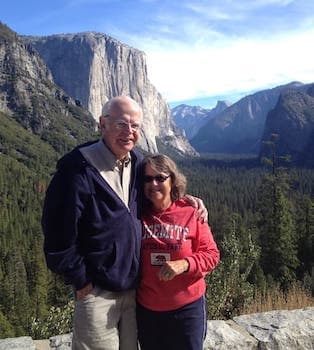
Curated with aloha by
Ted Mooney, P.E. RET
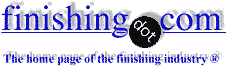
The authoritative public forum
for Metal Finishing 1989-2025
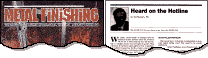
-----
Phosphate Coating Weight Specification & Control

Q. Dear sir,
We are using cold-type zinc phosphating and we are facing coating weight issue.
Coating weight is normally 4-5.5 gms/m2 and in this range mechanical tests are failing on sheet metal.
So we would require 1.5 to 2 gm/sq.m.
Total acid value is 30 ml
F.acid - 0.8
Accelerator - 3 - 4 ml
Conditioner concentration 4 - 5 ml.
Dipping time - 3 mins.
I have doubled the conditioner concentration of the bath volume and no change in coating weight.
Please share any method to find titanium content in activation and how to calculate the coating weight weight of the conditioner.
Please support to overcome this issue.
Thank you.
Sr.Engineer - Tamilnadu, India
December 13, 2021
A. Dear Mr Sridhar,
The coating weight is not only controlled by the surface activation. The formulation of Zinc Phosphate solution also play a major role in providing the desired coating weight. May use tri-cationic formulations with grain refiners to solve the problem. This along with a good titanium based surface activator may give you the desired results.
- MUMBAI
November 15, 2022
A. Hello Sridhar,
As Mr. Bhavesh said, the formulation of the bath is central for coat formation, so for certain zinc contesnt, there will be certain coating weight.
You can try making the FA value higher to make TA/FA ratio lower. This makes more compact finishes, so coating weight goes down a little. You can try it but the main contributor to the coating weight will be the formula.
Best of luck!
- Cañuelas, Buenos Aires, Argentina
January 3, 2023
⇩ Related postings, oldest first ⇩
Q. Dear sirs: I read about phosphate coating. Is there any specification on the coating weights so that any paint will adhere well to that phosphate coated surface.
Please suggest.
Sivakumar Balasubramanian- Hesston, Kansas
2002
A. I suggest you will look at TT-C-490 [from DLA] military standard. Anyhow as a rule of thumb and as appears in the literature for Zinc Phosphate the coating weight are as follow: For Spray application coating weight range from 1.5 - 3.5 grams per square meter For dip application coating weight range from 2 - 5 grams per square meter.
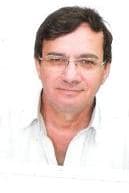
Yehuda Blau
YB Plating Engineering and Quality - Haifa Israel
A. INDIAN STANDARD SPECIFICATION IS: 3618:1966 GIVES COATING WEIGHTS FOR FOUR STANDARDS, VARYING FROM
1. CLASS D: extra light weight.IRON, AND ZINC PHOSPHATE COATING weight 03 to 1.1 g/sq. meter.
2. CLASS C (light weight) ZINC PHOSPHATE COATING FROM 1.1 to 4.3 g/ sq meter of treated surface.
3. CLASS B (mEDIUM WEIGHT) ZINC PHOSPHATE COATING HAVING A MINIMUM OF 4.3 g/sq meter.
4. CLASS A2. (Heavy Weight). processes giving coatings that consist essentially of zinc phosphates and have a weight not less than 7.5 g/ sq meter of treated surface. Normally used for similar purpose as A1. where a good degree of protection.
5. CLASS A1. (Heavy Weight) processes giving coatings that consist essentially of manganese and/or iron phosphate, and have a weight not less than 7.5 g/ sq meter of treated surface. This class is normally used where maximum protection is desired particularly under oil, or grease, or where resistance to wear is required.
IS: 6005:1970 is "CODE OF PRACTICE FOR PHOSPHATING OF IRON AND STEEL.
IS: 4777: 1968 reg. PERFORMANCE TESTS FOR PROTECTIVE SCHEMES USED IN PROTECTION OF LIGHT gauge STEEL AGAINST CORROSION.
REGARDS,
S. M. SubramaniamChennai, Tamil NADU, India
A. It is tricky to answer the question based on ANY paint. In my experience the type of paint makes a good deal of difference. That being said I have found that a Zinc Phosphate coating of 8-12 g/square meter is very versatile.
David J Wolf- Painesville, Ohio
A. As my old friend Joe Menke at the US Army's Rock Island Arsenal taught me, SEM photo graphs of 2 zinc phosphate coatings of equal coating weight can give dramatically different results. If a coarse, sporadic phosphate due to low temperature and calcium modifier, for instance, you get reasonable coating weight values but the paint adhesion or corrosion results will be terrible. For a phosphate coating weight to be good, you have to look at the surface morphology as well.
