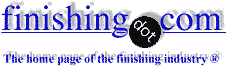
-----
Powder Coating Shrinkage on Edges
Q. My company manufactures snowplows and earthmoving attachments and outsources the powdercoat finishing of these products. Our powder coat job shop has a problem with getting adequate coverage on the outside edges our product. For example, there are 1/4" thick support ribs, that when painted and cured, have a thin grey line along both edges of the part. When exposed to the elements, these thin lines quickly rust. Note: The ribs are cut on a laser which produces a very distinct 90 degree edge.
I have brought this problem to the attention of my paint contractor and have asked them to increase the coverage on these areas, but they tell me that all paint tends to shrink away from the edges during the curing process and increasing the coverage is not the answer. They have also suggested that we round the edges of these parts to eliminate the sharpness of the edge. This is not an acceptable recommendation as it would take considerable time and effort to accomplish this task.
Currently they are looking for other powder formulas that may tend to shrink less and provide the coverage we need.
Is this a correct approach and if so, is there any stock powders available that will solve this problem. If not, are there any other suggestions?
Cal Niemela- Calumet, Michigan
2002
A. Hi Cal!
I am not sure why your coating supplier is telling you this information. During the powder coating application, the electrostatics usually tend to apply more powder to the edges than the flats. You can usually see this on most powder type properties. Especially when using a TGIC as I assume your using for outdoor use. The more likely candidate for suspect in your case would be that the 1/4" stiffener/rib was laser cut.
The plasma machine was adequate until customers started asking for closer tolerances and straighter edges. The running speeds are faster too. Plasma usually leaves burrs that needs grinding before topcoats. The two most common methods for removing laser smut/carbon are mechanically and chemically. The residual material that is left by the laser must be removed before topcoating or you will have premature topcoat failure. I think the chemical (acid) removal method is probably the easiest to implement. My guess is that once you remove this material, ! you will notice the powder attracting to entire areas previously suspect and you will eliminate the premature paint failure.Many companies use hydrochloric acid to eliminate the laser smut. Lastly, remember that if you use high acid concentrations to clean with, you need to watch out for premature flash rusting.
![]() Bob Utech Benson, Minnesota |
![]() Ed. note: Bob is the author of: "High Performance powder Coating" on eBay or AbeBooks or Amazon [affil links] |
2002
"You don't need a weatherman to know which way the wind blows" -- Bob Dylan
A. This by way of saying that although Bob Utech is far more qualified to answer your question than me, I have seen this thin-at-sharp-outside-edges problem. When parts are powder coated then plated, forexample, you can count on seeing plating "trees" building up along the edges/corners. I understand that outside edges get the most plating current, but still, the trees can't be there unless the coating is perforated, and that always seems to happen along sharp outside edges as the powder melts and fuses. Surely something about the cohesive contraction causing a tension and thinning at corners.
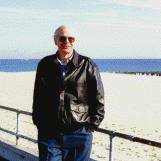
Ted Mooney, P.E.
Striving to live Aloha
finishing.com - Pine Beach, New Jersey
2002
A. Cal,
This problem is not real unusual in the brighter colors: Reds, oranges and yellows. Because of the cost of pigments especially in heavy metal free powder formulas, some manufacturers try to keep powder cost down by reducing the amount of pigment and using less expensive fillers.
I have seen the edges show through on Safety Yellow that was applied at 4 mils. Other powders will have full edge coverage in Safety Yellow at 1.5 to 2 mils, BUT the price of the powder is significantly higher. Because you are having the work done through a job shop who most likely uses the same color for other customers, they are probably reluctant to change to a higher cost powder because they would not be able to increase the price to their other customers.
If you have a large enough volume of work, they should be able to work something out. If not, then you either need to find someone receptive to doing the work and finding a powder to solve the problem or bring the work in house, which would require purchase of a powder system, but you would have total control.
This problem occurs on sheared edges as well as laser cut. We have been seeing a lot of laser cutting shops adding an additional two stages to their washers to chemically remove the burr/slag left by the laser cutting. This is generally on only one side. This will not stop the edge show through except if it is due to the slag. It is the nature of all powders to pull away from the edge somewhat during cure due to surface tension issues.
Tom Binney- Wisconsin
A. Although I am not a plater, I am convinced that Ted "hits the nail on its head"(old dutch proverb). It is a well known fact that the thickness (DFT) of a coating - at a sharp edge- is less than the thickness at the flat. This effect is stronger with liquid paint than with powder. During the drying/curing the coating "shrinks" (solvent evaporates, due to melting and crosslinking the spec. density of the layer increases and therefore less volume is left).
