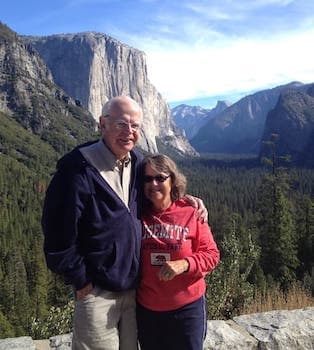
Curated with aloha by
Ted Mooney, P.E. RET
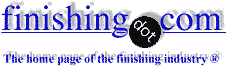
The authoritative public forum
for Metal Finishing 1989-2025
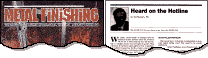
-----
Hard anodize thickness
Q. We have a product call for hard anodize thickness 0.002"" to 0.003". Is this an industry norm that refer to the total thickness including imbedded and build up thickness? I understand that for hard anodize half of the coating is imbedded and the other half is built up. Correct me if I'm wrong.
William Wong- Singapore
2002
A. Its common practice to account for both the "on top" growth, and the penetration, when referring to a anodizing thickness specification. So you are correct.
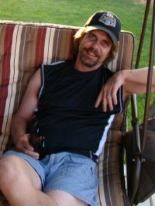
Marc Green
anodizer - Boise, Idaho
2002
A. Hi William. The thickness spec sounds okay; probably .002" minimum would be fine. This would be the TOTAL thickness of the anodized coating.
It may be true that part of the coating is 'imbedded' and part is external, but there is no real difference in them and that's not the way most people view the situation.
An easier and more useful to look at it like this: the coating is essentially Al2O3, .002" thick. But where did the Al2O3 come from? Well the aluminum that was on the surface of the part reacted with oxygen from the solution. To build .002" of Al2O3 consumed about .001" of aluminum off of the surface. Good luck.
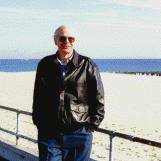
Ted Mooney, P.E.
Striving to live Aloha
finishing.com - Pine Beach, New Jersey
2002
Q. Hi Everyone,
Thank you for your time. I am a sales rep at a machining shop in Taiwan. We received a print that calls for hard anodizing per MIL A-8625C, Type III class one with thickness of 0.0003/0.0005" (0.008/0.013 mm) on AL6061-T6. Several anodizers all advised that at such thickness, it would be normal anodizing instead of hard anodizing. Never did they hear of hard anodizing that's so thin and thought that the client must be confused because the minimum thickness for hard anodizing is 0.02 mm. But the manufacturing engineer of our client replied that hard anodizing is needed at the stated thickness. It is a thinner callout than typical hardcoat callouts but they have had success doing it for over 10 years.
Who is right? If the manufacturing engineer of client was correct, could there be a technology that can achieve the hard anodizing at such thickness that's already out there for over 10 years which the Taiwanese anodizers not only did not mastered but also never heard of? What is the "callout?" With my very limited knowledge in this area I also did not find this information when searching online.
Or could there be a disagreement in each side's definition of anodizing and hard anodizing? If the thickness and the required hardness of the part was achieved, could it be said that "normal anodizing" is doing the job?
Thank you.
- Taiwan
May 1, 2014
A. Hi Arthur. Hardcoat anodizing is done at a lower temperature (approximately freezing) compared to conventional anodizing (approximately ambient), and there may be some other small variations. I see no particular reason the parts could not be immersed in a low temperature hardcoat anodizing bath for sufficient time to generate a coating of 0.0003 to 0.0005". This may meet your customer's needs.
MIL-A-8625 does say that the thickness must be 0.002^ 0.0002" unless otherwise specified; since it's otherwise specified, that part is okay. As a matter of good practice, though, you and your customer should probably not call it MIL-A-8625C Type III unless you know it will comply with all requirements of that specification, such as abrasion resistance -- and if it doesn't because it's too thin, where would that leave you except in the middle of a contract dispute?
Regards,
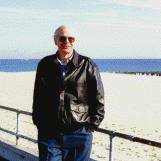
Ted Mooney, P.E.
Striving to live Aloha
finishing.com - Pine Beach, New Jersey
May 2014
May 3, 2014
A. Who is right? Why, the customer... of course! So basically I'm saying,in my opinion, it's not the anodizer's place to tell the customer to question or change what has been working for 10 years.
First things first, the print call out should at least be updated to the current mil spec, which is 8625F. The mil spec states that the minimum thickness for a type 3 coating shall be .0005" (I think Ted meant to type .002" which is the typical coating thickness call out for type 3).
There are several differences in processing parameters between type 2, and type 3. So I believe your Taiwan anodizers are wrong when they say it's the same.
1. Type 3 is generally done at a low temperature, as Ted stated, although some anodizers employ an additive that allow them to "hard coat" at higher temps.
2. Type 3 is also ran at a higher current density than type 2.
Those two parameters alone alter the pore structure of the coating, and the density of the coating, which results in different coating properties (some of which, may be important to the end user)
And finally, type 3 coatings are not sealed, unless specified per print. Sealing reduces the hardness properties of the coating. Type 2 coatings are sealed.
If I received a print like this in my shop, calling for hardcoat at that thickness, the only thing I would do, would be to insure that the customer didn't mean to call out .003"-.005" and verify that someone didn't accidentally insert an extra 0 (as Ted just did :) ). Once that's verified, and if the thinner thickness is indeed what the customer wants, I'd shut up, and give it to them. Like I said, the end result comparison of the type 2 and type 3 coatings, at the same thickness, would show that the coating properties are indeed, not the same.
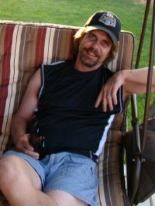
Marc Green
anodizer - Boise, Idaho
A. The process parameters for Type III hardcoat are different than Type II commercial anodize. Typical variables include electrolyte chemistry and lower temperatures as well as electrical waveform and higher current density. It is not usual for a callout for a thin or flash hardcoat. It is processed using hardcoating parameters for a reduced cycle time. The hardcoat process per MIL-A-8625 is proofed once a month using a Taber abrasion test on a panel with a 0.002" thick coating.
Chris Jurey, Past-President IHAALuke Engineering & Mfg. Co. Inc.

Wadsworth, Ohio
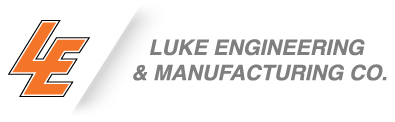
May 3, 2014
Thank you everyone for your input. Contract dispute is definitely something we actively avoid. Your knowledge and the willingness to share is much appreciated!
- Taiwan
May 5, 2014
Q, A, or Comment on THIS thread -or- Start a NEW Thread