it with electroless nickel, and there is also similar pinhole of pit on surface when 10X visual.
Finally we found there is a small defect on the material surface before plating., and the same pits occur after plating at the same position.
- China
October 24, 2022
Q, A, or Comment on THIS thread -or- Start a NEW Thread