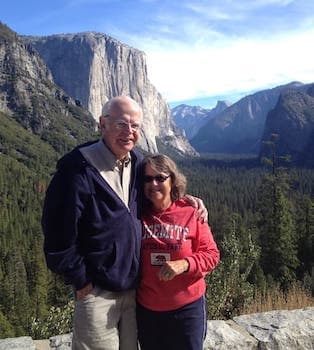
Curated with aloha by
Ted Mooney, P.E. RET
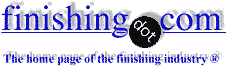
The authoritative public forum
for Metal Finishing 1989-2025
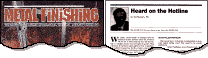
-----
Hot dip tinning vs. tin electroplating

this text gets replaced with bannerText
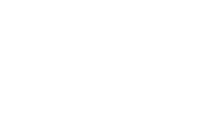
Q. I am about to manufacture tinned copper wires of diameter in the range 0.25 mm to 0.30 mm for low voltage solar energy applications. Shall I prefer hot dipping or electroplating for the same? The wires are flexible cable types.
- Delhi, India
June 30, 2023
A. Hi Anurag. I don't know much about wire drawing, but I think it's conventional to put a heavy deposit on a thicker wire and then draw it down, rather than electroplating directly onto the fully drawn-down wire.
Hot dipping is probably a little simpler and lower in capital costs, but does not offer the precision thickness control that electroplating does, because controlling the amount of electricity directly controls the thickness. Hot dipping will require maintenance and frequent replacement of some sort of 'wipes'.
I am not an expert on this decision and welcome additional comments.
Luck & Regards,
Ted Mooney, P.E. RET
Striving to live Aloha
finishing.com - Pine Beach, New Jersey
⇩ Related postings, oldest first ⇩
Q. I am looking for a home process to tin plate reproduction spurs. Originals were cast malleable iron and tin plated, they date to the early 1800's.
John Vaccaro- Dillon, Montana
1998
A. Hi John. Around here we're not big on doing metal finishing at home.
But please look into some of the books listed at www.finishing.com/books/ for an introduction to the subject. Good luck.
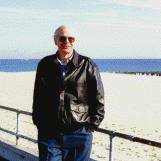
Ted Mooney, P.E.
Striving to live Aloha
finishing.com - Pine Beach, New Jersey
A. Hot dip tin is NOT plating. There is no electrical or chemical activity. Hot dip amounts to having something that can get tin to its melting point, dipping the part in the molten tin and then trying to get the excess off. We used to refer to it as the dip and sling method because if you tossed it into the corner of a cardboard box so that it would caroom off at least two sides, it would not have too much excess tin on it. Allowing the part to stay in the tin longer gave a little higher part temp which gave a little longer "sling" time.
A small amount of lead will lower the melting point a fair amount. I would not take it to the eutectic point of 60/40 tho.
Tin is reflowed in very hot lard. Now that is a stinky mess.
James Watts- Navarre, Florida
Thanks, Jim, I wasn't alert to the fact that we were talking about hot-dipping. Whether hot dipped or electroplated, tin itself is usually not regulated in the effluent. So it's then a matter of whether cleaning and pretreating is a safety or environmental issue, and avoiding post treatments.
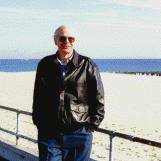
Ted Mooney, P.E.
Striving to live Aloha
finishing.com - Pine Beach, New Jersey
A. Ted, I am going to mention this just for fun. But tin plating on copper and brass utensils at home is still a big "small business" in the third world. Once every couple of years, these proprietors used to come to our door to check if tin plating was needed. If so, he would set up his tiny operation in our yard. A charcoal stove to heat the pot, a white powder to rub the hot pot using cotton glove as the preclean, and a tin wire. Once the surface was cleaned, he would rub a little tin wire on the hot surface and then polish the whole surface with the same cotton glove. I forget the name of the white compound but that compound generated a lot of white vapors which I am sure are toxic. But the guys lived for many years for sure. You would not believe how bright and shiny the pots looked.
