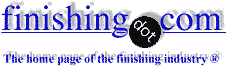
-----
Monitoring anodizing parameters
1998
I am working with a plating shop to standardize their anodizing parameters. We are hoping to set up a system to monitor temperature, amps and voltage. This data will be stored electronically so it can be called up when we repeat the same product at a later time.
We also want a monitor available so the operator can see if the tank is maintaining the setpoints.
Is there anyone that is doing this now that would be willing to discuss their system?
Thanks for you help.
Dave SlavenskyRoseville, California
I set up a sytem like you describe about 8 years ago for an anodizing/paint shop. When researched, it turns out that there are quite a few people out there which have products and services to do what you want. We were on a tight budget and already had several controllers. We went with Partlow MIC 2000 and 6000 controllers with RS-232 data output boards added, daisy-chained and run into an old pc. Partlow had an association with a sister company which had fairly inexpensive software, which worked in conjunction with their controllers. They also helped a lot with free phone advice with the set-up. We were able to add a proportioning controlled gas fired paint oven to the system.We were able to combine other individual controllers with two and three input/outputs with the data aquisition software. This included output from the waste pre-treatment system pH meter. The software was configured to customize the screen display and we printed out bake charts, anodize line parameters and waste pre-tx system info. There were alarms which allowed us to see when parameters were out of their limits. At that time the controllers were about $750.00 each, the software was under 2 grand. There were all sorts of ancillary costs such as thermocouples, wires, etc. We already had most of that including an old pc. We never configured the system for control, only aquisition, although it had that capability. We set the controllers out on the line and set a dip switch inside so that the control parameters could not be changed easily.We did not have the electrical parameters for the anodizing process set-up as that was controlled manually by a variable potentiometer, there was not a control circuit in our rectifiers at the time that made that easy.With a modern control circuit configured with 5-20 milli-amp capability that would not have been a problem to add.I have seen several other systems with automatic lines, etc. However, this one was fairly inexpensive and easy to build.Hope this gave you some ideas!
Ward Barcafer, CEFaerospace - Wichita, Kansas
1998
Q, A, or Comment on THIS thread -or- Start a NEW Thread