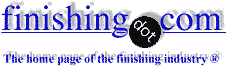
-----
Recommended Al alloy(s)for bright dip & clearcoat anodizing
Can you recommend aluminum casting alloy(s), to be used in Precision Investment Casting (PIC)process which is suitable for bright dip and clear coat anodizing process.
WILFRED DE GANNESindustrial art - Port of Spain, Trinidad & Tobago, West Indies
1998
1998
My experience with bright dipping castings is that they are pretty tough to get a consistently bright finish on, additionally the clear anodize afterward exacerbated the shade differences between individual parts and from part to part. However, that said, generally speaking the issues are related to the porosity, the alloying constituents and the grain structure. Grain structure was a major player in the mottling seen. The finer grain structure the better, perma-mold type castings seemed to give the best grain structure. Porosity must be dealt with as best as possible by alternating hot and cold rinsing at all stages of the cleaning process and after the bright dip. After the anodize cycle which was very short with low voltage, a 5% nitric acid rinse was used to prevent bleed-out. The alloy types which bright dip the best are not the usual ones used for casting purposes. Alloys which contain magnesium as the major alloying constituent are the best bet. Impurities to be avoidedare high silicon and iron levels. Try to find an alloy with iron below .003%, Copper below .05%, Silicon below .05%, and Manganese below .001. The processing step which caused the most problems was extended etch rates. That usually resulted in a splotchiness due to granular boundries being emphasized and also caused the porosity to become opened up. The best resource I could find at the time was a company called Allbright and Wilson. They had a booklet available on bright dipping. I don't know if it is still published, my copy is from 1992. They were very helpful even though we formulated an in-house proprietary bath.
Ward Barcafer, CEFaerospace - Wichita, Kansas
There is another excellent reference book from ASM entitled: Aluminum and Aluminum Alloys ⇦[this on Amazon affil links] which discusses most of the commercial alloys. Castings are tough, particularily due to the soluble components which have a nasty tendency to dissolve in the bright dip baths. Best bet is to contact one of the major aluminum houses, Alcan, Alcoa, Kaiser, Reynolds for a recommendation.
Lee BranchRichmond, Virginia
1998
Q, A, or Comment on THIS thread -or- Start a NEW Thread