Mandar Sunthankar- Fort Collins, Colorado
Thanks, Mandar. An update for the readers: This site now has a couple of threads about the tinning of pots as mentioned by Mandar. Please see topics
25553 and
29192 for starters or search the site for 'tinning copper pot'.
Remember that only lead-free tin, not solder, must be used on a vessel for food or drink.
Regards,
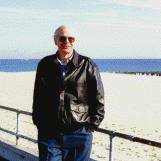
Ted Mooney, P.E.
Striving to live Aloha
finishing.com - Pine Beach, New Jersey
Q. Can you give me some suggestions on hot dip coating tin on Aluminum?
Dingminsjtu - Shanghai, China
2006
A. Hi, Dingmin. The only way that I am personally aware of doing it is to zincate and then copper electroplate the aluminum before the tinning.
Regards,
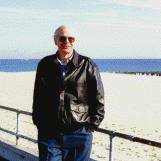
Ted Mooney, P.E.
Striving to live Aloha
finishing.com - Pine Beach, New Jersey
Multiple threads merged: please forgive chronology errors and repetition 🙂
Q. Would like to know: what are the main components in a tin plating line.
Marc P [last name deleted for privacy by Editor]- Houston, Texas, USA
2001
A. A hot dip tinning line may contain many of the same process tanks that an electrolytic tinning line does, Marc: alkaline cleaning, acid activation, and post treatment dips in anti-tarnish treatments, plus rinses between each step. But in place of the electroplating tank it has a flux tank and a tin dipping tank.
If it's a continuous line, such as for wire, it probably has "wipes" of some sort to smooth out the tin and remove the excess. Good luck with it.
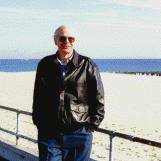
Ted Mooney, P.E.
Striving to live Aloha
finishing.com - Pine Beach, New Jersey
Q. Is "Hot Tin plate" different than Hot Tin Dip?
Casey Heitzmanmetal finisher, Oregon
May 8, 2009
A. Hi, Casey. Unfortunately, people invent ambiguous slang constantly so there is no saying what they might be thinking about when they decided to call it "hot tin plate". But I personally do not know of any other deposition processes that might be called "hot tin plate" other than "hot dipped tin".
Good luck.
Regards,
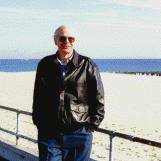
Ted Mooney, P.E.
Striving to live Aloha
finishing.com - Pine Beach, New Jersey
Q. I am working as production engineer in a plant producing cables and plugs for home appliances. On one side of the cable we attach plugs and on the other receptacles with brass materials. We would like to work on tin plating which is very common for both receptacles and plug connections.
Cumhur EsinProduction engineer - Istanbul, Turkey
July 19, 2009
Q. We have a unit here for hot-dip tinning on copper wire, but nowadays customers are asking for Tin plated instead of hot-dip. Please suggest which process is more suitable for copper wire which will be used to make cables.
Thanks
Kannadas
wires & cables - Daman, India
October 15, 2012
![]() |
A. Electroplating is preferred to hot dip tinning when a thinner, pore-free coating or a more uniform thickness is desired. consultant - Cleveland Heights, Ohio A. Hot dipping will give you a much thicker coating than electroplated tin, so it depends from what perspective you are looking. As a customer, I would like hot dipped, as there will be better protection, but from the producers side, hot dipping will cost more in tin. However, hot dipping is easier to do and hence cheaper (I presume you do not have either hot dipping or plating facilities). If you decide to reduce your tin costs and go for electroplating, you have to factor in the costs of a plating line, chemicals and pretreatments. ![]() Trevor Crichton R&D practical scientist Chesham, Bucks, UK |
A. Both hot-dip and electroplating are suitable, and either will work in all uses of tinned copper wire.
The equipment for electroplating is more expensive than for hot dipping. It also usually runs just one wire at a time, whereas hot dipping can have dozens of wires in parallel. Electroplating is only practical for coating large wire sizes, while hot-dip is better for smaller diameters.
