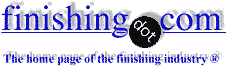
-----
Aqueous degreasers vs. vapor degreasers
Q. I would like to invite opinions of those who have used aqueous degreasers on small parts, threaded and/or with holes, in volume and have compared with vapor degreasers. Should I look for an OSHA acceptable vapor degreaser or are there equal-performance alternatives for plating? Any opinion about the types of equipment?
Mandar Sunthankar- Fort Collins, Colorado
1998
A. In my opinion, the best system ever devised for cleaning oil, grease or wax from metal parts is the two chamber vapor degreaser, particularly if the clean sump is fitted with good ultrasonics.
There are a few environmentally "friendlier" solvents available to replace the 1,1,1-trichloroethane (TCA) that everybody thought was so wonderful a few years ago. TCA can no longer be legally manufactured in most of the world thanks to the Montreal protocol and the price of recycled stuff is going out of sight, if you can find it. The "new" solvents start at about $2400 per 55 gallon drum and must still be used in the new EPA-regulated degreasers that start at about $20,000. N-propyl bromide (NPB) is probably one of the better "drop-in replacement" solvents, and I think it sells under at least three different names already.
If you want to deal with outrageous regulations, perc, TCE, and methylene chloride are cheaper. I doubt that they are worth it. All you have to do to understand why is TRY to read and understand the regulations covering them.
On the other side of the issue, a lot of work has been done on aqueous systems. The good side for them is that the regulators seem to prefer them. They don't do as well on oil, grease, and wax, but it's a lot cheaper to buy and operate them. And if you are going into a plating operation immediately afterward, you don't need to worry about drying the parts until after the plating is done.
I know there are proponents of semi-aqueous and other in-between systems, as well as solvents like alcohols, petroleum solvents, MEK / methyl ethyl ketone and acetone ⇦ on eBay or Amazon [affil links] Warning! Flammable! , and the citrus and pine stuff. If you can find one that fits your specific case great. However, I don't think anyone can beat our newly refitted EPA-legal Baron-Blakeslee with the proprietary blend based on NPB for the wax that is our main problem.
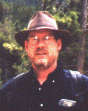
Bill Vins
microwave & cable assemblies - Mesa (what a place-a), Arizona
1998
Thanks, Bill.
I agree, Bill, and would add a couple of comments myself.
First, there are some piece-parts which are bimetallic and can be cleaned just fine via solvent degreasing, but which can easily be weakened or destroyed if put into an aqueous cleaning bath. Second, there are parts with high chrome content, or high zinc content (brasses), or high percentages of other amphoteric metals, that can be easily weakened by aqueous cleaning. I have seen aerospace parts processed in down & dirty jobshops by $7/hour laborers . . . and I find it terrifying that nobody vocalizes any concern about the implications involved in telling these laborers to stop processing the parts in solvent solutions (which can't damage the parts) and to start processing them in aqueous solutions (which will damage them if the process is not done precisely right). Does nobody else see the danger, or are they sworn to silence?
For decades, hollow parts like turbine blades have been safely and ecologically processed by filling them with wax, then performing the plating process, then stripping the wax away with solvent, and finally separating the wax and solvent for re-use. Aqueous processing of such parts is an ecological improvement? That's ridiculous.
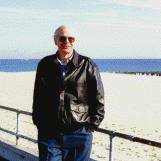
Ted Mooney, P.E.
Striving to live Aloha
finishing.com - Pine Beach, New Jersey
Q. Ted and Bill, I appreciate your feedback. There is another solvent I tried recently and that also worked well, that is Stoddard solvent. It is available as paint thinner in hardware stores. I tried it because I used to use it on a production line 20 years ago. Since then I have not heard much about it. Anyone knows about its use?
Mandar Sunthankar- Fort Collins, Colorado
1998
A. Mandar, I recently received an automation inquiry from someone planning to use Stoddard Solvent. As I understood it, Stoddard Solvent is the same as, or similar to, "subterps". We have become so accustomed in recent years to using non-flammable materials that it is easy to forget that some solvents are flammable. I don't know the flash point of Stoddard, how flammable it is, but it is something you need to remember to check, because it is one thing to dampen a cloth with a quarter ounce of a flammable material, and quite another thing to put a thousand gallons of it in an open-top processing tank.
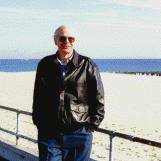
Ted Mooney, P.E.
Striving to live Aloha
finishing.com - Pine Beach, New Jersey
Q. Ted, the stoddard solvent (other names: mineral spirit, petroleum solvent, naptha distilled solvent) is a VOC with a flash point of 100 °F and boiling point of 325-384 °F. Like acetone, it contains benzene product, and is less flammable but a bigger health hazard than acetone. It does stink though, so needs good ventilation. It is cheap, but the real problem in production is, at room temp it does not dry for hours. So the overall benefits are questionable.
Mandar Sunthankar- Fort Collins, Colorado
1998
Thanks for the data and the practical problem about drying as well, Mandar.
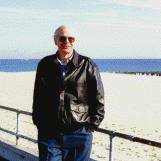
Ted Mooney, P.E.
Striving to live Aloha
finishing.com - Pine Beach, New Jersey
![]() |
A. You can purchase 143° flash point Stoddard Tracy Cheatham1998 Q. Tracy, do you have any info about its availability, handling and use? Mandar Sunthankar- Fort Collins, Colorado 1998 A. 143 solvent is one of the solvents sold by various chemical distributors. These are commonly known as aliphatic napthas. 140 Solvent is another drop in. The number is derived from its flash point, 140 °F being the point below which a flammable sticker comes on the drum. J.M. Chunn1998 |
Q. Mr. Mooney:
I read with interest your statement in the June-- issue of Metal Finishing, that aqueous degreasers can weaken or destroy high zinc (brass) parts. I had not heard this before and was wondering if you could provide details. I have seen a lot of literature specifying alkaline soaks or electrocleaners for prepping brass for plating and am wondering if I am missing something. At the moment we are ultrasonic-cleaning brass in "Blue Gold" followed by electrocleaning in Oakite 90 [Chemetall] and haven't seen negative effects.
Joel Mitchell1998
A. Joel:
It is certainly not the case that caustic cleaning or electrocleaning always destroys brass parts :-)
Rather, that vapor degreasing will not hurt brass, whereas brass is vulnerable to damage from aqueous solutions if things aren't done right.
One case I remember was nickel-chrome plated brass parts for writing pens. The engineers felt that they were overcleaning the parts, so they instructed the operators to remove most of the anodes from the electrocleaning tank. However, the tank in question used submerged anode rods; so the result of removing the anodes was to expose the one band of parts that corresponded with the elevation of the anode rod to severe etching and dezincification. You could inspect 98 percent of the parts and see no problem whatever, but the 2 percent that aligned with the anode rod were in serious trouble. This was just a cosmetic issue when dealing with writing pens, but is the kind of thing that frightens me for automotive or aerospace parts. When we ideologically convert from solvent cleaning to aqueous cleaning, but find it inconvenient to talk about the possibility of adverse consequences, dismissing anyone who urges caution as a reactionary, we can position ourselves for trouble.
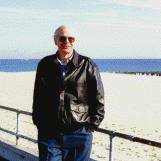
Ted Mooney, P.E.
Striving to live Aloha
finishing.com - Pine Beach, New Jersey
Q, A, or Comment on THIS thread -or- Start a NEW Thread