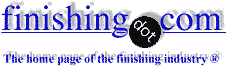
-----
Re-use of DI water from solder plating process to electrolytic deflashing process
Dear Sir/Madam,
I would like to propose a project for a cost reduction program of our company and I badly need the help of some experts. Can I safely re-use the deionize water which is used as a final rinse in solder dipping process as a final rinse in electrolytic deflashing process? And what method is the most reliable and effective in terms of initial installation cost and operation cost?
Presently, the company is using demineralized water as a final rinse in one machine (out of 4 machines)which process nickel frames requiring solder dip process since yellowish contamination is observed with the use of tap water or city water. The 3 other machines are using tap water only since most of the packages processed in these machines require matte solder plating.
I have come to this thought to re-use the DI water and save money for using tap/city water instead of throwing it out directly to the wastewater system. Please help me.
Thank you so much! God bless you.
- Metro Manila, Philippines
2002
It is unusual to use tap water for the final rinse before or after solder dipping or plating lead frames, especially the hard, high silica water in the Philippines! Most companies use DI water for both.
The rinse after deflashing is not a critical one as long as there is an acid descaling step and a rinse with good quality water before solder dipping or plating. Many companies recycle a significant percentage of deflash rinsewater with just a filtration system. The only problem that I can think of would be any flux residues that may be present in the rinses after dipping, so you may want to filter the water through activated carbon and also a particle filter before reusing it in the rinse after deflash.
It may also interest you to know that there are may companies that recycle the DI water from Solder Dipping and Plating rinses back to the same rinse after with activated carbon and deionization. This includes many companies in the Philippines. This is a more expensive approach, but could also result in significantly higher savings. You can find more information about this on my company's web site.
consultant - Cleveland Heights, Ohio
2002
2002
Sir,
I'm sorry if I didn't make my letter clear enough for you to get me. We are actually using DI water in solder dip and solder plating processes. The electrolytic deflashing machines that we have, uses the tap/city water which we are encountering yellowish contamination on heatsink area especially to frames requiring solder dip. Presently, the containment action that we are doing to somehow eliminate the problem (yellowish contamination on heatsink after electrolytic deflash) is the installation of demineralize water on one machine exclusively running nickel frames (since other machines process frames/packages requiring solder plating)which is too costly. And so I've thought of using the DI final rinse after solder dip, to be used as a final rinse in electrolytic deflash.And I'm asking for your help. I'm interested to know more about the DI water recycling method you have suggested. And I'm looking forward about it by visiting your company website. I wish to hear more from you, sir to clear things up with me regarding this matter. I'm very much interested and I'm proud to have this project in our company with you as my adviser. Please help me more.
Thank you so much. God bless you!
- Philippines
Q, A, or Comment on THIS thread -or- Start a NEW Thread