This means that a) the dft at the sharp edge is less and b) there exists an internal tension in the coating-layer possibly causing micro-cracks. Probably the cause of the trees Ted described. Yes, one can notice a layer building up at the edges of thin sheets, but also there the dft AT THE EDGE is less than the one at the rest. To see this yourself, simply make a crosscut and look at it through a magnifier (20x will do). But..... we are not talking about thin sheet but material of about 6 mm thick, an enormous distance compared to the dft of the powder (60 -100 microns).
Remedy: ROUND THE SHARP EDGE before powder coating! How? The powder coater has to remove the laser scale/oxides anyhow (provided lasercutting was done under "normal" gas)before applying the coating. I presume they did, otherwise Cal would have more corrosion problems than just at the sharp edge. If the coater uses any mechanical system (grinding, blasting) normally the edge is rounded sufficiently. If he uses a chemical system like pickling the rounding effect will NOT be enough. In such a case the job-shop and the client must come to an agreement, one of the two has to do it. Normally it ends up that the producer of the part performs this because he is better equipped (a simple hand-grinder is enough) and he knows what is allowable for his product.
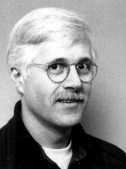
Remmelt Bosklopper
- Enschede, The Netherlands
2002
A. I agree that some non-electrostatic and many liquid paint systems have less edge coverage. You are right that it can be caused by solvent evaporation and paint shrinkage that pulls away from the edge, however this is not true of powder systems. In general, powder will "usually" have more edge coverage than not. This is especially true if the part has a recess or a channel on its surface, the electric field will follow the path of the lowest resistivity to ground (i.e. the edges). Therefor, with most of the electric field concentrating on the edges, powder deposition will be greatly enhanced in these areas and the edge coating layer will build up very rapidly. This is one reason that you find back -ionization occurring at the edges first. There are instances of Faraday Cage areas that may not accept powder no matter how much powder is applied. Take some 3x5 test panels and spray up 2 or 3 at different film thicknesses and you will visually see the increased edge thickness.
![]() Bob Utech Benson, Minnesota |
![]() Ed. note: Bob is the author of: "High Performance powder Coating" on eBay or AbeBooks or Amazon [affil links] |
Multiple threads merged: please forgive chronology errors and repetition 🙂
Powder coating is too thin at sharp corners
Q. Dear sir/madam
I want to know how can to control to gain a certain thickness on sharp area of goods when powder coating?
employee , engineering - Tehran, Iran
August 30, 2008
A. Dear Faribia
if you want make a good control of the powder thickness specially at the sharp edge you have to make a control in KV of the guns , distance of guns from the surface of parts , your earth of the conveyer , the quality of the powder , the speed of the gun reciprocator , the speed of conveyer chain , the quality of the air line
if all these point are ok you will have a good film thickness in all points at the part surface
best regards
- Cairo, Egypt
September 16, 2008
Q. I need the edges of my parts to have a heavy build. Of course, there are powders that are much better than others at holding onto edges when surface tension tugs at the coating during the melt-densify-cure cycle, but they all flow to some extent. Regardless of how thick the initial powder may be on the edges, it will become thinner there than on the flats after curing.
Rounding the edges seems like something that should improve the situation, and I would like to try it.
Now, I wonder if anyone has or knows of any data about how round the edges should be? Should the radius be the same as the coating thickness? Half? Twice? In the case of sheet metal, should it be related to the metal thickness? Or is a certain radius good for any coating thickness, like maybe 0.003"? This is an important question, because it wastes time and resources to deburr more than necessary.
I am sure a precise answer will have to consider the surface tension and viscosity during cure, and the period of time available while the coating can flow, but maybe a useful rule of thumb is out there somewhere.
- Columbus, Ohio, USA
March 25, 2010
A. According to my experience, deburring is not solution but you have to do it. The easy way is after curing the paint, paint the edges again and cure it. The second solution is, rounding edges with oscillation sanding machine. And after applying the paint. The sand will be 50 or 80 (aggressive sand). Another way is wrinkle paint ⇦ on eBay or Amazon [affil links] . Wrinkle or textured paint can be used after deburr operation.
