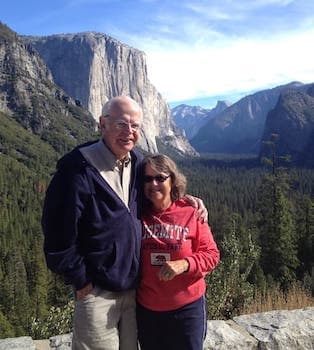
Curated with aloha by
Ted Mooney, P.E. RET
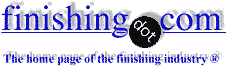
The authoritative public forum
for Metal Finishing 1989-2025
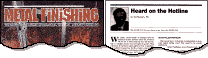
Thread 168/49
Seeking method to control HF concentration in Titanium Chemical Milling Operation
Q. We forge medical implants from a variety of materials. In our titanium forge process, the parts are "etched" or chemically milled to reduce overall dimensions, dissolve any alpha case and expose any indications to be more easily found at FPI (Fluorescent Penetrant Inspection).
Our problems are in the acid room where the chemical milling takes place. We are having a very hard time controlling the acid concentration (nitric & hydrofluoric acid), and do so now by monitoring the etch rate and when it gets too slow we adjust or dump the bath.
We would like to install a monitor/control device(s)that would allow us to measure some parameter and when that gets low, a valve would open and trickle in hydrofluoric acid. Now the parts are rinsed right over the tank with water. Currently the operators drain some of the acid solution when the level gets too high. We've thought, with the help of several vendors, that the possible parameters we may be able to monitor and control may be pH, Bath Conductivity, Fluoride ions with Fl specific probes, etc. We cannot find literature or expertise on this subject. Granted it seems like a difficult dilemma, considering HF's ability to attack glass probes and other mechanical contacts.
Thanks in advance for any help
- Lansing, Michigan
2002
publicly reply to Michael Diotallevi
A. To the best of my knowledge, there is no such device available. pH is not a practical way of controlling it since it is logarithmic--A tiny pH change requires a huge amount of acid- and it only gives total acid. Titration is quick and fairly easy-- a modest amount of training by a very good trainer- But, it only gives total acid also. Titrating for fluoride ion using a thorium chemical gives total fluoride ion and the darn stuff is a very weak radiation emitter. Not bad enough to be harmful with the tiny bit of care, but is a nightmare to dispose of AND it just might possibly require a license from the NRC or state. You can do a very good estimate of "available" fluoride , which is what you are interested in by using a selective ion fluoride electrode. Orion, now Thermo Orion, is my choice. It requires a better than average pH meter with a good mV range and accuracy. This method requires some trial and error and/or a consultant and some good to very good training by a sharp floor person or a chemical technician.
Unfortunately, fluoride complexes with titanium, typically, one Ti ion will tie up 6 fluoride ions. Without going into advanced inorganic or physical chemistry, The more Ti that you get in solution, the slower the reaction goes! 12 grams per liter will take ten to twenty times longer than one gram per liter.
Rinsing over the tank, other than a short mist, is a pain, a big pain to try and keep the tank in a good operating limit, since there is virtually no evaporation. You will not need a great deal of precision, but time is money and dumping is expensive (waste treatment costs).
- Navarre, Florida
2002
publicly reply to James Watts
A. I am in agreement with Mr. Watts here. We use the same process for alpha case removal in the aerospace industry. Etch rate is the most important factor. Do you assure the alloy is the same material and condition as the hardware...and "co-processed" through this same heat processing (welding, heat treat, etc.), since you are generating alpha case. In addition to your bath chemistry, review your temperature control and the ratio of your hardware surface area / mass to the tank volume. Your ventilation system could be a factor...years ago, I monitored a similar hydrofluoric/sulfuric anodic etch bath...small volume and a very "aggressive" exhaust system in place....I swear it sucked out my HF...had to adjust it three times a week. The fluoride selective ion method is probably the most effective. The thorium nitrate titration is effective, but takes some skill; the titration itself is simple (be sure to use Nalgene volumetric ware, but the endpoint is not sharp. I believe the method is in the Metals Handbook (?). Yes, its radioactive...but so is granite. Check with your state EPA for disposal...your lab may be exempt for small amounts. I did, however, go ballistic when I caught one of my technicians mouth pipetting thorium nitrate solution!
Douglas A. Hahn- Mason, Ohio
2002
publicly reply to Douglas A. Hahn
A. I have seen a two stage simple acid base pH titration for Nitric and Hydrofluoric. Titrate with 0.1N NaOH ⇦ this on eBay or Amazon [affil links] for the Nitric to one pH then use 0.01N NaOH to a second Higher pH because of the much lower concentration of HF. Unfortunately I can't remember off the top of my head the PH end points. I will have a look and if I get back post them.
Ciaron Murphyaerospace - South Wales, Great Britain
2002
publicly reply to Ciaron Murphy
A. Hello fellow tank jockeys:
Do you consider making chemical corrections three times a week excessive? In electronics manufacturing it is done continuously! Anyway, Free fluoride ion is commonly done by ISE (Ion specific electrode.) About $2000 in gear gets you a basic system and calibration is a bit temperamental. It is also very temperature sensitive as it measures an equilibrium value of Fluoride across a membrane which is very temperature sensitive. It can be mounted in-line and monitored continuously, but you'll need a chemist to study how it interacts with your particular process, then set up rules for usage. Most people don't consider this and simply junk the gear the first time a false reading is reported. Nitric can also be picked up by ISE. For overall etch activity, Oxidation potential can be determined by a Platinum electrode with internal reference. Waste titanium can be determined spectroscopically, colorometrically, XRF, maybe even by specific gravity. The trick here is to have a chemist study how each of these instruments interacts with your process and tie the results to reaction rate, then determine process control rules from this "envelope" based on your material specifications. All these instruments can be very accurate over small ranges of variance. Control within that range and your parts will come out perfect every time.
