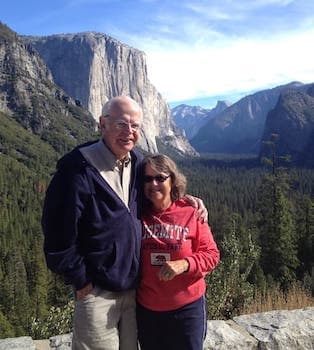
Curated with aloha by
Ted Mooney, P.E. RET
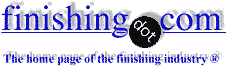
The authoritative public forum
for Metal Finishing 1989-2025
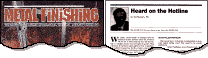
-----
Case Study - Hard Chrome Plating Problems - Crazing and Pin Holes
Q. I am a design engineer currently doing a case study at work for hard chrome plating problems as follows :-
1) crazing effect (also known as 'chicken wire' cracking and snakeskin effect)
2) pin holes
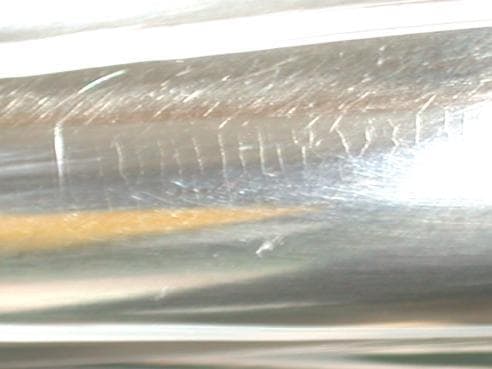
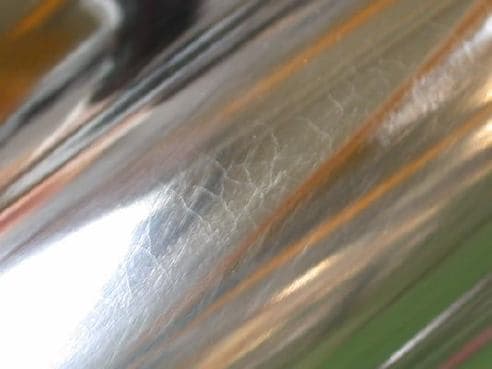
I would like to know what causes these problems and what effects they can have when pumping in oilfield applications.
The material being plated is precipitation hardening stainless steel to AISI type 630 (17 - 4 PH)which has been heat treated to NACE MR-01-75.
Please forward me any information you have.
Thanks,
- Manchester, England
2002
A. Mandy,
I would say the problem most likely lies in improper pretreatment of the base material. Otherwise it could be a result of excessive heat at the grinder operation (which you didn't mention if was carried out). Both situations may lead to crack patterns. Pitting, on the other hand, can only come from previous pinholes too small to be noticed, cleanliness of surface or lack of filtration before and during process. Most chrome platers are used to reverse etch conventional steel parts then forward plate them. This cannot be done with most SS as they will become passivated during reverse and will not produce good adhesion. They have to be activated in a special highly acidic formula.
Monterrey, NL, Mexico
2002
Q. Guillermo,
Thanks for your reply. What would you suggest for proper pre-treatment of the base metal ? The metal component is milled and then polished on automated machines using various grades of polishing belts. Once the component is received by the chrome plater, it is then given a pre-plate polish by hand grinding tools which as you suggest can be one cause of excessive heat. With regards to pitting and pinholes, our inspectors and the plating inspectors are currently looking for these in the base metal. This has shown an improvement. I will raise the point of filtration improvements with our plating supplier. I believe that our plater does reverse etch for approximately one minute. What would you suggest for cleaning the surface prior to plating ?
Regards,
- Manchester, England
2002
A. I would always try to inspect surface prior to chrome-plating to be sure that previously operation was right (as in process-inspection through visual inspection or microscope pictures, may be also by REM). Sometimes temporary protection was not good (by storage without preservatives - oils, VCI, etc.)
Stefan Svetsky- Dubnica, Slovakia
2002
A. Mandy,
Most experienced platers prefer the Wood's nickel strike (though there are other methods depending on facilities, etc.). This is a short forward flash of current in a solution containing 300 grams/liter nickel chloride salt plus 300g/l hydrochloric acid, rest water at room temp and 2 to 10 Amps/dm2 for 1-2 minutes. Some SS perform better if first given a short reverse etch in this same solution (10-30 seconds same conditions) some other don't need or like it. This activates the chrome and nickel present in the surface and leaves a very thin layer of almost pure nickel which promotes a good adhesion for chrome. Care should be taken not to let this layer dry and passivate again (oxidize) and chrome plating must be carried out with no delay, no rinse if possible and no reverse at chrome tank.
