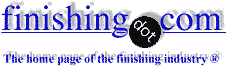
-----
Determination of nitric acid content in acid bath
Q. Hi,
I would like to enquire about how to calculate the Nitric concentration in the acid bright dip bath in Aluminium finishing? As I have been given two different methods.
1. 50 ml H3PO4 + 5 ml Bright dip sample and titrate it with ferrous sulfate
⇦ on
eBay or
Amazon [affil links] until clear %HNO3=no of mls * titration factor * 2.1225 / 5
2.Measure 5.0 ml bright dip solution into a 250 ml clean dry beaker [beakers on
eBay
or
Amazon [affil links] and add 100 ml of H3PO4 and heat it up to 40-45 °c. Titrate it with ferrous sulfate
⇦ on
eBay or
Amazon [affil links] until the first golden brown colour appears.
Let "b" ml be the volume of ferrous sulfate
⇦ on
eBay or
Amazon [affil links] used. and "a" ml is the titration factor of ferrous sulfate
⇦ on
eBay or
Amazon [affil links] against the standard % by volume of 70% nitric acid in the "phospol" = (b/a)*5
From my opinion, I think the 2nd method is the correct one. Can anyone please get back to me?
Another problem, we have a client that orders their aluminium from China then being send to Melbourne. Their aluminium has to be washed in caustic first before being dipped in the acid bath to obtain good finishing. Why is that?
Another problem, we have another client that complains that they are using too much caustic to neutralize their treatment tank. Is there any cheaper way to neutralize their tank? They probably go through about 8 tons of caustic every month. Please advise.
Any advice would be very much appreciated.
Regards,
- Melbourne, Australia
2002
A. Your questions are broad ranging. Not being a chemist I'll leave question no. 1 to others.
Yes, aluminum must be cleaned, and caustic cleaning is the standard. You would need to supply a lot more detail before anyone could hazard a guess of whether an acid cleaning process might work instead.
Caustic is not the least expensive neutralizing agent. hydrated lime
[affil links] would be less expensive on an alkalinity basis, but I would not know whether it's applicable for you.
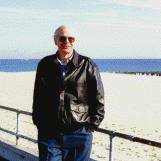
Ted Mooney, P.E.
Striving to live Aloha
finishing.com - Pine Beach, New Jersey
2002
2002
Q. Hi,
I would like to further specified the problem above. About the method of determination of Nitric acid concentration in the acid bright dip bath in Aluminium finishing? As I have been given two different methods.
1. 50 ml H3PO4 + 5 ml Bright dip sample and titrate it with ferrous sulfate
⇦ on
eBay or
Amazon [affil links] until clear %HNO3=no of mls * titration factor *
2.1225 / 5
2. Measure 5.0 ml bright dip solution into a 250 ml clean dry beaker and add 100 ml of H3PO4 and heat it up to 40-45 °C. Titrate it with ferrous sulfate
⇦ on
eBay or
Amazon [affil links] until the first golden brown colour appears. Let "b" ml be the volume of ferrous sulfate
⇦ on
eBay or
Amazon [affil links] used. and 'a' ml is the titration factor of ferrous sulfate
⇦ on
eBay or
Amazon [affil links] against the standard % by volume of 70% nitric acid in the "phospol" = (b/a)*5.br
I still think the 2nd method is the correct one. Can anyone please get back to me?
Problem 2: we have a client that orders their aluminium from china then being send to Melbourne. their aluminium has to be washed in caustic first before being dip in the acid bath to obtain good finishing. why is that? It is not the case if the aluminium is bought from a Melbourne supplier. Yes All the aluminium has to go thru a cleaner stage called 'borax' but for the aluminium that is bought from China , they have to go thru caustic bath before being dipped into the bright dip, they need an extra step and that is taking too much time, why is that?
Problem 3: we have another client that complains that they are using too much caustic to neutralize their treatment tank. Is there any cheaper way to neutralize their tank? They probably go through about 8 tons of caustic every month. The caustic is used to treat the waste water and overflow from the aluminium anodising plant. it is merely acid bath, sulfuric acid, caustic bath and etc. Is caustic the best way to treat the waste water? Is there another efficient method to reduce the amount of caustic being used to treat the waste water? Please advise.
Any advice would be very much appreciated.
Regards,
- Melbourne, Australia
A. I'll try the first question.
Firstly the ferrous sulfate
⇦ on
eBay or
Amazon [affil links] is not stable and requires regular standardization. Suggest you make up a electropol solution without any nitric then add a known amount say 5% and then make your own factor for the ferrous sulfate
⇦ on
eBay or
Amazon [affil links] to the same end point. The titration requires the solution to be heated.
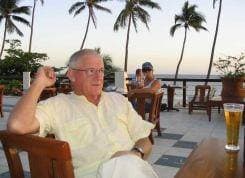
Geoffrey Whitelaw
- Port Melbourne, Australia
2002
![]() |
A. Hi, Joe. Problem 2 probably relates to "etching" rather than cleaning. It is possible, I suppose, that the local company is etching before shipping the product to your client. Then again, who knows if it's even the same alloy. ![]() Ted Mooney, P.E. Striving to live Aloha finishing.com - Pine Beach, New Jersey 2002 Q. Hi, Geoff Whitelaw, - Melbourne, Australia 2002 A. I use 5 mls of the bath to 95 mls of DI. Add 5-10 drops of phenolphthalein ⇦ on eBay & Amazon [affil links] into the beaker, put on a stirrer. Titrate with 1.0N sodium hydroxide solution and wait for a solid red color. Calc. is: 1.34*vol. titrant= Nitric concentration (%) Bob Forrest- Port, Maine 2002 |
A. ferrous sulfate ⇦ on eBay or Amazon [affil links] oxidises in air.How fast depends on air above surface of storage bottle. You can actually minimize by using a flexible bottle and squeezing to eliminate air from the bottle. How often depends on how accurate you want to be. The reaction is not instantaneous so warming fastens reaction rate and makes titration viable
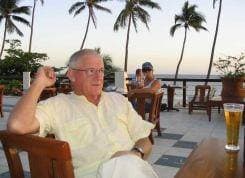
Geoffrey Whitelaw
- Port Melbourne, Australia
2002
Q, A, or Comment on THIS thread -or- Start a NEW Thread