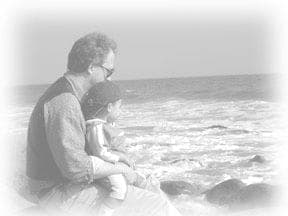
Dave Kinghorn
Chemical Engineer
SUNNYvale, California
2002
publicly reply to Dave Kinghorn
adv.
Why even consider such hazardous method if we can reduce overall dimensions or even electropolish medical implants of titanium or other alloy in environmentally safe solution - takes only few minutes and no fumes are released.
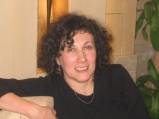
Anna Berkovich
Russamer Lab

Pittsburgh, Pennsylvania
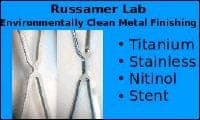
2002
publicly reply to Anna Berkovich
A. I believe a continuous monitoring system for your etch bath might be devised as described below. You might find something commercially available that could be modified to do the job. [deleted by editor]
A small dual channel peristaltic pump would remove liquid from the etch bath. The same pump would pull a buffer, "TISAB", from a reservoir. The two liquids would then be mixed by passing the mixture through a helical coil.
Conventionally formulated "TISAB" contains a complexing agent, CDTA. This is intended to liberate the fluoride from complexes that it forms with ferric, aluminium, and other metals so that a more accurate value is obtained for the total fluoride concentration. For a reason I'll give below, it would be better to omit this ingredient from the "TISAB" for this application.
Because the "TISAB" addition raises the pH into the 4 - 5 range, a precipitate will likely form when the two liquids were mixed. So, the mixture would need to be passed through an on-line filter to remove the solids. Lastly, the clarified liquid would be run past a fluoride ISE and a Ag/AgCl reference electrode, fitted with a flow through cell. The voltage across the two electrodes will be related mathematically to the fluoride concentration. Since what is sought is not the total, but the "free" fluoride concentration, the omission of the CDTA would leave the complexed fluoride bound to the metals such that it would not affect the reading, or at least not much.
The voltage generated by the electrodes could then be wired to a conventional controller unit. Just as the voltage from an ORP probe is used to regulate the addition of treatment chemicals to chrome reduction and cyanide oxidation processes, this controller would regulate the addition of fresh HF to the etch bath. I realize that this is all fairly hypothetical. But I have little doubt that such a system could be constructed. Whether it would be cost effective is another question! In any case, I think it would be worth a look. Hope this has been of some help.
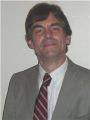
Dave Wichern
Consultant - The Bronx, New York
2002
publicly reply to Dave Wichern
----
Ed. note: Regrettably, we had to delete the helpful vendor suggestions that Dave offered because -- as almost always eventually happens -- it led to suppliers posting ads. Offering brand names often causes friction, spamming, and even fictitious postings from 'satisfied customers'. Plus, this site needs supporting advertisers for it to be possible, and none will pay for posting ads by and testimonials to their competitors who choose not to bear any portion of the cost :-)
A. Unfortunately the SIE is not like a pH probe in this case. At the concentrations that I used in the lab, the mV would drop to a point and reverse. The rising mV lasted longer than I could accept and the Orion rep said to use the reversal point. Reproducibility was very good. It also is quite temperature sensitive. It would be interesting to see how long the electrodes would last and what variability and accuracy it would have. The nitric/HF ratio must be kept in reasonable ranges or pitting can/will occur. I think that I would look at daily analysis in preference to automated. If a system is "automated" it is checked less and less as time goes on, so the first indication of an Oh-OH is a scrapped batch/batches.In plating, you just strip and rerun. Here, we are talking about scrap.
James Watts- Navarre, Florida
2002
publicly reply to James Watts
A. Our company has been in the business of milling Ti castings for about 35 years. We also us a HF/HNO3 solution. To maintain control of our solution we have the solution tested once every 24 hours and make adjustments based on that test. It is not the most advanced system on the market, but it does work. Good luck.
Jack Davenport- Portland, Oregon
March 30, 2008
publicly reply to Jack Davenport
Q. Hi,
I just began a contract assignment with the Center to assist with a project to extend acid bath (HF/HNO3) life for chemical milling of titanium. Some initial work has been done with an attempt to use an additive to precipitate the titanium compounds and remove them by physical treatment. If you have any experience in this regard I would appreciate the opportunity to discuss it with you.
The data from a series of trials using the additive have yielded lower removal rates of titanium than anticipated - perhaps due to the existence of titanium complexes that interact slowly or not at all with the additive. I'm particularly interested in learning about the chemistry of titanium in an HF/HNO3 milling bath environment if you can direct me to any sources.
Thanks,
Dick Poduska
- Rochester, New York
November 21, 2008
publicly reply to Richard Poduska
A. I have found that a reasonable control of Etching with HF is using a cooling bath and controlling the temperature at 20 °C ± .5 °C.
Bernie Newman- Fenton, Michigan
February 24, 2009
publicly reply to Bernie Newman
Controlling Dissolved Titanium in Etch Solution
Q. I am interested in finding a cost effective way of removing dissolved titanium from an acid etch solution (HNO3/HF). I believe controlling the concentration of Ti4 serves to stabilize the performance of the etchant.
Matt Homuthtitanium anodizing - Lakeville, Minnesota, USA
February 21, 2017
publicly reply to Matt Homuth
Q, A, or Comment on THIS thread -or- Start a NEW Thread