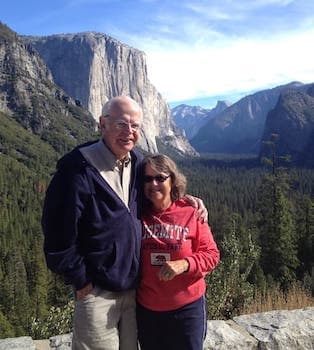
Curated with aloha by
Ted Mooney, P.E. RET
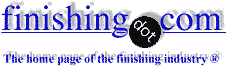
The authoritative public forum
for Metal Finishing 1989-2025
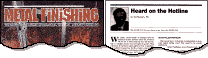
-----
Temperature of acid copper solution
1998
Q. Can anyone give me information as to why bright acid copper plating takes longer during the hot summer months? We are plating small (40mm) diameter lead medals.
- I think that when tanks are at 20 °C they plate perfect.
- At 25 °C they plate slow
- At 30 °C and over, impossible !
Does anyone have the same problem? If so what suggestions can you give me.?
Mick LongMEDALS - Australia
A. It is the nature of the beast. You will have to add cooling coils to keep up quality and production when the air gets warm, or the tank heats up from the passage of current. This information should be available in the Technical Bulletin for the acid copper additives. The higher temperature also chews up brightener, and this creates organic impurities, and the need to carbon treat more often. It would be worthwhile to run the bath at the correct temperature. Please see the finishing.com directory for suppliers.
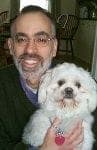

Tom Pullizzi
Falls Township, Pennsylvania
1998
A. Mick:
"The Nature of the Beast" referred to above is well known and can be used to your advantage if you so desire. It is as follows:
Electroplating solutions are actually chemical etching solutions that you force to run in reverse with your rectifier. Especially Acid copper which is heavily laden with 10% v/v of Sulfuric Acid or more. As you have no doubt observed in other systems, as temperature of an etch bath rises, etch rates increase. This is the phenomena you are fighting in the summer months. Acid Zinc baths are even worse than your copper. So on your workpiece, you are trying to plate at say, for example, 20 ASF with temperature cold at 20 °C, and it works fine. You get 20 ASF worth of Copper at the cathode. At 25 °C, the etching of copper off your part is no longer negligible, and probably has a rate equivalent to 10 ASF but in the reverse direction. So of your 20 ASF supplied by your rectifier, 10 ASF's worth of the copper is being etched away by your bath, so you only net out a slow 10 ASF at your cathode. At 30 °C, the etch rate is so high that it may account for greater than 20 ASF, so you net out with nothing at your cathode. Now just imagine what is happening at your anode! It is dumping copper into your bath! Also the organic brighteners may lose their activity or become sparingly insoluble at these temperatures.
How to use this to your advantage? Higher temperatures can support higher rates of plating if you engineer for them. 100's of ASF. Your throughput can increase 100's of %. But it requires a bit more than just turning up the current.
Regards,
Dave
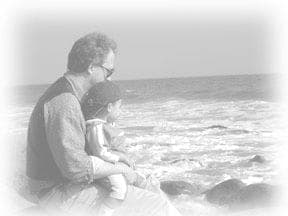
Dave Kinghorn
Chemical Engineer
SUNNYvale, California
1998
Q. WOW Dave !
Your information has really got me thinking, back to the books for me I guess.
As I am new to this type of work I have discovered that previous platers have had great difficulty because current consultants informed them that they could plate at temperatures up to 32 °C.
It's winter now but summer's coming.
Mick Long [returning]MEDALS - Australia
1998
A. Gentlemen,
I agree with Tom. The low efficiency in acid copper plating at high temperature is mainly caused by failure in additive functions. With adequate additives, copper deposition can be performed at around 30 °C.
The chemical dissolution of plated coatings can be ignored in the majority cases of plating. In the case of copper deposition, the acid with complexing agents does not considerably attack copper because the equilibrium potential of copper is more noble than that of hydrogen. Only possible etching results from the disproportional reaction of Cu(++) and Cu to 2Cu(+) at the condition of off-power. This reaction cannot take place under plating. Even for zinc plating, the chemical attack almost does not exist during plating. At the off-power, zinc dissolution cannot reach the rate as high as 20 ASF at 30 °C because the overpotential of hydrogen evolution on pure zinc is very high.
Ling Hao- Grand Rapids, Michigan
1998
1998
Dave:
To prove your assumption that the acid copper bath starts etching the deposit at higher temperatures, try to run this test:
1. weigh 2 pieces of copper
2. suspend them in copper bath samples (in beakers [beakers on
eBay
or
Amazon [affil links] ) maintained at 20 and 40 °C for as long as you think it will take to etch the copper (1-2 hours?)
3. re-weigh your samples
4. let us know if you detect any weight loss of copper
Has anyone heard of copper anodes dissolving in the sulfuric bath without current? - I have not!
Regards from PlaterB
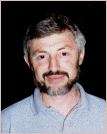

"PlaterB" Berl Stein
NiCoForm, Inc.

Rochester, New York
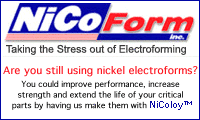
Q. We are currently copper plating with an ideal temperature suggested by the chemical company to be maintained is 25 °C.
Just by normal working our temperature reaches to 40 °C. What is the best, consistent way of maintaining the temperature needed.
Thanks
- Vadodara, Gujarat, India
December 5, 2018
A. Hi Tirath. The tanks require cooling coils and probably a refrigeration system to generate the necessary chilled water. Virtually all of the power which the rectifier puts into the tank is consumed by the resistance of the plating solution, which means that virtually all of that power must be removed for you to hold an equilibrium temperature of 25 °C.
Thus calculate the input power in watts (volts x amps), multiply by the conversion factor of 3.412, and that's how many BTU/hr the cooling coils must remove.
Regards,
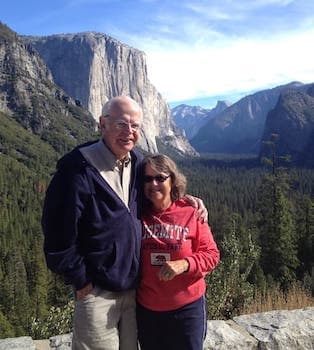
Ted Mooney, P.E. RET
Striving to live Aloha
finishing.com - Pine Beach, New Jersey
December 2018
Q. Thanks for the equation.
Reading the above posts on this thread kept me thinking about a research paper I read that claimed of successfully depositing high amounts of copper at 240 A/sq. ft. with Acidic Bath maintained at temperature 48 °C.
Are the baths functional at such high temperatures?
- Vadodara, GJ, India
December 8, 2018
A. Hi Tirath,
Theoretically acid Cu bath can be operated at 48 °C especially if run at such high current density (240 asf) then higher bath temperature can facilitate ionic movement across diffusion layer between bath solution and cathode surface. However, additives may breakdown to become organic byproducts easier at high temperature to affect deposit ductility & appearance.
Regards,
David
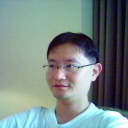
David Shiu
- Singapore
December 25, 2018
Q, A, or Comment on THIS thread -or- Start a NEW Thread