Hope this helps but in any way let us all know the outcome.
Bye,
Monterrey, NL, Mexico
2002
Q. Stefan,
Thanks for your reply. It may be that we can improve on pre-plate inspection. Before plating it is only a matter of a few hours before we dispatch the components to the platers - do you think it is still necessary to protect the component, or do you refer to protecting the bar before machining and plating ?
Guillermo,
I am not familiar with the different methods but I may be able to find out which method our plater uses. I believe that our plater does perform a short reverse etch. This is very good information, thank you for your time. I will let you know the outcome.
Best regards,
- Manchester, England
2002
A. a) No, some hours shouldn't be any problem. ... Before plating it is only a matter of a few hours before ... do you think it is still necessary to protect the component, or do you refer to protecting the bar before machining and plating...
b) I think you should also make some samples with chrome-coats electroplated by various conditions to try obtain coats with defects. Also to do porosity test - number of microcracks on cm2 - could be useful (may be the stress in coat is too high).
c) Did you try to measure mechanical impurities in bath?
- Dubnica, Slovakia
2002
2002
Q. Stefan,
b) We are currently in discussion with another plating company to see if they can replicate the 'crazing' effect.
c) We have not tried to measure the impurities in the bath ourselves but our plating company has a chemist who regularly checks the contents of the bath & makes the necessary changes.
Anders,
After chrome plating, the parts are given a polish using 'sateen' polishing wheels. The parts are not shot peened before chroming.
Ted,
After a visit to our chrome plating vendor, they are not actually using emery cloth but sateen finish polishing wheels. Apparently they are using the same wheels for rough polishing as for finish polishing, so each polishing wheel may not be at the same standard.
All,
I am currently putting together a report for my manager with causes and recommendations. It may be that we need to work closer with our plating vendor in the future. Thank you all for you help.
Best regards,
- Manchester, England
Q. Has anyone got any information on what causes pin-holes in HCP?
Mandy Bailey- Manchester, England
2002
A. Hi Mandy. I'm not a chrome plater, but a truism that I have been lectured about by a major chrome plating process supplier several times about is: Take a walk around your machine shop and pick up every piece of used emery cloth that is out there. Pay your machinists a quarter for each old scrap they'll give you if you have to! Only after there isn't an inch of old emery cloth anywhere will it be worth considering another possible cause :-)
Per those experts, the "old hands" frequently keep slightly worn emery cloth on hand because it's less dusty and not as aggressive . . . but it has tiny amounts finger oils and grease which can pit your plating :-)
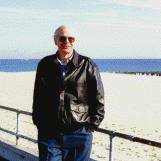
Ted Mooney, P.E.
Striving to live Aloha
finishing.com - Pine Beach, New Jersey
2002
A. Mandy,
You don't mention anything if the part are grinding after hard chromium. A grinding machining can cause chicken wire if the operator take more than 2 µm at each cut when the grinding operation starts. Also check which types of wheel the use they should be type K or L. Did the part also be shotpeened before hard chromium operation if the hardness is over 50 HRC. I don't believe the pretreatment method is wrong. Pinholes can occurs if the part is bad pre-machining, wax contamination in the solution high trivalent chrome.
Regards,
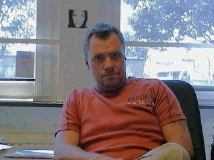
Anders Sundman
4th Generation Surface Engineering
Consultant - Arvika,
Sweden
2002
Can coefficient of expansion difference cause hard chrome plating on stainless steel to crack?
Q. I want to start looking at the differences in the coefficient of linear expansion between 17-4 Ph Stainless steel and hard chrome plate. Can anybody help?
Best regards,
- Manchester, England.
2002
A. Hard chromium thermal expansion coefficient is about 4 millionths per inch per Deg-F (7.4 microns per meter per °C) at room temp and increases with temperature (50% at 1,000 °C). 17-4ph steel is slightly higher (around 5 english, 9 metric) G. Marrufo-Mexico
Guillermo MarrufoMonterrey, NL, Mexico
2002
Q. Guillermo,
I am carrying out my master thesis in materials engineering about the oxidation process of Cr at high temperatures. I have a problem searching for data about the expansion coefficient. I have seen that you know the behavior of the expansion coefficient of Cr with the temperature. Do you know the behavior of the Cr2O3 too? How is the plot of its coefficient depending of the temperature (to 2000 °C)?
