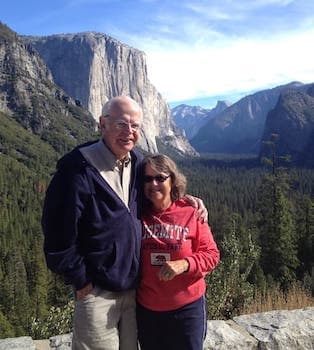
Curated with aloha by
Ted Mooney, P.E. RET
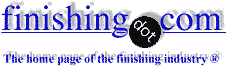
The authoritative public forum
for Metal Finishing 1989-2025
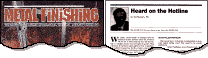
-----
PVC Dipping to form thin transparent product
2002
I am looking for a source of detailed information on dipping of pvc to form transparent products with a thickness equivalent to that of packaging film.
Most appreciated would be information on:
Simplified explanation of the dip process
Suitable Resins and primers
Temperature of dip tank
Temperature of former
Any post dipping processing required e.g. chilling.
I am a degree qualified mechanical engineer but have little knowledge of the dip molding process.
Many thanks,
Joe Gibson- Nottingham, Notts, UK
2004
What kind of piece do you want to make ? You can make dipping with PVC. So you need :
1. to produce a plastisol (Paste-PVC + DINP + stabilizer + pigment)
2. the piece is dipped in the plastisol bath
3. Cured in an oven 180 °C
That the basic idea. The difficult point is to get the right rheology and viscosity level in order to get the proper layer thickness.
Steve VINCENT- Strasbourg, France
Q, A, or Comment on THIS thread -or- Start a NEW Thread