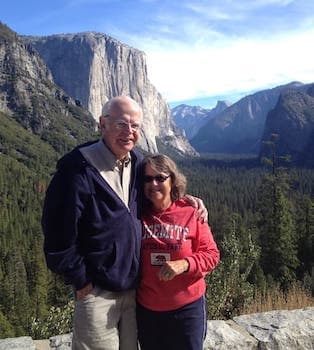
Curated with aloha by
Ted Mooney, P.E. RET
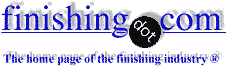
The authoritative public forum
for Metal Finishing 1989-2025
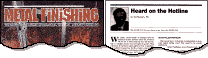
-----
Need ZINC-IRON plating to meet specified salt spray hours
Q. Recently we have seen our customer base move from using ASTM B633 Black Zinc and calling for a Black Zinc Iron Specification ASTM B842. It would appear that it generally increases the salt spray requirement under ASTM B117 but we are unclear as to its other characteristics. Is it RoHS compliant? Will the chemistries used in the B633 process overlap and work with B842? Will our current tank layout need to change or add tanks to complete this B842 process?
Thanks in advance for your response.
Ken
- ROCHESTER, New York
December 16, 2021
A. Hi Kenneth. For the benefit of newbies trying to follow this discussion, zinc plating is not black ... rather "black zinc" means zinc plating followed by black chromate conversion coating.
The zinc alloy platings (zinc-cobalt, zinc-iron, and zinc-nickel) do offer greater corrosion resistance than plain zinc. This may be partially because they are less reactive (closer to steel on the galvanic chart), but probably mostly because their corrosion products are more stable and do a better job of protecting the substrate from the atmosphere.
But another feature of zinc-iron plating is that it may be easier, less expensive, and more stable to perform black chromating on than plain zinc; I believe that this is because the iron content allows a blackening reaction which zinc doesn't offer (many black chromates for zinc were based on silver and therefore exhibited troublesome color changes).
In this case it is the chromate conversion coating rather than the plating which is or isn't RoHS-compliant. I assume there are RoHS-compliant (hexavalent chromate free) black chromates for zinc-iron available, but this is something for the chemical supplier to assure you of.
I was involved in a case where, in the course of a new startup, the silver-based black chromate on zinc was turning green, and a transition to zinc-iron and silver-free black chromate was done overnight and immediately solved the problem ... but that was pre-RoHS, so again, you'd need to check with the supplier of the plating process and chromate process.
Luck & Regards,
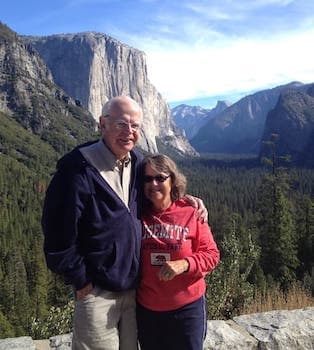
Ted Mooney, P.E. RET
Striving to live Aloha
finishing.com - Pine Beach, New Jersey
December 2021
⇩ Related postings, oldest first ⇩
Q. I work for an industrial supply company, and have a customer that is using Zinc-Iron Black. This spec calls for a minimum of 200 to white rust and 338 to red at a .0005 thickness (12 microns). I am having a little difficulty finding a plater in the US that will certify to these specs. I am being told that they can only certify this 140 to white rust? Are there standards that dictate what a plater can certify to like there are with zinc and zinc dichromate in the ASTM book. I know the ASTM B842 covers Zinc-Iron, but I will be honest with you, I can't understand what it is telling me about actual salt spray hours. It seems that other countries like Japan and India can meet these specs but again in the US I am having difficulty.
Jennifer Sterchi- Lexington, Tennessee, USA
2002
First of two simultaneous responses--
A. Generally, it is not a matter of what a plater can do but of the liability a plater may have. Therefore, they will use the corrosion resistance information from their supplier of the process. Typically, many processes exceed the amount of corrosion resistance in the literature. Since a plater cannot test every part, they will want to have a large margin for error in what they promise.
Gene Packmanprocess supplier - Great Neck, New York
2002
Second of two simultaneous responses--
A. My firm has been supplying black chromated zinc/iron plating to the automotive and other demanding industries for over 3 years now and it is our experience that our black zinc/iron will indeed meet your 200 hours to white / 338 hours to red at 1/2 mil (0.0005 inch) thickness. I checked this out with our chemical supplier and he too sees no problem; use a quality black chromate and a process-control driven plater will achieve this requirement quite consistently.
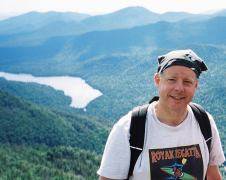
Milt Stevenson, Jr.
Syracuse, New York
2002
A. Being a process control driven plater, I promise 600 hours to white rust and 1000 hours to red rust FOR VAT PLATED PARTS and the same hours as you have specified for barrel plated parts with zinc-iron black.
The issue here is to differentiate between barrel and rack plated specs. Zinc iron baths cannot be handled as easily as other zinc plating baths and your plater has his work cut out if he has to get proper results. Either that or you are getting confused with zinc-black which has very poor SST resistance .
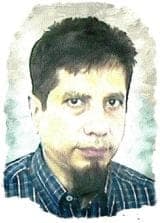
Khozem Vahaanwala
Saify Ind

Bengaluru, Karnataka, India
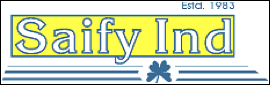
2002
April 15, 2012
Q. What is the procedure to get a good salt spray life of above 200 hrs white rust and 500 hrs of red rust with the a process of Zinc iron with trivalent white passivation + sealant.
Your suggestions are welcome.
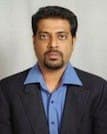
Jayakumar Selvaraj
metal finisher - Chennai, Tamilnadu, India
Hi Jayakumar. As you see, we added your question to the above dialog, which goes a way towards answering it. But please get back to us if you consider your question unanswered. Thanks.
Regards,
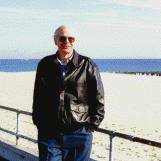
Ted Mooney, P.E.
Striving to live Aloha
finishing.com - Pine Beach, New Jersey
Q, A, or Comment on THIS thread -or- Start a NEW Thread