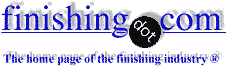
-----
Bend test for plating hardware
1998
I need a clarification of the FED QQ-C-320 bend test. We use coupons for process testing prior to plating hardware. The specification reads "The article or specimen may be clamped in a vise and the projecting portion bent back and forth until rupture occurs. If the edge of the ruptured plating can be peeled back or if separation between the plating and the basis metal can be seen at the point of rupture when examined at four diameters magnification, adhesion is not satisfactory." Our problem is with the phrase "Edge of the ruptured plating." When the chrome comes off approximately 0.200 inches back from the break in the coupon during the bending, yet won't peel back any further using a Exacto knife ⇦ on eBay or Amazon [affil links] . Is this considered a failure? Or does the coating need to break right at the point of the break in the coupon and no further? We interpret the adhesion criteria as the latter. What do you think?
Garry Pickettaerospace - Los Angeles, California
Garry, I think that a bend test is a poor test for chromium. It is by design a very hard and brittle material. The bend test is severely influenced by to operator and by the exact equipment and procedures that he uses. A wide radius bend is going to fail much differently than a narrow one. Going less than 90 degrees each way affects the break also. The parent metal affects it.
A cut or grind thru would seem like a fairer test for adhesion.
The way you stated it, I would call it a failure since it delaminated before the parent metal broke, rather than breaking at the metal point of failure.
James Watts- Navarre, Florida
1998
Mr. Pickett,
Your description of the coupon indicates an adhesion failure. My experience with the Defense Contract Administration Service (DCAS) is that they would also consider your situation an adhesion failure.
Rick PainterCleveland, Ohio
1998
I would also vote for calling it a peeler.
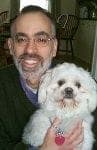

Tom Pullizzi
Falls Township, Pennsylvania
1998
Although I do not recall the theoretical reason for the phenomenon in discussion here, the stresses between the film vs. the substrate can cause peeling if the radius of the bend is less that 4X the thickness of the substrate, and if an alloy is not formed at the interface. So first check if you are using thicker substrate than the common practice. Decrease the substrate thickness and you may find that peeling does not occur. However, this may not be an appropriate way to qualify your product.
The best way to quantitatively determine the adhesion is to use the pull-tester as described in ASTM D4541. I do not think it is a common practice in electroplating shops but I recommend using this test. I have been using one unit made by Elcometer, Rochester Hills, MI. It will reveal wonders!
Mandar Sunthankar- Fort Collins, Colorado
1998
Q, A, or Comment on THIS thread -or- Start a NEW Thread