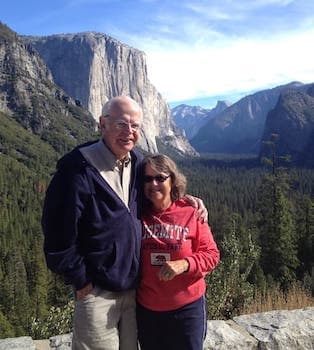
Curated with aloha by
Ted Mooney, P.E. RET
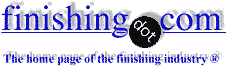
The authoritative public forum
for Metal Finishing 1989-2025
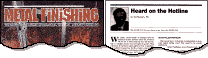
Thread 159/09
Plastisol & Solvent Ink Formulas & Improvements
DOP = Dioctyl Phthalate
Q. Which grade of PVC resin is dissolved in DOP? How can I dissolve PVC in DOP? What is the method to dissolve? Can anyone tell me the process?
Anik Hasan- Dhaka, Bangladesh
July 6, 2023
publicly reply to Anik Hasan
Some of pvc resin dissolve in solvent like methyl ethyl ketone etc. You have to check technical data sheet of pvc resin manufacture. After that you can go for plastisizer.
You have to use solvent for PVC. Check the TDS details. Everything is showing in data sheet.
Alfat sheikh- Bhavnagar [Gujarat, India]
February 4, 2024
publicly reply to Alfat sheikh
Q. Hi, I am trying to develop plastisol ink for textile screen printing. I faced problems that dry ink. What can I do for for always wet my plastisol ink except dryer not in frame?
Alfat sheikh [returning]- Bhavnagar [Gujarat, India]
January 25, 2024
publicly reply to Alfat sheikh
This meeting place welcomes Q&As, photos, history, & interesting tidbits π
Please engage with other posters
β’ When people show interest in each other's situations, the forum quickly becomes a fun & informative learning experience for everyone !
β’ But if posters show little interest in other people's situations, it can deteriorate into a string of unanswered questions

Q. We are making PVC handles on pliers by dipping into the plastisol. We have a problem our handles are sticky and the pliers don't get into the poly bags easily. We are seeking help to solve this problem. Our question is what chemical can we add that makes the handles non-sticky. It should be phthalates free. We will appreciate if some experts or chemical engineers can help us in this regard.
Muhammad Aslam- Sialkot, Pakistan
September 14, 2023
publicly reply to Muhammad Aslam
Q. Hello finishing members, I am trying to make plastisol ink. There is a problem with vinyl acetate monomer (VAM). Is it necessary to add VAM in plastisol ink? First I used copolymer and plasticizer then added vinyl acetate monomer for coating. When I added it in canister our material is being very hard..
Alfat sheikh- Bhavnagar, India
October 9, 2023
publicly reply to Alfat sheikh
β© Related postings, oldest first β©
Q. We are trying to use titanium dioxide
β¦ this on
eBay or
Amazon [affil links]
for our plastisol (PVC). I have no idea how much weight of titanium dioxide we should add into the plastisol.
* What is the general dose for TiO2 in plastisol?
* Can TiO2 acts as filler (CaCO3)?
* Can we reduce the and replace the weight by using TiO2?
* Our product should be dark brown in colour.
Another question:
UVA can mean UltraViolet light in the "A" range, 320nm to 395nm wavelength.
UVA can also mean Ultraviolet Light Absorber (an additive for inks, paints, & plastics)
* We are now using UVA in our plastisol. Now, we are trying not to use it anymore. Will it affect or how much will it affect our product?
* Is UVA just for the stability of colour?
Additional information:
* Last time our product has sticky problem just a few weeks after the production. The sticky problem is especially serious for the product strongly exposed under sun.
* We changed our formula totally and temporary satisfaction of products achieved.
* I started to join in the plastisol production just during the changing of new formula. I don't really know how the mixing of plastisol did last time with the bad result. After all, We don't want the problem to occur again nor any other new problems.
The production is running everyday. New formula needs to be ready as soon as possible for the production. Hope someone here can help us in this matter. Thank you very much!
- PJ, Selangor, Malaysia
2002
publicly reply to Susan Low
A. Why don't you try PCC as it provides the time-stable rheology required and has the ability to remove HCl formed by any partial decomposition.
Formulation : PVC 25%, Plasticiser 36%, PCC 20% and GCC 12%, others (Adhesion promoter, ZnO, CaO, hydrocarbon oil) 7%.
