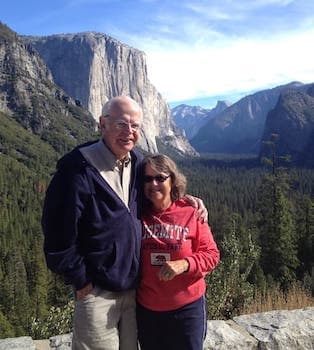
Curated with aloha by
Ted Mooney, P.E. RET
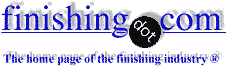
The authoritative public forum
for Metal Finishing 1989-2025
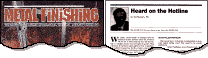
-----
White Spots on Cadmium Plating?

Q. We are currently seeing the same white powdery residue that you noted may occur on cadmium coated surfaces for products packed in wooden crates. Looking for any published work that supports the mechanism for this condition and recommended changes to packaging.
Ed CounsellQA representative - Pittsfield, Massachusetts
February 10, 2022
⇩ Related postings, oldest first ⇩
Q. I am having problems with corrosion on the threaded portion of a safety critical item. After being subjected to 48 hours of humidity at 40 degrees and 90% R.H., I have noticed the formation of what seems like white pustules/spots on the steel component (S96) which is Cadmium plated to a thickness of 15 microns and subsequently coated with molybdenum disulfide. Does anybody know what species these white spots could be?
David Moore- Stevenage, Hertfordshire, England
2002
A. I would expect that the white spots are cadmium corrosion products. I would expect cadmium to start corroding to white rust within 48 hours unless the post treatment was protecting it. It sounds like the molybdenum disulfide is not providing 48 hours of protection. Is there a chromate conversion coating between the cadmium and the molybdenum disulfide?
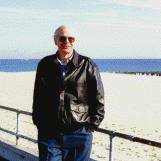
Ted Mooney, P.E.
Striving to live Aloha
finishing.com - Pine Beach, New Jersey
2002
A. Hi Dave,
I agree the white spots are the cadmium corroding. What are your expectations of the coating? One of the main engineering characteristic of cadmium is its corrosion. The fastener industry is flooded with cad plated threads specifically because of the lubricity of the corrosion. This coupled with eliminating corrosion of your base material are the main reasons for cadmium plate. In testing, don't confuse cadmium corrosion as a failure. Typically testing criteria is base corrosion. I also agree that increased corrosion resistance of the cadmium can be attained through secondary chromate treatments. Take a look a what your requirements are, and good luck.
Tim Martinplating shop - Springfield, Massachusetts
2002
Multiple threads merged: please forgive chronology errors and repetition 🙂
Q. I have cadmium corrosion on equipment tie-down shackles, what do you recommend as the safest way of removing this corrosion and preventing its return.
Thanks,
Mark Hoods- North Yorkshire, UK
2004
A. Cadmium is a chronic, cumulative poison like lead and mercury. It isn't safe to try to deal with these corrosion products except at a plating shop which recognizes the hazards and has the necessary protective gear and medical monitoring programs. Take the items to a plating shop for stripping and replating.
There was a time when zinc and cadmium plating were used interchangeably. Today, cadmium is applied to parts only when its unique combination of properties is important. It is quite possible that these shackles can simply be zinc plated this time.
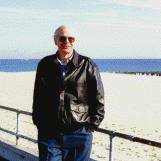
Ted Mooney, P.E.
Striving to live Aloha
finishing.com - Pine Beach, New Jersey
Q. I have a problem of widespread white blooming on aerospace components, some after a very short lifespan (nearly new); is this due to porosity of the original plating, or some kind of other chemical component in the process. Disposal issues aside, how long can this equipment be expected to last before base metal corrosion is a problem, and is there any alternative to complete re-plating or replacement.
John Eaton- Sleaford, Lincolnshire
February 15, 2009
Cause of white powder on cadmium or zinc plated components?
Q. We have a plating facility doing cadmium and zinc cobalt. After plating we are inspecting components 100 % but some of the components at customer end are rejected due to a white powdery deposit. We are carrying out cad/zinc cobalt plating over aluminium and aluminium die cast parts.
