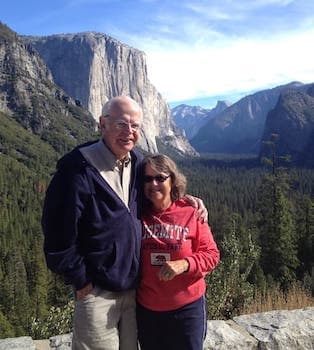
Curated with aloha by
Ted Mooney, P.E. RET
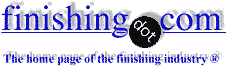
The authoritative public forum
for Metal Finishing 1989-2025
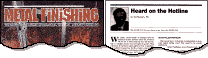
-----
Too Difficult to Passivate on Site; need alternatives
2002
We purchased two (2) ASME stamped 316L vessels, they are 10" SCH 10S pipe. The vessels were welded to a carbon steel skid (see poison pad) and the skid delivered to the client. After a rain the vessels rusted as seen in the attached picture.
According to the vessels manufacturer the material is 316L, as noted in the U-3 Manufacturers Certificate. According to the U-3 Certificate the pipe is A-312, which should be free of scale and contaminant iron particles by pickling, blasting, surface finished or bright annealed. The welding procedures indicates E316L filler metal. The manufacturer assures us that stainless steel brushes were used, but as you can see the heads, the shell, the name plate, the poison pad, and some welds are rusting. We don't understand why there is rust in places far away from welds and why there is rust in the nameplate (there is no rust next to the weld for the nameplate). Note that the weld from the support-arm to the vessel-poison-pad is not rusted, this was done by another shop that put the skid together.
The skid has been delivered and set in place inside a building, the walls should be up by now. Applying nitric acid or citric acid will be difficult since there are pipes, beams and equipment under the vessels and the acid could attack the carbon steel and the concrete. In your forum I have learned that nitric acid will passivate stainless steel but will not remove the rust. To do that hydrofluoric acid needs to be added. Will citric acid remove the rust and passivate the vessel, will it work in this case, the rust in the name plate looks that is "deep".
Someone recommended "Wedac", which is phosphoric acid. Will it work?
Sandblasting will be difficult, specially with the rotating equipment near by.
Can a primer or rust-inhibitor be applied? If so what kind of paint/primer is recommended. Will the paint provide a non-corrosive environment, or will the pitting (galvanic corrosion) continue? Does the rust need to be removed? Can the rust be removed using ScotchBrite wheels or pads and then painted. Any precautions with the rust dust while removing it so that other parts are not contaminated?
Are there any other possibilities.
We are not sure if there is contamination inside the tank. The product in the tank is a water/alcohol mixture.
Your suggestions are appreciated.
Walter Siebold- Houston, Texas
2002
You have a couple of options here. I believe the problem is from a power brushing operation, with brushes constructed from carbon steel, 302 or 304 stainless steel, all of these materials will give you the "rust bloom" you are seeing. I have duplicated the effects you see with the types of bristles I listed and verified the following treatments with salt spray testing.
1 Nitric/Hydrofluoric pickling gel
2 Brush electropolishing
3 Scotch Brite abrasives followed by citric gels
4 220 grit aluminum oxide blasting followed by citric gels
5 sintered ceramic bead blasting followed by citric gels The area someone else performed welding on that didn't have rust, was probably due to the fact they had proper finishing procedures.
All of the above listed will fix your problem, I would go with the brush polishing, it's easier to deal with the waste material and very effective. Better yet have a shop that specializes in field treatments and share the cost with the Fabricator. In the future specify de-scaling with Scotch-Brite type abrasives or 316L bristles if power brushing, the best would be to have the vessels pickled after construction.
Regards,
Bradford P. Maasfood technology - Northfield, Minnesota, USA
Dear Walter,
The stainless steel 316 type intend to protect chemical attack and not Atmospheric corrosion which is look like to happen in the picture. Till the walls of the building are not ready do not do anything .
After the building is ready and the atmospheric corrosion won't be a problem anymore , remove the rust with passivation paste, a common stainless steel passivation paste consist of Nitric and Hydrofluoric thick paste will remove and repassivate the vessels.
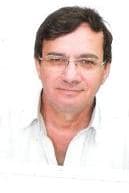
Yehuda Blau
YB Plating Engineering and Quality - Haifa Israel
2002
I agree with Brad on all counts. We have also verified that you cannot use 302 ss brushes on 316ss surfaces, if that is what happened.
We have had great success with this kind of problem using heated citric gel, but you need to somehow be able to rinse it off. With the layout of the equipment you may have to go to the brush electropolish to eliminate the need for a lot of rinsing anything off the surface and onto the steel and concrete.
Let us know if you need help.
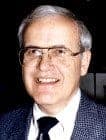

Lee Kremer
Stellar Solutions, Inc.

McHenry, Illinois
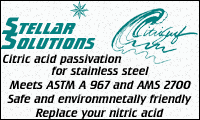
2002
Q, A, or Comment on THIS thread -or- Start a NEW Thread