- Malaysia
August 8, 2008
publicly reply to KL Chong
A. Question 1: To get high opacity you need to keep TiO2 in your formulation approx. 34%. But because of price you need to optimise your formulation with replacing some part of TiO2 with CO3Ca (like 10%).
Question 2: Formulation always need good balance between plasticizer and resin and pigment. Less plasticizer gives you sticky products but more plasticizer gives very soft and no sticky effect but problem is bleeding. try the best balance between them (33% plasticizers, 30% resins and 35% pigment and filler. do not forget makes a good dispersing of your pigment and filler with adding some dispersing agent. final product if you can pass through the three mils results should be better.
Regards
- Montreal, Canada
August 18, 2008
publicly reply to Farid Motamedian
I work in the field of production of plant insulation and adhesives. The information in this forum is very helpful and practical.
Production and trade - maker
April 2, 2022
publicly reply to mohammad shikhy
A. TiO2 is a pigment/UV protector/filler in plastics industries, which type of your end product, you can use TiO2. If products are film grade may create haziness/opacity in film by TiO2 depending by your formulation; in leather application use of TiO2 6-8 in your formulation
Ashish Patelcoaters - Valsad, Gujarat, India
January 25, 2012
publicly reply to Ashish Patel
Tip: Readers want to learn from Your Situation π
(little can be learned from abstract questions, so many readers skip them)
Q. How to eliminate air bubbles in plastisol? Can I get formulation of plastisol coating?
Sunartomarketing - bogor, west java, indonesia
February 19, 2012
publicly reply to Sunarto
A. Sir, air bubbles are created in leather; many factors like (1) humidity- your ingredient of plastisol are absorbing moisture in environment, so check your raw material at stores as well as mixing area for storage of plastisol. (2) if your raw material are not absorbing moisture, check it spread coating of top coat & foam coat; if air bubbles are created, check your plastisol viscosity. If it is thick reduce viscosity of plastisol by viscosity reducer and then observe; after using thin plastisol you can see your air bubbles are reduced at your top & foam coat. This above problem is avoided continually by practice.
Ashish Patel, (Q.A.In charge)- Valsad, Gujarat, India
publicly reply to Ashish Patel
Tip: Readers want to learn from Your Situation π
(little can be learned from abstract questions, so many readers skip them)
Q. What is the evaporation percentage in heat of DOP, DINP and other chemicals in PVC synthetic leather making?
Ashish bhavsaremployee - valsad,gujarat, India
February 25, 2012
publicly reply to Ashish bhavsar
Tip: Readers want to learn from Your Situation π
(little can be learned from abstract questions, so many readers skip them)
Q. What is the meaning of PCC and GCC?
Thanks.
- Bogor, West Java, Indonesia
March 27, 2012
publicly reply to Sunarto
A. Hi Sunarto.
PCC is precipitated calcium carbonate.
GCC is ground calcium carbonate. Good luck.
Regards,
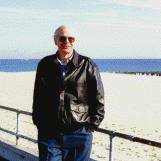
Ted Mooney, P.E.
Striving to live Aloha
finishing.com - Pine Beach, New Jersey
publicly reply to Ted Mooney
Q. Well, can someone tell me which is the best phthalate plasticizer for making low bleeding white, or formulation for making low bleed white?
Can we add any additive to make lb white?
How to make HD BASE?
- Jal, Punjab, India
April 23, 2012
publicly reply to Sumit Aggarwal
Tip: Readers want to learn from Your Situation π
(little can be learned from abstract questions, so many readers skip them)
Q. What is the process of PVC plastisol ink and material used with grades.
Malik Ahmad- Lahore Pakistan
September 20, 2012
publicly reply to Malik Ahmad
Tip: Readers want to learn from Your Situation π
(little can be learned from abstract questions, so many readers skip them)
Q. I wanted to know the Plastisol formulation for making car mat.
Akash Sharma- Delhi, India
March 6, 2013
publicly reply to Akash Sharma
This meeting place welcomes Q&As, photos, history, & interesting tidbits π
Please engage with other posters
β’ When people show interest in each other's situations, the forum quickly becomes a fun & informative learning experience for everyone !
β’ But if posters show little interest in other people's situations, it can deteriorate into a string of unanswered questions

Q. Dear Sirs,
Could you please give us some idea what chemical should we use for getting anti-slip or grip effect in plastisol Ink? The finished product is cotton knitted glove. It has dotted print. The dotted print needs anti slip or grip effect.
Waiting for your advice.