Thickness control is better with electroplating, but thickness can be controlled quite well with suitable wipes in hot-dipping.
Hot-dip has lower equipment costs, higher production speeds, and fewer problems. I would use electroplate only for large sizes (> .015" or thereabouts).
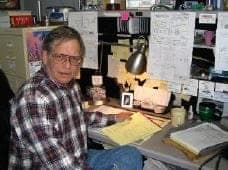
Jeffrey Holmes, CEF
Spartanburg, South Carolina
October 22, 2012
Q. I have a few questions about the processes involved in coating coiled brass strip. I hope you guys can help. :)
My coil is 142 mm wide and 1.8mm thick. Down the centre of the coil at a width of 66 mm, I need a tin strip at approx. 6 microns thick. I have nearly 20 tonnes of this to complete.
It may be that this cannot be achieved. In that case, is there a possibility of 'tinning' the whole strip and then removing the excess off the edges (acid?) so that the 66 mm strip is left down the centre.
It may be easier if the coil were cut into bar lengths and there is a good chance that this would need to happen. Running a long coil through a bath, drying it and recoiling at the other end is a pipe dream. :D
I know this tin isn't just something you can 'paint on with accuracy'. I understand that it doesn't work like that. I need some pointers on the best way to go around getting it 'something like' what I need. Perhaps there are other processes, not necessarily 'tinning' which better suit the kind of thing I need.
Any ideas, pointers, tips or loud laughing noises are welcome. :D
- Birmingham, UK
April 8, 2016
A. Hi Indy. Anything is possible although it may not necessarily be practical. In the electronics industry, "stripe" plating like this is not unusual, and in that case it's done with movable/flexible masking -- a machine is designed with rubber belts that cover the area that you wish to remain unplated while it is in the plating cell. But that is on a smaller, thinner more flexible substrate, and in higher volume.
A second approach is photosensitive masking, as used on circuit boards. The whole strip (or plate if you cut it to length) is dipped or sprayed with a resist that is cured with UV light. Then you wash it off the desired center stripe before plating, and dissolve the hardened resist from the unplated area after plating.
What strikes me as the shortest and cheapest development path, though, would be to cut the strip into manageable lengths and:
a). Apply swaths of plater's tape to the areas you don't want plated, including edges and bottom side. Maybe tape two pieces back to back for less waste; or
b). Build a plating cell approximately 66 mm wide, with no bottom on the cell. Then you lower this whole plating cell onto your brass plate, with some sort of flexible sealant along the bottom edge, fill it up with plating solution, and do the plating; or
c). Similar to "b" but leave off a side wall instead of a bottom wall, position your plate vertically as this last wall, and then use some sort of "jet plating" arrangement rather than filling and emptying the cell."
Finally, I do not mean to imply by any of this that electroplating is better for your needs than hot tin dipping, but the masking issues may be different. It might even be that you can sand and flux the stripe without hot tin sticking to the non-sanded non-fluxed area.
Luck and Regards,
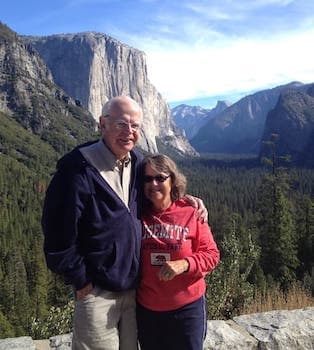
Ted Mooney, P.E. RET
Striving to live Aloha
finishing.com - Pine Beach, New Jersey
Wow! That is fantastic information! Now I can talk like I know a bit about it. Absolutely chuffed to bits with the technical info and standard of response given. Thank you soooooo much!
