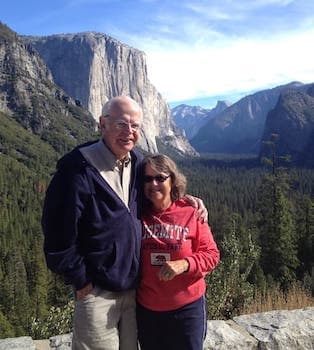
Curated with aloha by
Ted Mooney, P.E. RET
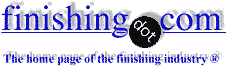
The authoritative public forum
for Metal Finishing 1989-2025
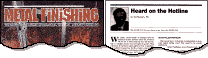
-----
3 Sigma certification for selective plating
We have a customer that is asking for 3 Sigma Certification for a selective plated job. The part is a ceramic piece with about a dozen isolated areas. They are being plated with electrolytic gold over nickel on a copper substrate. Is a Cpk value of 1.33 something that is common in the plating industry now? We haven't had to plate to as strict a tolerance as this for gold before with any of our other customers, especially with a dozen selective areas on each part. It has definitely made a difference in pricing for what they originally wanted (a minimum of 100 microinches). Of course, we were shooting for as close to the 100 microinches as possible but had some problems developing a rack to keep everything consistent on a multi-piece rack. Just wanted to know if other platers were dealing with the 3 Sigma or 6 Sigma certification on selectively plated parts.
Thank you,
- Erie, Pennsylvania
2002
First of two simultaneous responses --
Hello fellow tank jockeys:
Most "regular" plating tanks, big open vessel with anodes hanging over the sides and a DC rectifier plate out ± 50% of mean within
± 3 sigma either side of mean. This is why a standard nickel callout is 100-400 microinches, because they know that at about 240 microinches targeted mean, 99.99+% of readings will be within 50% of
240, well within the callout and CpK targets. The problem comes when product engineers don't investigate the failure mechanisms with thick or thin deposits, and set an unnecessary bandwidth. Now say the callout above is 200-300 microinches. The part still functions as before, but but this run now has a low CpK entirely due to the callout limits. The engineers doing the callout never did a "FMEA" on thick or thin deposits to determine spec limits, and just unwittingly set them tight. Your marketing should always be aware of your process capability so that they don't agree to impossibilities. In bondable electronics, 6 sigma is preferred and often required due to the sensitivity of wirebond and solderball processes to things like Gold & Nickel thicknesses. But this entire concept lies at the confluence of three engineering concepts. First, in electronics, the processor wants to process as large an area as possible per run for higher thruput, so he works to drive uniformity over larger and larger areas. Second, the product designer must design parts that will plate uniformly, in electronics, this means don't have both densely & sparsely populated areas on the board, and a multitude of vastly different sized plateable areas. And third, the metallization engineer on the product side must thoroughly understand what failure mechanisms the deposits suffer at both the thick and the thin end of the thickness callout. Now all three of these people get together to come up with an acceptable callout and product design as it goes into plating. You make 6 sigma every time.
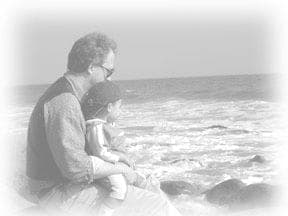
Dave Kinghorn
Chemical Engineer
SUNNYvale, California
2002
Second of two simultaneous responses -- 2002
Dear Dave,
I used to work for a QS 9000 company in Toronto. My customers always required Xbar charts with Cpk values more than 1.33 while submitting PPAPs. So the answer is, a Cpk value more than 1.33 is attainable if you really maintain your process baths. You might end up in daily additions to your baths instead of weekly additions. So process is fine.
But if your customer is talking about Cpk for rejections then certainly it is tough. In my 10 years in plating my experience tells me that the average for rejections in plating shop is at the least
3%.
Any other thoughts on this ?
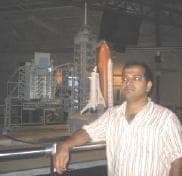
Hemant Kumar
- Florida, USA
2002
Dave,
There are 2 items that might require 3 sigma certification. One is the thickness of the nickel and gold and the other is the location of the selectively plated areas. The location is usually well controlled by using photo resist and some kind of marks on the substrate to align the photo tool to the substrate. Typically this is not a problem.
The plating thickness can be controlled by carefully designing the plating cell and type of rectification. As a start, I recommend using a separate rectifier or channel of a rectifier for each part. If both sides of the part have to be plated and the amount of surface area is varying from one side to another, you should consider using a separate rectifier for each side of the part. This will insure the same weight of metal on each part but not how that weight is distributed among the selective areas.
Getting thickness uniformity within each part is more difficult. As a minimum, I would suggest using shields to prevent areas near the edges of the part from being too thick. The gold thickness will typically follow the nickel thickness. For the nickel, I would use pulse reverse plating on the nickel to even out the thickness from one are to another. If the nickel is well controlled then the gold will also be well controlled.
Another item to consider is the thickness of the resist. For the most accurate control you want the sum of the nickel and gold thickness to be less than the resist height. All of the plating should be within the walls of the resist. If the plating extends over the resist it is hard to control the current density unless you have a programable rectifier. Using individual rectifiers, PR and shields should give you 5 to 10 percent thickness variation within a part and a 5 percent or less variation from part to part.
Good luck
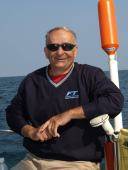
Pat Mentone
St Paul, Minnesota
Q, A, or Comment on THIS thread -or- Start a NEW Thread