Our cleaning is as follows:
Degreasing, soak clean,rinse,desmutting HNO3 50 + H2SO4 25 + 100 gm/lts ammonium bifluoride.
rinse , albond zincating ,rinse,HNO3 50 % strip, rinse, albond zincating, rinse, electroless nickel undercoat, rinse (2), cadmium plating / zinc co plating, Olive green passivation, rinse(2), dry. Oven test 1 hr. 150 °C.
PLATING MANAGER - PUNE, MAHARASTRA, INDIA
November 4, 2009
A. You are turning the chromate to a powder. Above 140 °F it basically becomes worthless. Notice that it is F and not C.
James Watts- Navarre, Florida
November 4, 2009
Q. Regarding the white spots on the cadmium plating. Can we use an 'over the counter' cleaner, or use a Dremel ⇦ this on eBay or Amazon [affil links] and polishing pad, or is this best left to replacement?
Jeff Willis- San Diego, California
November 30, 2009
A. Hi, Jeff. As mentioned above, cadmium is a bio-accumulating poison. For that reason I would not use a Dremel or polishing pad or other method that might spread cadmium dust around. I would strip and replate.
This is the fourth mention on this thread of cadmium corroding, but no one has discussed their chromate conversion coating which is what keeps the cadmium from corroding. After replating, I would include a proper chromate conversion coating. Good luck.
Regards,
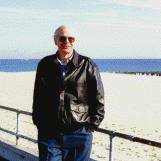
Ted Mooney, P.E.
Striving to live Aloha
finishing.com - Pine Beach, New Jersey
November 30, 2009
Watermarks on Cadmium Olive Drab Finish
Q. I would appreciate any advice on how to minimise or eliminate water marks and staining to our cadmium olive drab finish. We operate within the defence/aerospace industry and as such the visual acceptance criteria for both our iridescent & olive drab finishes are extremely high. 90% of our work is the plating of aluminium components with cadmium over electroless nickel. We operate two manual cadmium lines with one line dedicated to yellow iridescent finish and the other olive drab. All parts are plated manually and are blown dry with compressed air guns before drying in an oven at about 70° C. If however a small bead of water remains on the part the potential exists for an unsightly brown stain to appear.
This problem use to affect our iridescent finish but after introducing a small ion resin system on the final rinse tank this problem was eliminated. Even if a part isn't fully dry, the ultra clean water dries clear and is essentially invisible on the iridescent finish. We attempted the same process of ultra clean rinses on the drab rinse but this resulted in an awful white marking and pale finish as the ultra clean water seemed to affect the drab coating. A technical sales rep suggested dirtying up the rinses which eliminated the problem (I am still somewhat confused by this, but it worked?) Due to work throughput it is seemingly impossible for the plater to air dry every jig of work so thoroughly to eliminate all trace of water on every occasion. The result of watermarking means that the parts have to be re-worked, such is the visual acceptance criteria.
I apologise for the lengthy query but just wanted to be as detailed as possible. Would anyone be able to offer any advice as to a method or combination of techniques to eliminate this problem. I have read some articles that suggest adding wetting agents to rinse waters though I am unsure what wetting agents are suitable. Any advice will be gratefully received.
Works Chemist - Ashford, Kent, UK
April 14, 2012
A. Rather than reworking parts with the water stains, have you tried cleaning them with pure ethanol? It may be cheaper and faster than reworking them.
- Brisbane, Queensland, Australia
April 23, 2012
A. Hi Lewis,
We introduced a quick rinse with iso-propyl alcohol (IPA) after the final rinse as a water displacement and drying accelerant. Since it was introduced we haven't seen any watermarks.
Aerospace - Yeovil, Somerset, UK
First of three simultaneous responses -- April 25, 2012
A. Why don't you try a "very" hot water final rinse prior to drying!!
Best of luck.
Regards
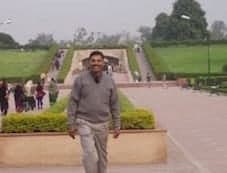
T.K. Mohan
plating process supplier - Mumbai, India
Second of three simultaneous responses -- April 25, 2012
A. You may try drying the components using hot air blower in a closed conveyor chamber system to avoid manual drying. It involves capital investment, but it's worth considering your cost of rework.
