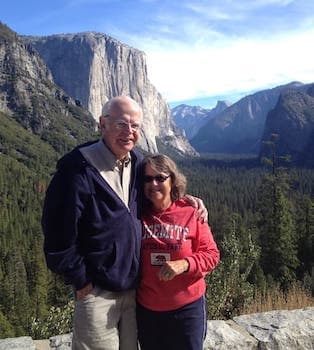
Curated with aloha by
Ted Mooney, P.E. RET
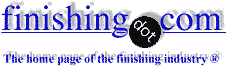
The authoritative public forum
for Metal Finishing 1989-2025
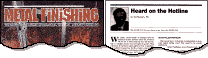
-----
Mastercylinder seal wear
2002
I am using a hardcoated piston and cartridge for a dynamic brake master cylinder application. The hardcoat solved a problem of piston/bore wear.
However, the coating in the bore seams to vary from batch to batch and part to part (.0006 -.0008 is the target). Also, the hardcoat thickness will vary from the bore opening to the bore bottom. The problem has to do with rubber seal wear. One set of parts will operate for over one million cycles and the next will wear out the rubber seals in less than one hundred thousand cycles. There seams to be subtle, almost imperceptable differences in the surface finish, based on hardcoat thickness build up. But those minute differences have a huge effect on rubber seal life.
My questions are:
1. Is a dynamic hydraulic application suited to hardcoated surfaces? Has anyone used this combination before?
2. What type of instrument should I use to measure surface finish (Ra does not tell me what I need to know)?
3. How controllable is the hardcoat process? Am I asking too much from this process?
4. Is there a better coating alternative?
- Menomonee Falls, Wisconsin, USA
2002
I will only address your Number 3 question. Hard Coat is controllable. It sounds like your applicator is not accurately calculating the surface area in order to apply a uniform number of amperes (24 to 36 amps per square foot).
OR if he does have the current correct then perhaps he is not getting enough agitation down on the inside so that the stagnant solution is not getting a fair share of the apparent current density.
Perhaps some of the parts are positioned to get good agitation and others on the same rack are realtively stagnant.
This is a very common problem with job shop anodizers. Different current density yields different thickness in the same time. Lack of UNIFORM agitation interprets as different current density on the inside depth from the "apparent" current density on the total part.
You did not state the inside diameter and depth that he has to "throw" into. Maybe he needs an inside cathode. Maybe he needs higher acid content, or lower temperature, or less overall tank side cathode (should be ±=1/3)
Get us some more data and let's eet again. When you come back let us know the alloy. ALso let us know aboutthe thickness - do you mean on the diameter or"on the side". Machine shop folks talk about "on the diameter", most anodizers and platers talk about "thickness on the side".
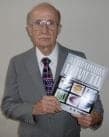
Robert H Probert
Robert H Probert Technical Services

Garner, North Carolina
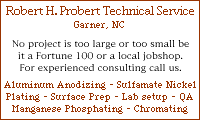
Q, A, or Comment on THIS thread -or- Start a NEW Thread