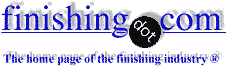
-----
Zinc plating vs. hot dip galvanizing

I would like to know the difference between hot dip galvanizing and zinc plating in relation to pole line hardware used in the construction of overhead electrical distribution power lines. ie. machine bolts, lag screws, etc.
What is the difference in the two methods and the life in the atmosphere.
Gerry Geall- Winnipeg, manitoba, Canada
1998
aZinc is a sacrificial coating that does its job by slowly corroding; the life of the coating is essentially directly proportional to its thickness.
There are three common ways to apply zinc: electroplating, mechanical plating, and hot-dip galvanizing. Where bright, smooth and shiny appearance is an issue, electroplating is the only choice. In a case like yours, where appearance isn't an issue, the operative phrase is "zinc is zinc"--there is no real corrosion-resistance advantage to any of the three methods.
The thing is, electroplating is usually the least expensive option for thin coatings, mechanical plating the least costly for mid-range thicknesses, and galvanizing the least costly for heavy coatings.
When you need thick coatings for extended life in tough situations, hot dip galvanizing is the usual way to go.
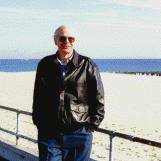
Ted Mooney, P.E.
Striving to live Aloha
finishing.com - Pine Beach, New Jersey
1998
A. Gerry,
You only have two choices if you are following any spec. I worked on a Manitoba Hydro spec about 4 years ago. I recommended mechanical zinc over hot dip. Same holds true for other projects I worked on for Quebec Hydro and Ontario Hydro.
Ray Delorey- Cambridge, Ontario, Canada
1998
What is the most cost effective but durable coating for pole line hardware conducive for tropical countries, where there is no temp dip (winter). Generally, atmosphere is humid, high salt content, weather ranges from 12 - 35 °C.
Joseph NavarroQuezon City, Philippines
1998
The responses you see near the top of this letter should hold true for your situation. For something that receives rough handling and minimal maintenance, you really need a sacrificial coating of metal because organic coatings will not deliver adequate protection once scratched. Cadmium is too toxic to be recommended anymore for straight corrosion protection. So, it's a question of applying metallic zinc, and that can be done by mechanical plating or hot dip galvanizing. It doesn't much matter which method you use, but you'll probably find that mechanical plating will be more economical up to a certain thickness, after which galvanizing will become more practical.
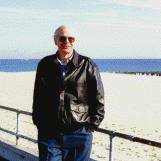
Ted Mooney, P.E.
Striving to live Aloha
finishing.com - Pine Beach, New Jersey
1998
1999
It is possible to use Alkaline Zinc/Nickel plating on the type of high power electric transmission equipment that you mentioned. A thickness of 0.0005 inch with an iridescent chromate conversion coating can give in excess of 5000 hours in the ASTM B117 Salt Fog test. The iridescent chromate has a readily identifiable vivid coloration.
I do not have figure available comparing this finish to Galvanize (hot or mechanical), so you will have to help me out on that part of your question. If you are now using galvanize, you will know how long the finish can be expected to last.
Certainly, I can supply other information if you are interested in learning about this technology. Hope this has been helpful in answering your question.
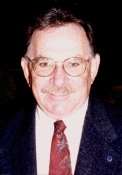

Ed Budman [dec]
- Pennsylvania
With deep sadness we advise that our good friend Ed passed away Nov. 24, 2018
I am trying to source a practical method to preparation and zinc-coating anchor chains used on marine vessels.
GREG STONE1999
Welded chain has to be coated after assembly. There are basically two ways this can be done: the really big chain manufacturers use continuous plating methods, like a coil coater would. Smaller manufacturers hang the chain on racks, and rack plate it, usually periodically jiggling it. I have seen people TRY to barrel plate chain of this sort, but I haven't seen anybody accomplish it with enough success to put the rack platers out of business
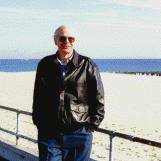
Ted Mooney, P.E.
Striving to live Aloha
finishing.com - Pine Beach, New Jersey
1999
I have personally seen all three processes done, and worked personally on a Barrel Plater line, and a Hot Dip Galvanizing line. Chain looks great coming out of a Barrel plater line, although only short lengths of chain can be plated in this way. If the chain is too long, the chain tangles up, and there is no movement while plating causing a poor appearance, and a very thin plating. For something like nuts and bolts, Electroplating is the way to go. I used to plate bolts at a former job, for a very large nut and bolt company, and they needed to either use undersized threads, or oversized nuts because the zinc was too thick (this is hot dip galvanizing method) but that was definitely the way to go for thickness, and longevity. I could also get it to look quite nice compared to mechanical plating. (Be warned that hot dip galvanizing is an expensive process, and a dangerous one as well)
Bottom line is, if you want it to look good (no matter who is doing the work) electroplate it. It won't last as long as Hot dip Galvanizing, but it will give a better appearance to the customer. If you have an experienced Hot Dip Galvanizer, go with that route, someone with experience can get the right tin, and aluminum levels in the zinc for a great appearance, but someone with little experience won't know what to look for in appearance to tell them the correct levels. Also, thickness in hot dip galvanizing is dependent on how long the metal is in the zinc, the temperature of the zinc, and the grade of steel being plated.
Also bear in mind the if the steel being plated needs to be heat treated to a certain RC, then it can not be Hot Dip Galvanized, as this will change the RC of the material.
Neil Kamrowski- Winona, Minnesota, USA
2002
Another thing to consider is the material your using.
Zinc Dichromate can have a bad effect on some grades of steels. The process allows hydrogen to accumulate in the steel causing hydrogen embrittlement which mimics a high quenched carbon steel (brittle). This can be reduced or eliminated by baking the parts after coating. Make sure you look into this when choosing your method.