Kishore Phadnis- Mumbai, Maha. India
Third of three simultaneous responses -- April 25, 2012
! Many thanks for all your good advice. As of last week I introduced a wetting agent to the rinse tanks with an immediate effect. Over the last 10 days we have not recorded a single reject for watermarking.
I will closely monitor the situation to determine how effective this method is in the long term. As regards to Mr. Phadnis suggestion of using a conveyor oven, this is something we have been considering for a long time and have subsequently approached a manufacturer with the view to designing an oven suitable for our application.
Regards
- Ashford, Kent, UK
April 30, 2012
White film on Cadmium Plated connectors with Olive Drab finish
Q. My name is Nick and I am an Engineer with a cable manufacturing company. I have a problem with cadmium plated connectors. I make a junction box assembly that has a lot of Olive Drab Cadmium plated military circular connectors on it. I recently received about 10 of these unused boxes back from my customer's stock because all of the olive drab connectors have a white film on them. The film has a slightly acidic smell to it. The connectors are from a variety of different manufacturers, but all have the same finish.
Any ideas what could be causing this?
Thanks.
Engineer - Saint Petersburg, Florida
April 30, 2012
A. Hi Nick,
This sounds like you have a storage issue, especially as the fault occurs across a number of manufacturers.
Cadmium is susceptible to corrosion (that is what you are seeing, cadmium corrosion products) when stored in certain conditions such as in wooden containers or in corrosive atmospheres. I think your first step is to check out the storage conditions.
Aerospace - Yeovil, Somerset, UK
May 2, 2012
Q. Brian,
Thanks so much for your helpful response. As a matter of fact, these assemblies have been stored in a wooden crate for the last couple of weeks. The crate is made from OSB board (commonly known as chip board). Do you know what it is about the wood that may cause corrosion of the cad plate?
I am running a test in another crate now to see if I can duplicate it. It's only been one day, but no sign of corrosion yet.
Nick
Engineer - Saint Petersburg, Florida
May 4, 2012
A. Hi Nick,
Chip boards are bound using a resin. The resin leaches into the box and is corrosive to several metals, but is most noticeable on zinc, zinc alloys and cadmium, all of which seem to be particularly susceptible to this particular corrosion issue.
Replacing with solid wood boxes won't help either, especially pine as the sap is is corrosive to the cadmium.
The best bet is to have them packaged in plastic containers if you can. If it has to be wood then I would suggest the parts need to be individually wrapped in polythene bags or similar, the boxes need to be vented and some form of corrosion inhibitor could be added. Saying that do not use VPI/VCI type papers as these can also corrode cadmium. You may want to look at VpCI type corrosion inhibitors.
Aerospace - Yeovil, Somerset, UK
May 8, 2012
Thanks Brian. The wood box did in fact cause the corrosion. After 5 days we saw the white film all over the connectors. The odd thing is that these connectors have a chromate conversion coating on them that is supposed to prevent the corrosion of the underlying cadmium, at least until it gets into service. It doesn't seem to work very well. In any case we are going with the plastic bag and some desiccant material. That should take care of it.
Thanks very much for your responses. They have been extremely helpful.
Engineer - Saint Petersburg, Florida
May 14, 2012
A. Hi Nick,
The passivation is unfortunately not very good at stopping corrosive vapours, that's why the cadmium was able to be attacked. The mechanism for corrosion is a little different from that of a moisture laden environment, where the hexavalent chromium is mobile and able to protect the cadmium. Good to see that you got to the bottom of the problem.
Aerospace - Yeovil, Somerset, UK
May 15, 2012
Cad plating turns white during storage
Q. We store a lot of CAD plated items. We have trouble with stored items turning white. The parts are stored in wooden boxes in an un-climate controlled warehouse. Is there anything we can do to stop the CAD plating from turning white? Items left out in the weather do not seem to have this issue.
John EberlingPlant Engineer - Monroe North Carolina USA
June 3, 2015
![]() |
A. Hi John, Aerospace - Yeovil, Somerset, UK June 4, 2015 June 4, 2015 A. Good day John. Lab Tech.- Whitby, On. Can. A. I suspect your plater is not neutralizing off the cyanide film before applying the chromate, then with temp/humidity cycling the cadmium corrodes. Or that it is one of those lately tri-valent chromates that is failing. ![]() Robert H Probert Robert H Probert Technical Services ![]() Garner, North Carolina ![]() June 4, 2015 |
Gentlemen,
I thank you all for the quick responses. We will not be able to abandon the wooden boxes but we will explore some dry film lubricants to coat the CAD plated parts before assembly. Thanks again for all the help.
