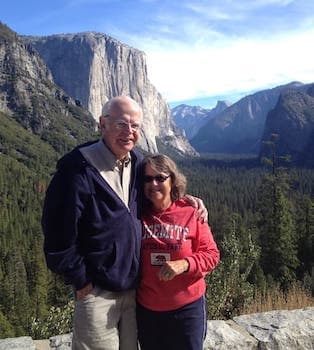
Curated with aloha by
Ted Mooney, P.E. RET
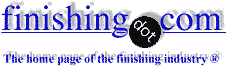
The authoritative public forum
for Metal Finishing 1989-2025
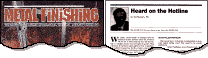
Thread 179/20
Cracking pattern in old brass
Crazed cracking pattern in 100 Year old clock base. The base is 7" dia. x 2" high and probably "spin formed". Wall thickness 3/32". Structurally, the base is strong enough to continue, but is there some means of filling the cracks to minimize their appearance when the brass base is polished? Perhaps a low melt point brass filler? Or a brass powder filled epoxy? The clock is a Tiffany Never Wind made in Buffalo NY about 1901.
Ken Carlson- Kenton, Ohio, USA
2002
publicly reply to Ken Carlson
Are you positive that the parent metal is cracked? Sounds like it could possibly be that the "crazing" you are seeing is the protective finish that was applied years ago has finally begun to deteriorate. Try using a mild solvent in an inconspicuous are to see if the finish (and crazing) will come off. Brass needs a top coat of some type of clear to prevent tarnishing.
Good luck.
Bill Miller- Shinnston, West Virginia, USA
2002
publicly reply to Bill Miller
2006
The base of your clock was spun and most likely was not annealed. As is typical of this type of clock, the brass is very stressed and is vulnerable to cracking as a result of air borne chemicals (even though the surface is protected by a coating, it has deteriorated and its ability to protect has been compromised), or direct attack by chemicals used to polish the brass or to clean it (
Brasso
⇦ this on
eBay
or
Amazon [affil links] contains an ammonia
⇦ this on
eBay or
Amazon [affil links] substance and many aqueous cleaning solutions contain an ammonia substance or related chemical).
Exposure of stressed brass to ammonia or its chemical relatives will introduce Stress Corrosion Cracking (SCC). Attempts to plate over the cracks in order to hide them can also exacerbate the cracking unless the stresses have been relieved already by the previous cracking to a level below the critical point.
Polish with a mixture of fine chalk dust and a hydrocarbon such as Stoddard's Solvent and rinse thoroughly with Stoddards to remove the chalk. Then coat with a suitable lacquer.
Clock Conservator - Boxborough, Massachusetts
publicly reply to Jim Moss
Q, A, or Comment on THIS thread -or- Start a NEW Thread