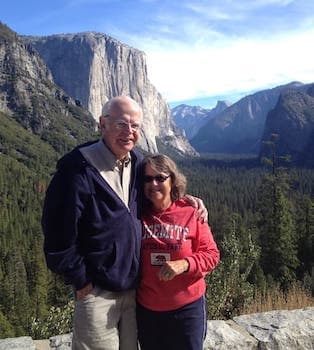
Curated with aloha by
Ted Mooney, P.E. RET
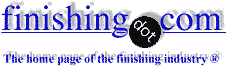
The authoritative public forum
for Metal Finishing 1989-2025
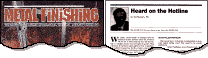
-----
Hastelloy welding problem
Q. I have to go to Tampa to the local to take a test on Hastelloy with a MIG gun. Never heard of such a thing. Any tips? If I pass this test I'll write back and give what I know.
I did Hastelloy at the bomb plant years ago but that was TIG'd. You keyhole the root in there if I remember right and it'll crack on you, so it takes some pre-heat. But yeah, real cold. You'll think it couldn't tie in but a constant and uniform advance speed is the trick. Stop and wait on anything and you got a mess.
As far as a repair goes you've got to cut it out fore and aft of the problem. It's not going to wash in. Feather every stop and your bevels.
UA local 421 Charleston, South Carolina
2003
A. There is a great deal of information available on welding various grades of Hastelloy from the website of Haynes International, the producer of these alloys.
Toby Padfield- Troy, Michigan
2003
A. Hello Jerry!
Good luck on the test! Having only book knowledge on welding these alloys, all I can suggest is checking out Haynes International (makers of Hastelloy alloys) site that discusses welding, at:
www.haynesintl.com/CRAfab/CRAweld.htm#Gen
It does list something for gas metal arc welding.

Lee Gearhart
metallurgist - E. Aurora, New York
2003
Well, I went to Tampa and took the Hastelloy weld test. It was pretty simple, a groove joint, 3/8 plate, 3 passes on top, back ground and one pass on back and a T-joint to be broken. It was a lot easier than I thought it would be. We used a Miller feeder with a pulse-arc pendant, .035 wire, a spray arc. It seemed unusually hot and heavily deposited to me but Mac-Tech had their parameters and we got in them. As far as welding went it seemed no different than any other alloy spray-arc I've used.
They would not let us grind on the weld. This caused me a little concern because a crust forms on top of the weld that multiplies with each pass. You can't brush it off even with a power wheel. It didn't seem to hurt anything though the X-rays aren't back yet. It's apparently to weld some type of attachments on some type of boiler components. We're working for a sub who's going through a temp whose working through a shop who's contracting for B&W so no one really knows much about what we'll be doing but the guy paid us everything he said he would before we left the test shop so one thing he does have is me :-)We ain't in this for our health you know. I'll update ya'll later.
Jerry P [returning]UA local 421 Charleston, South Carolina
2003
Yo Jerr. Me and my buddy cruised in his chariot down to Tampa for the test. We had no hassle with the hast. We finessed that rod like a lady. You gotta treat welding like you treat a lady. Real welders know how to lay the rod. Later, Big D.
Dustin O [surname deleted for privacy by Editor]- Connellsville, Pennsylvania U.S.A.
May 15, 2008
Q. We are trying to weld 0.125" thick Hastelloy using Argon gas and 2% Thoriated Tungsten. We are having trouble establishing a puddle and when we do the pkplate collapses or melts through like aluminum with an oxyacetylene flame. This plate has 25% Moly 10% Cr and 10% Ni with some other residual elements. Can anyone offer some advice?
Richard B Miller- Albuquerque, New Mexico, USA
2002
A. I don't read anything unusual with the equipment set up. Sounds like your problem is that you are waiting for a puddle to form and flow like stainless steel does. Hastelloy, Inconel and some other alloys do not flow, where you place the arc and the filler is exactly where your weld bead will be. Minimum heat input is needed for this type of metal. Back purging will be important.
Hope this helps you.
- Northfield, Minnesota, USA
2002
A. On a plate that thin of that composition you should be using lanthanated tungsten. And as far as your technique, try to focus your arc directly onto your filler wire with short waves onto the plate for blending and penetration. The previous comment about the back purge will definitely help too, but keep both your purge and torch between 10-15 CFM; too much pressure and you'll blow the joint out. Another angle you might consider is a consumable insert. They work wonders in high pressure and critical thickness situations.
Good luck.
US Navy 4955 coded "superwelder" - Rio Rancho, New Mexico, USA
2003
A. YOU'RE SET UP SOUNDS CORRECT, BUT YOU FAIL TO TELL ME IF YOU ARE WELDING ON AC OR DC. WELDING IN AC IS SIMILAR TO WELDING ALUMINUM.
JOHN RODGERS- JEANNETTE, Pennsylvania, USA
2004
A. In Ft. McMurray we are in the middle of a 200 Hastelloy joint job with the use of a tri-mix gas, purge puddle and weld appearance are all well within parameters; it involves changing weld procedure but it is WELL worth it.
Kkuly [surname deleted for privacy by Editor]- Edmonton, Alberta, Canada
2004
A. Change your gas on the torch to argon helium 75% Ar 25% He. It will stabilize the arc. You also must back purge or the weld will sugar, about 5 to 10 CFH of straight argon; amperage range depending on type of joint design from 80-130 DC straight polarity, pulsed TIG is also a option.
M Walters- Seattle, Washington, USA
August 26, 2009
A. The 75/25 mix is correct as well as the amps.
Create your puddle, then move off it, then come back and create the next one before the first is cold.
Hastelloy and Duraloy both cool fast so you have to move fast.
Stay in one place too long, you have a hole to fill in.
Nate (33 years of welding and retired)
- Heber Springs, Arkansas
June 24, 2011
Q. SMAW (shielded metal arc welding) or GTAW (gas tungsten arc welding) for Hastealloy?
I am going to begin a 3/16" Hastelloy plate job, and I was wondering if stick rod or TIG welding the plate would be better? I am on a timeline for completion, however I want the best possible welds for my welders to put out. Any advice?
Dustin HacklerSupervision - Angleton, Texas, USA
October 8, 2012
Q. I am going to weld Hastelloy C276 using microplasma welding. What problems may I face? Any suggestions?
Jobin georgestudent - trichy,tamilnadu, India
September 13, 2017
Q, A, or Comment on THIS thread -or- Start a NEW Thread