- Winnipeg, Manitoba, Canada
2005
Checking if article was actually hot dipped
Q. To anyone --
I'm not an engineer but I was sometimes assigned to check the quality of output of our finished products in sign making. We have this billboard project and our client requires us to do some hot dip on their structure. We don't have in-house facilities to provide such requirement and we searched for some suppliers to do it.
We found one with cheaper price, but when an engineer of our client visited us he said that the result of job done by our supplier is not really hot dip. My question is "How can we know if the steel really passed through the hot dip process". "What is the quality of hot dip"?
I appreciate any response coming from your end. Thank you very much.
Makati City Philippines
2006
For a company to do hot dip galvanizing they must have a kettle full of molten zinc (at about 840 °F) big enough to dip the product fully into the molten zinc. If you visit your hot dip galvanizing supplier, you will see the zinc kettle. Sometimes electro plated zinc is called "galvanized" (but is not hot dip galvanized).
After the product is hot dip galvanized it will have a zinc coating about 3 mils to about 10 mils thick. For electro plated zinc the coating is usually only a few tenths of a mill thick (e.g. 10 to 100 times thinner zinc). Electro "galvanized" steel is suitable for indoor use (but not outdoor use), whereas hot dipped galvanized steel is suitable for most any use indoor or outdoor. The thicker the zinc coating the longer the lifetime of the product.
You can use a "banana" magnetic thickness gage to non-destructively determine the zinc thickness of the coating.
One mil equals 25.4 microns. A mil is 1/1,000 of an inch. A micron is 1/1,000,000 of a meter. Hot dipped galvanized steel can sometimes show "runs" or "drips" at the last part of the product to be withdrawn from the molten zinc. Electroplated is more uniform with no "runs" or "drips."
Regards,
2006
What micron thickness of zinc plating will withstand the Antirust test (salt fume test) as per ISO 0072/any relevant standards.
Bharat Singh GarsaExport company - Noida, Uttar Pradesh, INDIA
2006
Could you please explain the advantages, either to apply hot-dipped galvanising or electro plating process for the nuts bolts, for the external use in the middle each, with extremely corrosive atmosphere.
Vrajesh AstiProjects- Power Transmission - Abu Dhabi, U.A.E.
August 22, 2008
Hi, Vrajesh. The short answer is that galvanizing is usually about 5-10 times as thick as zinc electroplating and therefore about five to ten times as corrosion resistant. Very similar questions are asked here every week, and the people who have responded a dozen times already have wearied of it and probably won't answer again :-)
So please patiently use the search engine to see what they have written. Good luck.
Regards,
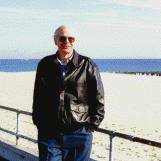
Ted Mooney, P.E.
Striving to live Aloha
finishing.com - Pine Beach, New Jersey
August 22, 2008
Multiple threads merged: please forgive chronology errors and repetition 🙂
How to identify Zinc plated and hot dip galvanising. Any difference in Inspection certificates? What is the major difference?
Anoop Venugopal- UAE
January 12, 2009
Is there a way to determine whether a partially corroded, zinc coated fastening was originally protected using the plating or hot dipped process? For example, can one examine the bond between the zinc and the substrate to determine how the coating was applied?
Peter CastleHobbyist, homeowner - Stonington, Connecticut, USA
June 21, 2011
Hi, Anoop; hi, Peter. As you are seeing, we find that the readers are wary of possibly being drawn into contract disputes, so they generally won't answer questions that are cast in the abstract. To improve the response, you might describe your situation. Thanks, and good luck.
Regards,
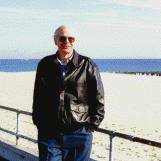
Ted Mooney, P.E.
Striving to live Aloha
finishing.com - Pine Beach, New Jersey
June 22, 2011
Multiple threads merged: please forgive chronology errors and repetition 🙂
Are the parts really Hot Dipped Galvanized as spec'd?
Q. We use some items that must be Hot Dip Galvanized per ISO 1461 TZNO. These are brackets made from 5/16" up to 1-3/4" plate. We have recently been receiving some brackets from a new supplier, and based on visual inspection, may not meet the specs. When handling these items a bright silver film easily transfers to your hands and the surface is very smooth. What type of test can be performed to determine if this coating system is actually hot dip galvanized?
Guy SeymourManufacturing - Greer, South Carolina, USA
February 16, 2012
A. No galvanizing should come off in your hand as a silver film.
This sounds like a case of using silver paint. Perhaps they were galvanized but there were bare patches (usually as a result of poor pretreatment before dipping in zinc). ISO1461 allows for the "repair" of very small areas of bare steel with zinc rich paint.
But the thickness of that paint repair should be more than the thickness of the galvanizing, and should not exceed a size limit thats about the size of a medium size coin.
One test you could do yourself to check this is to try rubbing with a solvent like say thinners. A galvanized surface will not be affected at all, but paint will start to come off. If you get silver on the cloth, its likely paint. If the area of the paint is more than say 1" square, then ask the galvanizer what standard he uses.!
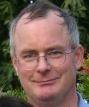
Geoff Crowley
Crithwood Ltd.
Westfield, Scotland, UK
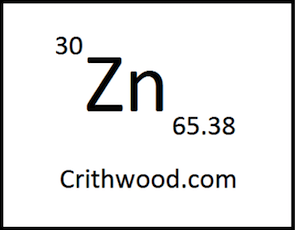
February 18, 2012
Sir, what kind of protection is required for hot dip galvanised conduit, and which test is required for corrosion testing?
Arslan Cheema- Pakistan
August 17, 2012
Q, A, or Comment on THIS thread -or- Start a NEW Thread