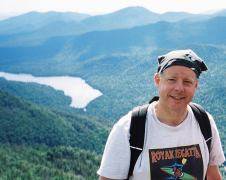
Milt Stevenson, Jr.
Syracuse, New York
Two coats/layers of phosphate?
Q. Hi all,
We have a new customer who is asking for two coats of zinc phosphate on his carbon steel parts, followed by an organic paint coating. He is telling us that additional coats of phosphate will increase salt spray resistance. I don't see how repeating the phosphating process twice will achieve additional protection. Has anyone else heard of this?
Thank you in advance for any information you can give me,
fabricated metal manufacturer - Muskegon, Michigan
2007
![]() |
A. Gut feeling is that you will end up with a worse coating since it takes iron to kick off the phosphate process and going back into the tank will probably soften the existing phosphate before it can kick off. For better corrosion resistance, go to a finer crystal phosphate such as a calcium modified one. - Navarre, Florida A. Hi Kim, - Naperville, Illinois |
A. If your customer was aware of how a phosphate coating forms there would be no need to ask this question.
Zinc phosphating is a precipitation process. Zinc phosphate has very low solubility in higher pH solutions. When the phosphoric acid that the zinc phosphate is dissolved in attacks the substrate the pH at the substrate liquid interface goes up and the zinc phosphate precipitates out to form crystals at the substate surface. This is a self limiting reaction, if you want a heavier coat you just raise the temperature of the bath a few degrees. A second trip in the bath would just result in stripping some of the first coat and re-depositing it in any areas where the substrate may have been exposed. Higher coating weights don't necessarily give better salt spray resistance. Automotive and appliance lines like 250mg/ft^2 and coil lines like 180mg/ft^2. The fineness of the crystals is the most important attribute, much more than the coating weight.
Coil coating - Brampton, On., Canada
Thank you for your responses and for confirming my limited understanding of the phosphating process.
fabricated metal manufacturer - Muskegon, Michigan
A. Dear Kim,
phosphate coating is a conversion coating reaction from chemical and steel, if the steel surface is fully covered by the phosphate coating, no more reaction. you have to find out how to uniform the phosphate coating on the steel part. Coating weight is not important in corrosion protection, fine crystal coating is a point in corrosion protection.
- Malaysia
How to increase zinc phosphate coating weight
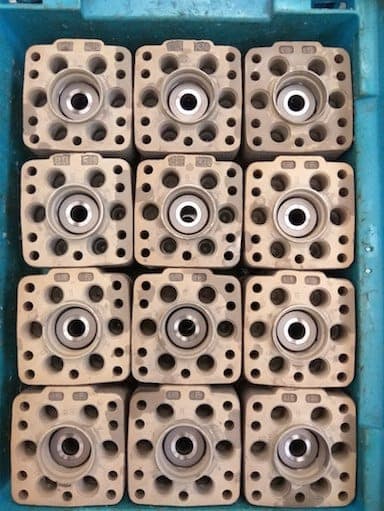
Q. I m having issue with the coating weight. Spec is 2-5 gm/mm^2. Bt every time I m getting it on lower side. I m maintain ing TA at 55-60 ml and FA at 3-4 ml. Using a activation bath at 3-4 ml. Please suggest me possible ways to increase coating weight. At first we are doing degreasing process at 2 bath having a time of 8 min each. Followed by three rinse. Then pickling bath having time of 9 min. Followed by three rinse bath. Then activation of 1 min. And then phosphating for 8 min. Followed by 3 rinse bath.
I am getting these type of rusty part if my coating weight is at lower side.
Rahul JangidSenior engineer at zinc phosphate shop - Jaipur, India
February 27, 2017
A. Hello Rahul!
If you did not solve your issue, give us some more information about the parts, type of steel, and accelerator concentration in the bath.
Regards,
TEL - N FERRARIS - Cañuelas, Buenos Aires, Argentina
Q. Dear sir,
Material is medium carbon steel.
And accelerator conc. is 8-9 % per litres.
Activation conc. is 3-4 ml per litres.
Senior engineer at zinc phosphate shop - Jaipur, India
A. Hello Rahul,
I think this: if you are getting rusty parts when you have low coating weight, you must do things to maintain the coating weight between 4 and 5 g/m2, and not so near to 3 g/m2.
I don't know what is the product you call "activation", but I'm going to assume it's a grain refiner.
For this:
-Maintain TA/FA ratio between 10 and 15.
-Accelerator in nominal to lower concentration spec from your vendor (the more accelerator, the less coating weight).
-Maintain activation in nominal concentration. I don't know how the process will respond to a change in this, so I would ask your vendor in order to maintain coating weight near to 5 g/m2.