Thanks & regards,
Vishy
- Tirupur, Tamil Nadu, India
December 12, 2013
publicly reply to Vishy Nathan
Q. Dear Sir,
I am into screen process printing ink production, Namely water-base textile printing ink, PVC solvent ink for pvc sticker printing, ss polyscreen for polyethylene treated sheets, etc. But recently I added plastisol to our range. The question is what is the function of soy lecithin in plastisol production.
screen process printing ink production - Lagos Nigeria
June 9, 2015
publicly reply to Vincent Chinweze
A. Hi Vincent. I know nothing of plastisol formulation to be able to help you in detail ... but soy lethicin is an emulsifier, a release agent & a surfactant, so it sounds very useful in a number of ways including stabilizing the emulsion and reducing air bubbles.
Regards,
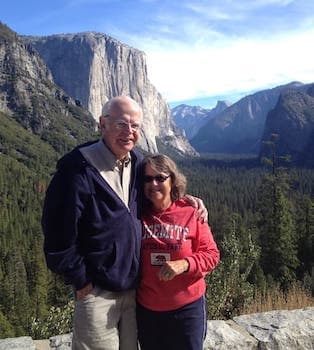
Ted Mooney, P.E. RET
Striving to live Aloha
finishing.com - Pine Beach, New Jersey
publicly reply to Ted Mooney
Tip: Readers want to learn from Your Situation π
(little can be learned from abstract questions, so many readers skip them)
Q. I require formulation for air drying (ambient temperature) plastisol or any other resin based ink formulation. I hope finishing users help me.
Suni milton- kochin kerala India
August 2, 2015
publicly reply to Suni milton
Q. I have been trying to make a plastisol from PVC resin by dissolving it in DOP. I used PVC: DOP in the ratio 25:36, and then made a colored plastisol with Titanium Dioxide and other pigments plus lead inhibitor in the ratio of 1% of total formulation to achieve a reasonably pasty product for dipping. However, when I used it for dip coating at 170 Β°C, followed by cooling under water, the end coat was still a bit sticky and not completely dry.
Would appreciate any comments
United Colorama - Alexandria Egypt
May 25, 2017
publicly reply to Nicolas Abdelsayed
Q. Hi,
I have an automatic screen printing machine and I made a white plastisol β¦ but it's sticky and didn't dry well. Please, I want the raw material which makes the white cured quickly without stickiness. Thanks.
Best regards,
art print - cairo, Egypt
August 12, 2017
publicly reply to ziad elsha
Plastisol Ink for Textile Screen Printing Production Process
Q. My situation: Dear finishing.com contributors,
We are starting to manufacture plastisol screen printing inks for textiles. For this we have already set up our factory, three-roll mills, mixers, etc.
We also took some consultations about the production process, how to best mix the chemicals.
However, at this point we are a bit lost, as we have two different suggestions for the production process. We are not sure which one is better, we only made small scale lab tests and both seem fine, but are not sure if in the long term one is better or correct for this purpose.
How we do the production is like this, the first approach:
1) First, add all liquid or paste chemicals into the canister while slowly mixing (plasticizer, additives, dispersants, etc.)
2) Add the PVC resin to the mixture and mix fast until the heat reaches 35 Β°C.
3) Then add the pigments, fillers, etc. and mix for 10 minutes.
4) Grinding at the three-roll mill.
Second approach is as follows:
1) First, add all liquid or paste chemicals into the canister while slowly mixing (plasticizer, additives, dispersants, etc.)
2) Then add the pigments, fillers, etc. and mix for 10 minutes at highest speed without the fear of overheating the PVC resin to make it gel.
3) Add the PVC resin to the mixture and mix slowly while the agitator blade goes up and down in the canister.
4) Grinding at the three-roll mill.
The consultant with the second approach claims that when you add the PVC resin before the pigments and fillers, you cannot disperse the pigments and fillers enough due to heat buildup which can cause the PVC resin to gel. And adds that adding the PVC resin at the last phase is the best solution, because to mix the PVC resin well into the mixture doesn't require high speeds but dispersing pigments need higher mixing speeds.
The first consultant we know has been consulting other manufacturers with successful productions and good quality phthalate free plastisol inks for textiles. But the second consultant is more technically capable with higher education in chemistry. So, we don't know which one to follow.
Would very much appreciate your help on this issue.
Regards,
Ibrahim
Manager - Bangladesh
July 13, 2018
publicly reply to Ibrahim Rahman
Q. Mr Rehman, I have the same problem with my plastisol ink. Also our ink is drying in screen. If you have solved your issue let me know. How did you do it?