- Birmingham UK
You're welcome Indy. Even if we can only give food for thought rather than a complete solution, we appreciate detailed real-world problems like yours rather abstract requests to re-post data from books ...
Regards,
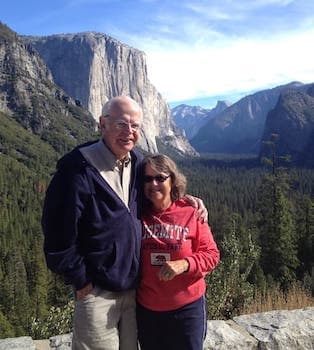
Ted Mooney, P.E. RET
Striving to live Aloha
finishing.com - Pine Beach, New Jersey
A. Hi Indy
I was with Ted - until I came to the bit that said 20 tonnes!
This is a job for a dedicated machine and a shop with experience in tin plating.
In Birmingham, I would put in a local call to the IMF 0121 622 7387 who may know of someone near already set up to do this type of work.
Otherwise there is a considerable market in UK for used reel-to-reel plating plant and a number of plant manufacturers with existing expertise.
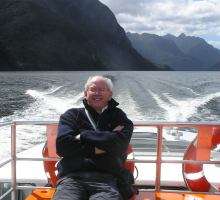
Geoff Smith
Hampshire, England
Q. Hello. I also am interested in making in-house tin plated mild steel bookbinding wires in silver finish. What type of tin is better suited for wire plating at 5-10 microns? What is the best way to clean the bright steel redrawn wire surface to obtain better tin adhesion? Wire sizes are 0.5 mm to 1.4 mm and production approx. 500 kg in 12-16 hours. Any small single or two line used plant available please contact.
Ismail Godhrawalawire - Mumbai, India
July 3, 2016
A. Hi Ismail. Electroplating is almost always preferable to hot dipping if the object is thin decorative coatings. Bright acid tin electroplating is probably the best.
Ideal prep is probably electrocleaning followed by a sulfuric acid dip. However, please don't design based on book knowledge and theoretical information. Have sample parts plated by a plating supplier test laboratory before committing to installation of a plating line. Good luck.
Regards,
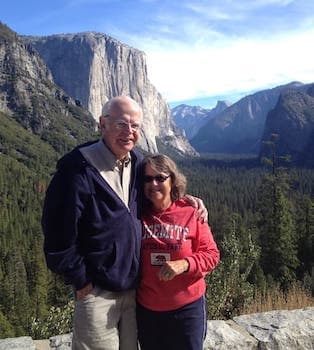
Ted Mooney, P.E. RET
Striving to live Aloha
finishing.com - Pine Beach, New Jersey
Q. Dear Sir/s
I am trying to hot plate Tin on steel flange to be filled with Zinc metal by centrifugal process. We find the bonding of the Zinc and steel not good at a few places with a large gap. Could someone help me with solution.
Thanking you,
- Chennai, India
October 17, 2017
? Hi Vijaya. Hopefully another reader will be familiar with what you are saying, but I have no idea what you're talking about, or what improved hot tin tin dipping has to do with the poor bonding of zinc to steel.
Are you saying that your present process does not involve tinning, and doesn't work well, but you believe that if you hot tin plate the steel then the zinc will be able to bond to the tin better than to the steel?
Please spend a few paragraphs explaining your situation. Thanks!
Regards,
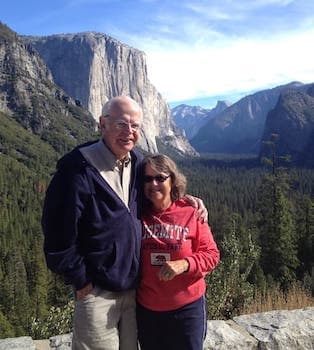
Ted Mooney, P.E. RET
Striving to live Aloha
finishing.com - Pine Beach, New Jersey
Q, A, or Comment on THIS thread -or- Start a NEW Thread