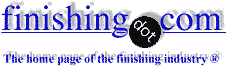
-----
Plating vs. anodizing
I'm working on an high end indoor furniture project using assemblies of wood and metal. For density reason I am likely to use aluminum rather than stainless steel as the frame. Although most of the alloy frame will be covered with wood, some parts of it will be visible to give an inlayed appearance, flush with the wood element. I would like to plate those visible parts in either yellow brass or red copper. I have only read about the zincification process necessary for plating on aluminum so I don't how precisely it can be performed (some parts may be no wider than 4-5mm wide and 20cm long). Can someone clarify this process to me? I'm also aware of copper oxidation and still looking for a way to prevent it, like perhaps dipping the frame in a lacquer solution before the assembly with the wood? Since it will be flush with the wood, it's important that neither affect the other (stain, oxidation, corrosion, etc...) when common household cleaners are applied. Finally, to avoid all of this I've been suggested anodizing instead of plating. My concern is, will anodizing give me the same tints and finishing appearance as copper and yellow brass (I haven't yet decided whether to have a glossy or brushed finished surface)? Thank you in advance for your feedback.
Victor Bee- Hong Kong
2002
2002
Pre-treatment by zincating
To obtain good adhesion when plating on aluminium it is necessary to start with a pre-coat of zinc or tin. This pre-coating is necessary pre-treatment prior to the main metal plating. As mentioned above, most plating on aluminium is currently carried out on top of chemically deposited zinc produced by immersion in modified zincate solutions. The zincate process has been developed into a relatively simple, cheap and reliable technique for plating on aluminium and a wide range of aluminium alloys. It is less sensitive to alloy composition than processes based on anodising pre-treatments, does not need the applied power requirements of anodising and is cheaper than the stannate immersion process owing to the high price of tin.
Theory of the zinc immersion process
The basic reactions in the alkaline zincate solution are the dissolution of aluminium and the deposition of zinc.
The basic reaction may be written as:
Anodic:
Al + 3 OH¯ ¯ => Al(OH)3 + 3e¯
Al(OH)3 ¯ => AlO2¯ + H2O + H+
Cathodic:
H+ + e¯ ¯> H ¯> 1/2H2 (g)
The zincate ion in strong alkaline solution is probably in the form Zn(OH)42¯. The deposition of zinc may therefore be expressed as:
Cathodic:
Zn(OH)42¯ ¯ => Zn2+ + 4 OH¯
Zn2+ + 2e¯ ¯ => Zn (s)
The zincate solution is normally made up from zinc oxide and caustic soda ⇦liquid caustic soda in bulk on Amazon [affil link] and it has been shown that the ratio of these constituents has a profound effect on the adhesion of the subsequent deposit. The physical conditions, time of immersion and temperature, can also affect the degree of adhesion.
Effect of solution composition
A lot of investigation has been done to define the optimum composition of the zincate solution. It has been indicated that the presence of nickel in the zincate solution improves the adhesion of nickel plated directly onto the zinc deposit. Copper also assists adhesion to some alloys, and a substitution of zinc oxide by zinc sulphate was found to give a further improvement.
Best regards,
Hannu Pyöriä- Helsinki, Finland
Q, A, or Comment on THIS thread -or- Start a NEW Thread