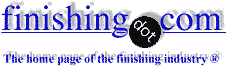
-----
Kettle erosion problem
A good friend of mine has a small galvanizing business and is having problems with his kettle, which local people in the industry are unable to solve. Unfortunately he does not have email access, so has asked me to post a question. I don't have all of the details, but he has a gas fired kettle made from local steel which is apparently "certified" for use in hot dip galvanizing kettles. The problem is that the steel is being "eaten" away rapidly (he has taken the kettle out once already for replacement of the affected plates, but the problem is recurring). The erosion is very uniform, almost in layers (although every now and then there is a small "island" of unaffected material, generally about an inch in diameter), and seems to be related to the composition/batch of the steel plate used to make the kettle. Not all of the plates in the tank are affected, but those that are seem to be uniformly affected over their area. The erosion also does not seem to be concentrated in the! area of the gas burners. The material has been analyzed, and its composition seems to be in the correct range for compatibility with kettle requirements.
Anybody have any ideas, or perhaps pointers to another forum or organization?
Thanks,
Mark Marshall- Cape Town, South Africa
2002
First of two simultaneous responses -- 2002
Mark,
I am not an expert in kettles but I guess if your friend is using fluxes or different types of steel parts it may be they are droping to the bottom and causing a drag of flux or bimetal galvanic sites for this corrosion. Or simply the steel uniformity is not good enough due to poor melting and rolling processind during its production. It has to be low carbon and low silicon as well.
Bye,
Guillermo MarrufoMonterrey, NL, Mexico
Second of two simultaneous responses --
Mark, there are necessary some additional information for answering your question. There can be a lot of influences - can you write me what is temperature of zinc bath, which elements are added to zinc bath, quantity of these elements, how long is lifetime of tank. Used pretreatment, composition of material of tank and type of galvanized goods would be also useful for solving this problem.
Best Regards,
Jiri Vana- Frydek-Mistek, Czech Republic
2002
Q, A, or Comment on THIS thread -or- Start a NEW Thread