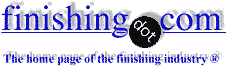
-----
Type III anodize/silver plating combination finishing
I am interested in type III anodizing the interior surface of a hollow aluminum extrusion, leaving the outside uncoated. Then, I would like to slice the long extrusion into smaller pieces. Lastly, I would like to plate all the exposed aluminum (outside and ends)with silver. Can the inside of the extrusion be anodized while leaving the outside surface alone? Is it possible to use the dielectric strength of the oxide formed from the anodizing process as a mask for the electroplating? I need to have very high dielectric and mechanical strength inside the extrusion, but need high electrical conductivity and wear resistance on the outside (there will be sliding electrical contacts here).
Thanks!
Brian Esser- Burlington, Vermont, USA
2002
2002
What is the alloy, diameter and length? For a cathode use any metal largest diameter wire you can snake through the tube while the tube is in a vertical position. This large diameter wire should be insulted to prevent shorting with plastic beads. While pumping the anodizing electrolyte in at the bottom and overflowing at the top,jiggle the insulated wire up and down for the length of time it takes to get the thickness you want, probably 60 to 90 minutes. I'll calculate your current and voltage and time when you furnish the alloy and sizes (length and Inside diameter).
After anodizing and slicing, then plug the inside with rubber stoppers and take through the zincate, alkaline electroless nickel strike, silver strike and silver plate.
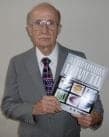
Robert H Probert
Robert H Probert Technical Services

Garner, North Carolina
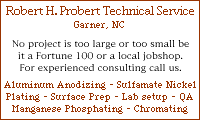
The material will be AA1370. The extrusion will have multiple voids, each very small (1.75 mm x 1.75 mm). Depending on the process, 1- meter lengths would be appropriate. As per the first posting, I would like silver plating on the outside and Type III anodizing inside each channel. Perhaps it would be better to plate the exterior surface, cut the extrusion into shorter (about 2 cm long)lengths, then anodize the ends and interior of the channels. The profile of the extrusion is basically stacked boxes. Would the silver plating act as a mask for the anodize process? Or, would the reverse be better (it is not important at this time whether the ends of the pieces are conductive (plated) or insulating (anodized))?
Thanks.
Brian Esser- Burlington, Vermont, USA
2002
I personally would suggest you pre-cut the parts in question to the sizings/dimensions you want. Then mask the exterior portion of the part, hardcoat anodize, then mask the hardcoat portion and silver plate. Because I am not familiar with silver plating I can't comment on what chemicals are involved in its prep and treatment steps that would/might affect the hardcoat finish. That is the reason for my suggestion on masking the hardcoat. If someone can confirm it would be fine in the process w/o the 2nd masking step, then do as such.
The reason for pre-cutting is because hardcoat thickness and edges do not match up. When you start sawing, or cutting a hardcoat anodized part, you end up with chips and nicks around the cut edges. This is just the nature of the beast.
Matthew Stiltnerplating company - Toledo, Ohio
2002
Q, A, or Comment on THIS thread -or- Start a NEW Thread