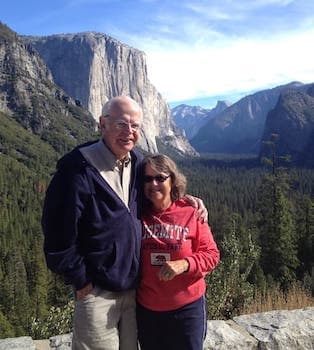
Curated with aloha by
Ted Mooney, P.E. RET
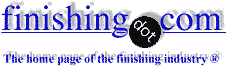
The authoritative public forum
for Metal Finishing 1989-2025
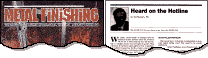
-----
Good Conductive Black Finish for Aluminum?
Q. I recently had a batch of parts (6061 aluminum) plated 'black zinc' with the understanding that it would provide a reasonable cosmetic finish and still be electrically conductive. They were underplated with copper I believe.
The finished surface is not electrically conductive at all, however, it can be pierced with probes to get to conductive layers underneath. Was my assumption incorrect or is there a more specific process to use to achieve a dark or black finish that is electrically conductive.
- Portland, Oregon
2002
A. Take a look at Black Electroless Nickel plating.
Todd Osmolski- Charlotte, North Carolina, USA
2002
A. Consider black chrome.
Conversion coatings [the black chromate conversion coating on the zinc] detract from surface conductivity and give variable, unpredictable results. Using a more metallic black coating such as black chrome might do the trick.
Todd's suggestion about black nickel is worth checking on; however, beware that the zinc sulfide post-nickel plating conversion processes as these have the same drawback as zinc chromate conversion coatings.
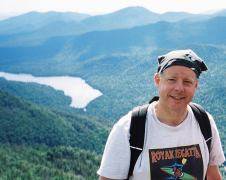
Milt Stevenson, Jr.
Syracuse, New York
2002
A. You said that there was no conductivity at all, is there any chance that your parts were black anodized, and not black zinc, Everybody is correct about conductivity varying but usually there is some.
Hope this helps,
plater - Charlotte, North Carolina
2002
Thank you to all for your responses. The plating source I have been using claims that black chrome is also non-conductive (the same source that was surprised that black zinc was not conductive). Responses here indicate otherwise and I have sought other sources to corroborate. It appears that many black chrome applications are top-coated for preservation, others are oiled. Those options would certainly compromise the conductive nature. The prior finish was indeed black zinc but apparently the black pigment was so concentrated that it greatly affects the zinc. I'm not a chemist so I cannot clarify or defend the claim. Existing parts are being stripped, adding a chromate conversion, masked in key areas, and having black anodization on the surfaces that can allow non-conductivity.
Again, many thanks for the wise perspectives offered in this forum.
- Portland, Oregon
2002
Multiple threads merged: please forgive chronology errors and repetition 🙂
Q. I am looking for a black color surface finish on aluminium alloy which is electrical conductive. Please kindly advise. Thanks.
Angus Chow- Hong Kong
2002
![]() |
2002 A. Angus: Several options exist: 1) Black Nickel (provides a dark grey to midnight black finish) 2) Black Chrome 3) Black Chromates These finishes are all commercially available. Mike Barnstead- Waterbury, Connecticut A. We apply both black nickel and black chrome over electroless nickel when aluminum parts need conductivity that black anodize can't provide. It's an expensive option, however, works! Also, there are several conductive paints that might fit the bill. ![]() Milt Stevenson, Jr. Syracuse, New York 2002 |
Multiple threads merged: please forgive chronology errors and repetition 🙂
Conductive black finish for Aluminum or Stainless for Vacuum E-Beam Application
2005Q. I work in the semiconductor industry and in our inspection tool there is a microscope that inspects for defects. It works well until the Field of View of microscope approaches a aluminum bar. Then we get reflective light from the top cover of the Bar. Current cover is bare aluminum sheet metal. It is not possible to move bar as it is integral part of equipment.
Tests show that a dark colored cover on bar reduces reflective light allowing for a clear picture. Easiest solution is to anodize the AL black however there is another factor. The entire system is inside a vacuum chamber and anodizing is a no-no in vacuum (high outgassing). Also, the Electron Beam which does the actual inspection can charge up the non-conductive anodized surface.
So the application is a conductive, black or dark colored finish for Aluminum or stainless sheet metal that is compatible inside a vacuum chamber.
We have had so-so experience with graphite paint on metal. However, this kind of surface treatment is not very sticky and can be easily wiped off by touching or when cleaning the bar.
Sorry for the long winded description, however I think it best to know all factors working here.
Thanks for your help,
Semiconductor Industry OEM - Santa Clara, California, USA
A. If this is an optical microscope, try using a polarizing attachment if it does not already have one.
A very thin coat of calcium modified zinc phosphate might work also. Should completely dehydrate at a relatively low vacuum.
- Navarre, Florida
2005
Q, A, or Comment on THIS thread -or- Start a NEW Thread