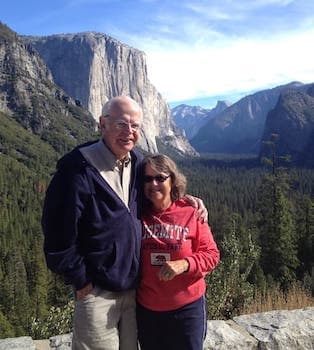
Curated with aloha by
Ted Mooney, P.E. RET
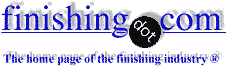
The authoritative public forum
for Metal Finishing 1989-2025
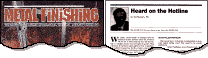
-----
Nickel-Tin Plating Problems
2002
Q. I am the Engineering Manager of an electronic components manufacturer. We wish to electroplate nickel and tin on a silver substrate. We are using a new technology for plating, I won't name the company, but perhaps some out there are familiar. The process of the machine is as follows:
1) Empty plating cell is filled with sample, no media is needed.
2) The cell moves to the nickel position.
3) The nickel anodes are suspended in a ss screen covered with a bag above the cell and then are lowered into the cell. (NOTE: the anodes are NOT in solution when not plating) using nickel S rounds and shot
4)The cell fills with a sulfamate nickel solution and the cell starts spinning. The centrifugal force holds the parts to the outer walls of the cell which in effect becomes the cathode. The cell spins and reverses to keep the samples from plating together.
5) After XXX amp-min, the cell drains, the anodes are pulled out and the cell moves to a rinse stage. cell is fully rinsed.
6) Cell moves to tin bath and process starts again.
My question/problem:
We are having one H__L of a time trying to keep these baths in range (metal concentration, boric acid, pH, everything goes). I have been told many things, including the fact that the anodes should never be removed from the solution. If this is true, the design of our plating machine is poor.
The tin used to be a very bright and shiny deposit, now it is a matte deposit. XRF indicates proper thickness. Solderability is no problem. What can be going on? Also, for the nickel, sometimes we get a very thin deposit for the same amp-min, and then again proper thickness. we clean the entire machine and anode daily. I clean the anodes in a 2% nitric acid solution for five min. because I am afraid it is O2 overnight while being dried out suspended over the solution. I am told by the plating chemical manufacturers that "dummy plating" is not required.
Thanks for any input you can give.
- Industry, California
A. Yes, in most plating lines, the nickel anodes are left in solution; an exception may be for strike solutions where it is desired to keep the nickel solution concentration low. Many shops periodically remove nickel anodes to clean the bags (or for replacement if they use bar anodes) though, and I'm not aware of any "start up" problems when they re-immerse.
Tin can be a different story. In alkaline tin plating, proper "filming" or "activation" of anodes is crucial. However, from your description of brightness, it sounds like you are using bright acid tin, not alkaline tin. At the risk of foolish oversimplification, it sounds like your tin bath may be low on brightener.
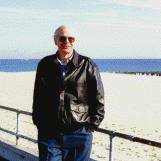
Ted Mooney, P.E.
Striving to live Aloha
finishing.com - Pine Beach, New Jersey
2002
A. A few thoughts:
Are the baths big enough? If you are making constant adjustments, it may just be that you don't have an adequate volume. I'd guess a reservoir of at least 4X the plating cell volume would be needed.
In my experience, it's normal for boric and pH levels to change constantly in nickel sulfamate baths. We measure and adjust pH every shift. But nickel levels are usually pretty constant. Do you have enough anode corroder? (chloride or bromide) Do you have enough anodes? We commonly leave our nickel anodes out of the bath overnight and sometimes for days at a time with minimal rinsing. I think anything more than a quick rinse is overkill.
Bright acid tin solutions need frequent additions of brightener. Has your vendor given you an addition rate based on amp hours?
Hope this helps.
- Chandler, Arizona
2002
2002
A. David,
My company uses this type equipment extensively for plating small ceramic capacitor components. We were also worried about the anodes being out of solution, but have never experienced anode passivation. You may have several root causes to your problems.
