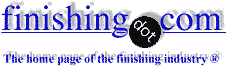
-----
Corrosion of 304 stainless burner in phosphoric acid tank
Have a pickling tank with approx. 10% phosphoric acid at 130 degrees F with a serpentine gas-fired side-mounted burner tube in the bottom. Tank construction is entirely 304 stainless. Having a problem with burner tube leaking, always at a welded location. Have re-welded or cut out and replaced sections three times in the past. Repairs last about 6 months. Leaks typically occur closest to the burner entrance. Weld repairs are high-quality work using 308L filler rod. There are no other tank leaks at any of the welds. There is a lot of sludge buildup everywhere in the tank, including on the burner tube. There was no subsequent treatment or cleaning of the welds after the various burner tube repairs. What is the best possible alternative to extend the life of the burner tube? Thank you.
Paul Dubenko- portland oregon usa
2002
First of two simultaneous responses --
Paul,
I have two suggestions to improve the life to the welds in your pickling tank. The first is to passivate the weld and surrounding surfaces with either nitric acid or another passivating solution. The second is to monitor the amount of chloride in the pickling solution. Chlorides may be present the city make up water and the evaporation of the water from the heated pickling solution increases their concentration in the pickling solution over time. Chloride in the presence of phosphoric acid will corrode the stainless steel.
Roy NussTrevose, Pennsylvania, USA
2002
Second of two simultaneous responses --
I hate the darn things. Your problem is your pipe is getting too hot where the flame enters the tube. SS was not intended to withstand high heat in an acid solution. Since money is a problem in most institutions, I would look a putting a sleeve with spacers for the first couple of feet at the inlet.I would also put less heat in. This will frequently give you a lower tube temp as it can dissipate the heat enough to keep the temp down. This can normally be done very inexpensively by the changeout of the burner tip. Combustion temp will stay the same for a properly adjusted system, but there will be less heat. Drawback is that it will take longer for the tank to heat up. A plus is that you will have a better heat transfer efficiency because less heat will go up the stack.
James Watts- Navarre, Florida
2002
2002
Thank you for your responses. I should mention that the tank is 14ga 304 stainless, and none of the welds on the tank walls or anywhere else are failing. The only problem is with the welds nearest the burner tube entrance. We will reweld, citric-acid passivate, install a ceramic sleeve inside the first two feet of burner, refill with Reverse Osmosis water, reduce the heat input to the burner tube (it's a fairly new [1997] modulating MAXON burner, does changing the max fire % do the same thing as replacing the burner tip?), and see what happens. Is an external coating on the burner tube for the first inch or so to prevent/delay burner tube corrosion at the troublesome weld area feasible? If so, any recommendations for an appropriate coating material? Would cured normal or hi-temp RTV silicone hold up to the temperature/acid or cause any bath problems?
Paul Dubenko- Portland, Oregon, USA
Q, A, or Comment on THIS thread -or- Start a NEW Thread