Alfat sheikh- Bhavnagar
February 4, 2024
publicly reply to Alfat sheikh
Q. Hello,
Dear finishing.com community,
Let me introduce myself; I'm Ferry and currently doing formulation about white plastisol screen printing.
I have a problem with the viscosity. The viscosity to flow and I have tried some filler to increase the viscosity like CaCO3 and sodium aluminosilicate (ex: kaolin, etc.)
The first question is how to improve the viscosity to be easy to handle when printed on the cloth?
The second, when I finished the plastisol to mill in the three roll mills, the white color became too dark. What happened to this process? Meanwhile, according to the explanation in the discussion, put the plastisol in three roll mills to get better performance.
Please, give me an advance for this problem.
Thank you.
- Bogor, Indonesia
January 25, 2021
publicly reply to Ferry Saputra
Q. Hello finishing community,
I have a question, do you know any online training course which can help me with plastisol formulations for dipping and issues encountered and solutions?
Thank you
Abraham
- Waterloo Ontario, Canada
June 9, 2021
publicly reply to Abraham Ganipur
Q. Que tal. Me dirijo a usted para preguntarle los porsentajes y material para elaborar plastisoles textiles..ya que publico la instrucciones de elaboracion ... muchas gracias.
Queria saber si alguien me podria pasar la formula para hacer plastisol textil ... ya que aki es muy caro ... Por favor. Desde ya muchas gracias.
- Buenos Aires
June 24, 2021
publicly reply to Roly Canaviri
Nota del editor: Solo inglΓ©s por favor.
Q. Dear, we have clients; he want to make plastisol pvc inks for pvc stickers, and we face some problems in this manufacturing of inks , its drying time is not good, so we don't find some good chemicals.
Khawaja imranTrading company - LAHORE , PAKISTAN
July 6, 2021
publicly reply to Khawaja imran
Tip: Readers want to learn from Your Situation π
(little can be learned from abstract questions, so many readers skip them)
Q. What is formula of plastisol ink and solvent ink pvc?
I study how to make product screen printing product like plastisol inks and PVC solvent inks vinyl.
What is formula please?
- Algeria blida
publicly reply to Red obelisque
Q. Please, teach me how to produce plastisol ink, PVC ink and water based ink. Thanks.
CJ THE APPLE- ABA ABIA STATE, NIGERIA
April 12, 2022
publicly reply to CJ THE APPLE
A. Hi Red. Hi CJ. Plastisol and vinyl inks are commonly used in screen printing because they don't dry instantly, but offer you some time to work with them. They contain PVC, plasticizers, and fillers, as well as the pigment. But even a single manufacturer may offer a dozen different plastisol ink formulations.
Apologies, but "teach me how to produce ..." is probably well beyond what people are able to do in a public forum like this :-(
Patents.google.com, scholar.google.com, the SDS of such inks, and books on the subject β¨
will probably all be needed; then when your questions are able to become more specific, readers will probably be able to help you.
Luck & Regards,
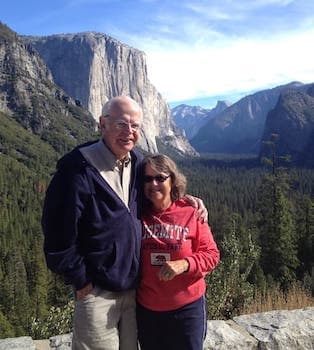
Ted Mooney, P.E. RET
Striving to live Aloha
finishing.com - Pine Beach, New Jersey
publicly reply to Ted Mooney
Q. Please,
teach me how to proceed water based inks for screen printing on T-shirt. Thanks
STUDENT - ABIA STATE, NIGERIA
publicly reply to CJ THE APPLE
Q. I am dip-molding molds to make marlin lure skirts β©
The problem I have is that the part is sticky and stays sticky after curing. I heat the molds up to 174 Β°C then dip into plastisol and back to the oven at 174 Β°C for 15 minutes. The company is not very helpful to solve the problem.
Can I get some advice as to solve the stickiness problem. I do not have the formula that the company used.
Leon Nolte- Mokoppane South Africa
December 3, 2022
publicly reply to Leon Nolte
Ed. note: Google tagged this page "ADULT SEXUAL CONTENT"
Huh? What?!
Maybe Melanie spotted the problem ...
Q, A, or Comment on THIS thread -or- Start a NEW Thread