-Always check degreaser and pickling for concentration and saturation. You must clean your parts thoroughly if you don't want any rust on your final part.
So, I would try that, and ask your vendor to help you to maintain your coating weight high!
I hope you can solve your issue!
Best regards,
- Cañuelas, Buenos Aires, Argentina
by Samuel Spring
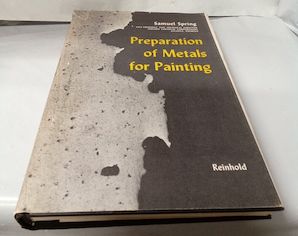
on eBay
(currently)
or AbeBooks
(rarely)
or Amazon
(rarely)
(affil links)
A. Hi Rahul,
I have some thoughts for you regarding the flash rusting and low coating weight phenomena and they center on the preparation of the parts prior to entering the Zinc Phosphate.
Looking at the way those parts are rusting would cause me to question a couple of things, one; whether they are clean going into the pickling process and two; could they be partially flash rusting coming out of the pickle before reaching your Zinc tank.
How long does it take to get thru the three rinses after the Pickle and is the first rinse after the Pickle a dead rinse or flowing in a cascade with the first two? My reasoning here is that a dead rinse or concentrated rinse could initiate almost instantaneous rusting of your parts. The problem with any rusting even if you can't see it is that it inactivates your parts somewhat and the initial Phosphating reactions then have to compete with the removal by the solution of the rust layer so you get an uneven and slow start off in the Zinc.
Oil carryover from your degreaser steps could do exactly the same thing in terms of deactivation prior to the Pickling step.
Also go easy on the Accelerator as that is actually a grain refiner which would lower your final coating weight.
Keeping your temperature up as one of the other responders mentioned along with a slightly lower total acid to free acid ratio will aid in keeping the reaction going longer before shutdown in the Zinc which in turn will raise your coating weight. Just don't push it too far and make the changes with the ratio (Free Acid) slowly to see the effect.
process solutions - Westhampton, Massachusetts, USA
Q. We are doing wire phosphate and our problem is adherence in coating for multiple extrusion products. Can anyone help in how to improve ?
Nagasubramanian Srinivasan- CHENNAI, TamilNadu, India
September 6, 2017
A. Hi Nagasubramanian. You are using this zinc phosphate coating as a lubrication soap for drawing of steel wire? I would not have expected a phosphate coating to not be abraded off by the dies. But please give us details like wire size, reduction ratio, phosphate formulation, etc., so we can discuss the actual case. Thanks.
Regards,
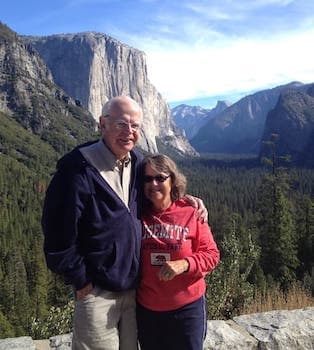
Ted Mooney, P.E. RET
Striving to live Aloha
finishing.com - Pine Beach, New Jersey
Phosphating coating weight too high or too low
Q. IF ZINC PHOSPHATING COATING IS HIGH THEN WHAT PROBLEMS WILL COME? AND IF COATING IS LOW THEN WHAT PROBLEMS WILL COME?
P MANSUR- Bangalore, INDIA
September 23, 2019
A. Hi Mansur. Too much coating weight can mean the coating will come off when the painted part is bent or adhesion is otherwise called into play, too little can mean rust, porosity, lack of corrosion protection. But as other responders have implied, these problems aren't just issues in their own right, they can be symptoms of other things seriously wrong in the process -- the consequences of which can vary depending on the situation. A full discussion needs multiple chapters in a phosphatizing textbook.
But if you'd please describe your actual situation -- painted, powder coated, or bare metal parts? type of paint which will be applied? parts formed after painting? exposure situation? -- and why this question comes up, I think our readers will be happy to try to help you like they helped the previous posters on this page. My experience from posting readers questions here for 25+ years is that if your question is highly detailed and longer than the answer you want, and you'll almost always get quick help; but if the opposite, requiring the reader to long-windedly qualify their answer with numerous ifs-ands-&-buts, that's usually a non-starter :-)
Good luck!
Regards,
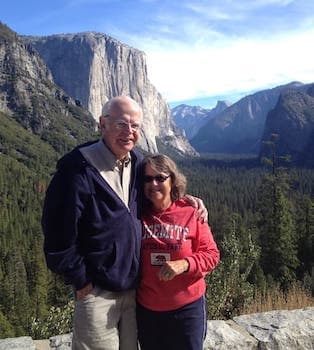
Ted Mooney, P.E. RET
Striving to live Aloha
finishing.com - Pine Beach, New Jersey
Q, A, or Comment on THIS thread -or- Start a NEW Thread