1. The chemical control issues could be caused by the small reservoirs of chemistry and uncontrolled dragout. Are you adding water automatically for level control? If so, you may be masking a problem of excessive dragout. It's amazing how much liquid can still be in the cell from poor drainage when the foam shim or cell orifices get plated up. This will be lost in the subsequent rinse. You should be closely monitoring all additions to this system and if everything changes proportionally, dragout losses are indicated.
2. "sometimes we get a very thin deposit for the same amp-min, and then again proper thickness" This issue is definitely not normal. This equipment has always given good repeatability on our parts, much better than our barrel lines.
Root causes could include:
- varying load sizes (plating area)without recalculating amp-minutes,
- poor maintenance of electrical contacts including rectifier cables, anode connections,and cathode brush connection. This would also be seen as varying times to complete the same amp-minutes.
- Each cell has a minimum volume of parts needed for optimum cathode coverage. Too few parts will cause the cathode to be exposed and thin plating on the parts.
- Simpsonville, South Carolina
A. Your nickel anodes can be removed regularly without problems.
There are enormous amount of possibilities that can produce problems with your design and chemistry. You are just grasping for straws trying to solve this problem on the internet. I have twenty five years of plating tin and sulfamate nickel on loose parts. Have you got any experience with vibratory plating or some of the new tumble platers? If you can get good results with your current system some or most of the time, it is probably a workable piece of equipment and process control and maintenance maybe your issue. If on the other hand your have been having problems from day one, then alternative methods maybe your best bet.Automating the chemistry on the type of chemistries you have does reduce the variability of the process enormously but it also requires a lot of other disciplines to maintain the equipment and do the calibrating.
- Lincoln Nebraska USA
2007
Multiple threads merged: please forgive chronology errors and repetition 🙂
How to maintain a Nickel-Tin plating bath
Q. I have been the wet process supervisor for a solar thermal manufacturing facility for quite some time and have been trying to address the life span of the Ni-Sn bath that we use to electroplate a black finish on to cu. The most important feature of the plating solution is the tin. As the age of the bath progresses, the 2 molecule tin converts to 4 mol and eventually the 10 mol. This is achieved through oxidation and ph changes. Because the 2 mol tin is is what I would like to maintain, is it possible to convert the 4 and 10 molecule tin back to 2 and still keep the integrity of the plating solution. The plating solution is made up of nickel chloride, stannous chloride (anhydrous), ammonium bifluoride, ammonium hydroxide, and D.I. water. The ph of the plating solution when operating at its optimum parameters is 5.8 to 5.9. To maintain the ph I use HCl to lower and ammonium hydroxide to raise it. If more information is needed, I will provide it upon request. Currently the life of the plating solution is 30 to 45 day's and then the tin will fall out of solution.
Raymond Villalva- Jacksonville, Florida, USA
2003
![]() |
2003 A. Where did you find the formula for tin-nickel plating. I have done tin-nickel plating but the formula that works best and does not oxidize tin is the following: - Plymouth, Michigan, USA A. Dear Raymond, - Odense, Denmark 2003 |
I have worked a long time on the Ni-Sn plating to diffusion PTFE in plating thickness. Now, obviously a good news that around 5%(wt) PTFE is entering in surface film which increases plating longevity at different complicated molds for releasinge sulfur-containing polymers.
Shuvra Majumder- Japan
December 6, 2010
YOU CAN USE THIO COMPOUND IN YOUR SOLUTION TO OBTAIN BLACK DEPOSIT.
REZA MOUMIVAND- Islamic Republic of Iran
November 30, 2011
Q. Hi,
I'm facing electrode turning black after winding and wire bonding. We manufacture ferrite core with Ag coated and Ni-Sn plated. Can somebody help me for this problem? Thanks.
QA - kuala lumpur
May 29, 2017
adv.: Supplier of Copper Anodes, Nickel Anodes, Bismuth Metal, & Other Metal Products for Industry & The Arts
Q, A, or Comment on THIS thread -or- Start a NEW Thread