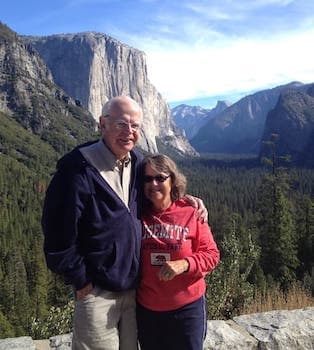
Curated with aloha by
Ted Mooney, P.E. RET
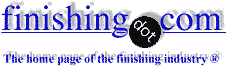
The authoritative public forum
for Metal Finishing 1989-2025
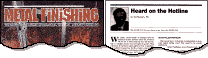
-----
Anodizing on reflectors

Q. We produce projector lamps.
We need mirror reflector. We use aluminum grade 1050. Can this grade be mirror coated? What alloy of aluminum should we use for mirror coating?
Shop - Esfehan, Iran
July 21, 2022
A. Hi Abbas. I am not an aluminum alloy consultant, and you might want to retain one, but 1050 (99.5% pure) should be okay while 1080 (99.8% pure) would probably be better. Chemical polishing / bright dipping followed by a thin layer of anodizing has been used on countless millions of reflectors.
Luck & Regards,
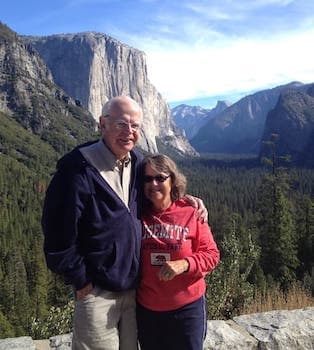
Ted Mooney, P.E. RET
Striving to live Aloha
finishing.com - Pine Beach, New Jersey
A. Hello Abbas
if you want mirror finish for reflectors you will need to use 3002 aluminum material. it will give you the brightness, clarity of image and the reflectivity that you are looking for. You can spruce it up a bit by performing a manual buff/polish on the surface which you are looking to enhance. Unfortunately material like 1100-0 which is pure aluminum or things close to it will not give you the desired results. It will normally only brighten up the material but then turn it a milky white ...e ven if it has been nicely polished prior to processing. If my memory serves me correctly, 3002 was formulated specifically for reflectors. Also be sure to turn the bright dip up to about 220 degrees. 210 is adequate but 220 is better. a 2-3 minute dip in the bright dip tank. The tank MUST be air agitated and don't be afraid to move the bar of parts while in the tank about every 15 seconds. You do not want the bright dip to puddle on the parts as you may then encounter orange peel effect.
Good luck to you
supervisor - Cicero, Illinois
Saporito Finishing Co.

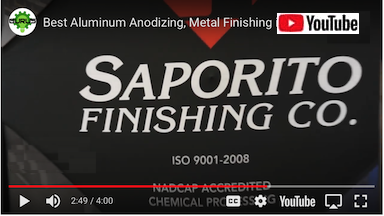
Thanks Philip. I designed a few bright dip installations in my career but never operated one, so your deeper knowledge is appreciated. Now hearing of type 3002 aluminum material from you, I looked it up and you are right of course.
Luck & Regards,
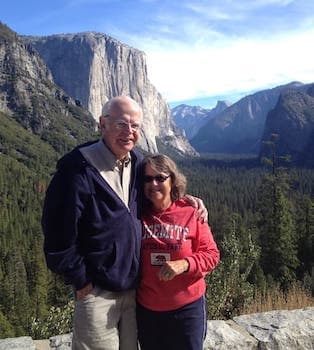
Ted Mooney, P.E. RET
Striving to live Aloha
finishing.com - Pine Beach, New Jersey
⇩ Related postings, oldest first ⇩
Q. We are currently trying to electropolish then anodize aluminum reflectors. Our customer has supplied us with two alloys: 1080 and 1100. When we try to dye the coatings we end up with splotchy results. Can anyone offer suggestions as to the best make-up for the electropolishing solution or, more importantly, the best treatment to use between the electropolishing and the anodizing to prep the surface for anodizing without dulling the parts.
Henry Wolffanodizing shop - Delta, British Columbia
1998
A. The reflectors that I have worked with over the years have predominantly been bright dipped, rather than electropolished. As far as I know, there is no intervening treatment between bright dipping and anodizing.
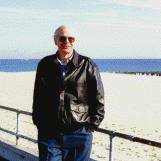
Ted Mooney, P.E.
Striving to live Aloha
finishing.com - Pine Beach, New Jersey
A. A couple quick notes: Ted is right, most reflectors are bright dipped, followed by a short low voltage anodize cycle. When dying standard anodize coatings however, thicker coatings are better, say .75 - 1 mil. Thicker coatings will dull down a shiny bright dipped surface. I have worked with aftermarket bicycle parts, which required a bright specular surface. They were bright dipped, rinsed WELL, followed by an anodize cycle which gave about .5 mils thick coating, then after an initial rinse, rinsed in a pre-dye rinse containing 5 % Nitric for 3-5 minutes. That was followed by the dye, rinsed and they were then sealed in a hot Nickel Acetate solution, followed by a hot water rinse.They needed to be immediately blown dry, and handled with clean cotton gloves. They consistently turned out well.
Ward Barcafer, CEFaerospace - Wichita, Kansas
A. There usually isn't a step before anodizing other than a desmut. This removes surface contamination which could inhibit the anodizing process. 25 - 40% nitric acid or one of the proprietary desmuts usually work. Most interior lighting uses ~0.2 mils anodic coating since the corrosion is minimal. Exterior doesn't go much thicker if any since the reflective surface is usually covered.
Lee C. BranchAlbright & Wilson
1998
A. After electrobrightening, a thin film is left on the part that should be removed prior to anodizing. This will cause dulling and nonuniform coloring . A chrome-phosphoric stripper, about 5 minutes at 180 °F, will remove it. A formula is 20 grams chromic acid and 35 milliliters of 85% phosphoric acid per liter of solution using water.
Also, don't expect the 1100 to stay bright after anodizing since it is only 99.0% pure aluminum. The 1080 should look pretty good.
John PowersConsultant - Pittsburgh, Pennsylvania
1998
Q, A, or Comment on THIS thread -or- Start a NEW Thread