- Monroe North Carolina USA
June 8, 2015
A. Bonjour,
It is not recommended to store or to transport the olive green passivated cadmium plated parts in wooden boxes. The vapors from adhesives based on formaldehyde or formic aldehyde are harmful and likely to produce this phenomenon. We see in the photo that the box is made of chipboard and heavily impregnated with glue.
- Mieussy,Haute-Savoie, France
August 5, 2015
Cadmium plating corrosion
Q. We store a lot of CAD plated(type II) items. We have trouble with stored items turning white, which I understand is cad plate corrosion. The parts come from multiple plating houses, and every part that has cad plating exhibits this corrosion. I do not believe this is a problem with the plating process, most likely a problem with our storage conditions. The parts are oil dipped and wrapped in paper(not VPI/VCI type paper) or stored in plastic bags. These parts are not cad plated all over, so we need to be able to protect the surfaces that are not plated from corrosion also (hence the reason for the oil). Is there anything we can do to stop the CAD plating from turning white?
Katey GrubisaPlating shop employee - Park City, Utah
November 12, 2015
Q. I have seen the white corrosion products on Cadmium plated connectors in the manufacturing process. EDS indicated strong Cadmium and Oxygen signatures. This is not from long term storage. This is from normal manufacturing that utilizes a saponified wash followed by de-ionized water rinse and heat/blow drying. The appearance is the same as in the images. Since the connectors came from two different manufacturers, I'm looking more at the process. Any ideas?
Sanmina-SCI - Huntsville, Alabama, USA
April 30, 2020
? What is in the "sponified wash"? pH. Read the MSDS to us.
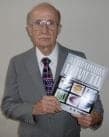
Robert H Probert
Robert H Probert Technical Services

Garner, North Carolina
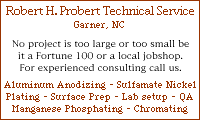
May 1, 2020
A. Hey Curtis,
It looks like you have cadmium corrosion. The protection of cadmium on steel or if it is plated on electroless nickel over aluminum/plastic is a sacrificial coating. This would mean it would corrode preferentially over the base materials. If you google cadmium bloom some of the images are similar to what you are seeing. Cadmium usually gets chromated which gives much more corrosion protection from seeing white corrosion products, it also gives it the Olive drab color you have (although other colors exist).
The chromate is most likely a hexavalent chromate which has an effective temperature limit. Cr6 chromate layers have a temperature limit, typically they excessively dehydrate at prolonged times exposed to temperatures above 150 °F, although I actually have not done any studies on bake times/ bake temps/ vs salt fog results.
It is also possible that, whatever this saponified wash is, could just be attacking the chromate, exposing the cadmium with no chromate layer. The "self-healing" of Cr6 chromates is meant for minor handling damages; it won't re-chromate the whole part! You could test this by just adding some concentrate of the wash on area unaffected and see if the area turns a metallic dull grey.
Amphenol Aerospace - sidney, New York, USA
May 2, 2020
Gentlemen. Thank you for your assistance and comprehensive response.
A. The Saponified wash consists of an additive amine ethoxylate. The MSDS reports a ph of 11 (10g/l).
B. I plan to work with the QE to get the process changed. It sounds like a combination of factors which include the aggressive wash and heat afterwards. I recognized the corrosion aspect and had read about high heat affecting the plating. I did not know about Chromate or consider the combination of factors.
Sanmina-SCI - Huntsville, Alabama, USA
May 6, 2020
A. The saponified wash is the corroder.
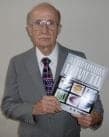
Robert H Probert
Robert H Probert Technical Services

Garner, North Carolina
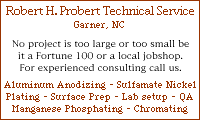
May 7, 2020
Q, A, or Comment on THIS thread -or- Start a NEW Thread