Okay, the solution is very interesting but I will share with you. First you have to take the burrs with oscillating sand machine, standard sanding machine is inefficient. Second you will speak with good static paint manufacturer they will increase the viscosity of paint with extra materials. In my country 3 different paint manufacturers did it. After if you are using primer type static powder you will check the paint thickness, if thickness is so much, you will clean with pressurized air, after you will make painting again. After conclusion is excellent. Durability of paint under salt test 1000 hr without scratch. Regards,
Dr. Burak DALCI- ISTANBUL, TURKEY
November 17, 2010
Cured powder is thin on edges of sheet metal part
Q. Polyester cat yellow top coat is thin on edges of sheet steel parts. Gray metal is visible at corners.
tom spear- racine, wis. usa
August 19, 2016
![]() |
August 26, 2016 A. Yellow has poor opacity, and often requires two coats. ![]() Geoff Crowley Crithwood Ltd. Westfield, Scotland, UK ![]() A. In our shop we have found that anything less than a .04 radius on any material that we use (20 ga - 3/4" HRS) causes major issues at the edge. It also has to do with the color and gloss level of the powder, quality of the gun, ramp time on curing parts,and prep work. For instance, Yellow, Red, and Orange powders with a 90% or better gloss level really take some adjustments on the coater's part to not have light spots on the first coat even on flat areas. The higher the gloss level the higher the flow rate of the powder, thus the more it will want to pull on corners. If I'm having issues with a part I will preheat for 10 min or so, pull the part out of the oven and shoot the inside and out side corners within a few min. This will instantly set to that area of the part, then at around 120 degrees I shoot the whole part again. This usually takes care of it. This too takes some practice because you don't want to build the powder too much on the corner either -- that's just as bad because the powder will simply break off the corner. Usually if I'm doing a custom part and I see corners that are going to be a problem, I'll shoot a powder with a lower gloss and shoot a high gloss clear over it. The lower the gloss of the base coat, the less it will pull at corners and build at edges. This is just what I've observed and works for me ... doesn't mean it's right. CHRIS COOK- columbia, Tennessee,USA August 26, 2016 |
Q. Chris that's a good idea to pre-coat the bits that will end up thin. But how do you ensure inter-coat adhesion?
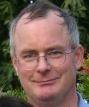
Geoff Crowley
Crithwood Ltd.
Westfield, Scotland, UK
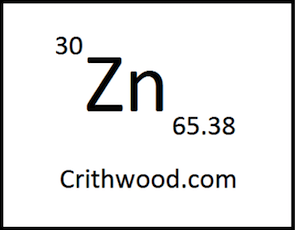
August 29, 2016
A. The layers of powder will flow together until a full cure schedule is done and crosslinking occurs. I hardly ever do a full cure on basic polyesters or TGIC powder until my final coat including clear. This basically makes all the powder bond together. There are some exceptions to this, Chrome being the biggest. I found that a full cure on a chrome base before the clear increases the brightness of the chrome tremendously. Metallics that are dry mixed with a lot of flakes need a full cure. And dormants, Neons and fluorescents seem a bit brighter with a full cure before clear but not much. And super durable polyesters.
I can tell a big difference when I'm stripping parts I've done a partial cure until the final coat. It takes forever in the best strippers where with a full cure on multiple coats it still takes a while but you can see the different layers stripping off. That's just the way I do it and it seems to work very well for me. I've had people tell me to scuff the powder before recoating but I couldn't tell any difference when I did. I keep a small hand held MAP gas torch by my booth and it's been a life safer on corners and welds. If it gives me problems I'll hit the corner for a second with the gas and remove my deflector tip and powder will lay right in there. Again this is just what I've found works for me .
CHRIS COOK- HOHENWALD, Tennessee, usa
August 29, 2016
Powder coating on small machined parts is thin on chamfers
Q. I am coating small machined parts with a mid quality yellow top coat. The parts are typically 1 to 3" long with diameters of 3 /4 to 1 .5". The parts are chamfered and drilled through. Parts are racked and suspended from wire loop ended hooks or small "C" hooks. Pre- treatment is within spec. Parts are manually coated and appear over thickness before cure in a radiant oven. Cured powder is thick on ends and sides, but thin on O.D. chamfers. The volume is huge and there is no margin for a second coat. I had fewer problems before I added more radiant emitters to the cure oven. Cold weather seems to lessen the problem. Or am I fooling myself ?? I run multiple colors with short gaps between colors and different customer's parts. I coat spray-to-waste, all virgin powder. Due to pre-treatment issues, the conveyor never stops but line speed is varied for different parts and presentations. Overbake is rare unless line is stopped. Am I ramping up part temperature too quickly or slowly? HELP !!
Tom SpearPowder coating manager - Racine, Wisconsin U S A
November 1, 2016
Q, A, or Comment on THIS thread -or- Start a NEW Thread