Thank you very much.
Regards,
- Barcelona
2003
A. As a very effective means of activating SS before Plating, try a method, what we generally refer as 'Hydrogen Flushing', i.e., raise the current in the Plating bath very slowly only to a limit, where the Hydrogen Gassing Starts but the Plating does not. This can be easily set, i.e., the current when the first Hydrogen Gas bubbles become visible. Let this be ON for a minute and then slowly raise the current to the final Current Density. This helps to a great extent in providing a good adhesion over SS.
Paramjit Singh- New Delhi, India
2002
A. Mandy,
I think that you must keep attention during 17-4PH steel cleaning process. This clean-up process is widely used!
I'm not sure, maybe it's inside AMS2460 - Plating, Chromium
We'd this problem pattern about one year ago and we noticed that it was generated during clean up process.
We are using a Sulfuric Acid and Hydrofluoric Acid-dip mix bath at room temperature for 3 min.
- São Paulo, Brazil
September 26, 2010
June 24, 2011
A. Mandy,
I would like to give information for relationship between hardness and Chrome plating.
17-4 PH has high hardness, so it has high surface stress also.
Some cases are cracked during ground condition as high hardness with severe grinding.
During Chrome plating, Hydrogen ion penetrated to 17-4 PH work.
Hydrogen ions combine to hydrogen gas in work surface, so the gas volume makes to high pressure with tensile stress.
Finally we get the cracked work piece by grinding crack or hydrogen embrittlement crack.
It is little difficult distinction between grinding crack or hydrogen crack.
However we can distinguish with removal plating and etching by nital (nitric acid 3% + alcohol).
If the removed surface has surface crack, the is evidence for pre-crack, grinding crack.
Simon
- Ansan, South Korea
Books about hard chrome plating
Q. Is there any book about hard chrome plating which I can easily access in India?
dhananjay patilPerfect Pins - Kolhapur, Maharashtra, India
April 1, 2012
by Robert K. Guffie
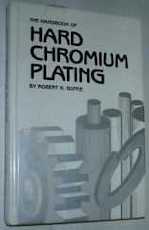
on AbeBooks
(rarely)
or eBay
(rarely)
or Amazon
(affil links)
A. Hi, Dhananjay.
I don't know if local libraries or local bookstores have it, but Guffie's "Hard Chromium Plating".
is the one book that I am aware of that covers how to do hard chrome plating and resolve problems. Good luck.
Regards,
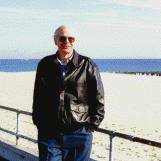
Ted Mooney, P.E.
Striving to live Aloha
finishing.com - Pine Beach, New Jersey
April 2, 2012
Cracks in Hard Chrome plating extend down to Base Metal
Q. I am noticing cracks in Hard Chrome plating. Defects are measuring 2 to 15 mm in length and depth of 0.03 mm to 0.4 mm (Cross Sectional Half). In SEM/EDX it is not showing any indication of presence of Non metallic inclusion. HR bars are peeled, reeled (1.3mm per side), Induction hardened and tempered and ground (0.4 mm over all) before plating. What could be the reasons for such defect.
GA PraveenQuality Engineer - Bangalore, India
May 14, 2014
"Tree bark" in hard chrome plating
Q. Dear sir,
I have a tank of around 30k ltr capacity divided into two cells referred as A and B. when rolls are hard chrome plated, on a smooth finish rolls having Ra value around0.8, I am finding a dendritic finish or tree bark like finish. the peculiarity is though both the cells are in same packet of solution, in one of the cell the tree bark finish appearance is more in one cell and in the other it is very faintly visible. to maintain temp uniformity, from the main tank solution falls into a weir tank from where it is drawn through pipe and pumped back into main tank through ejectors, these ejectors are close to the cell in which the tree bark finish is very lesser.
Can anybody help in sorting out this problem?
Warm regards,
Thyagaraj
Hard chrome plating of rolls - Bellary India
September 28, 2014
Pin holes and skip plating
August 2, 2015Q. 1- What is the "pin holes" in Hard Chrome Plating Process?
2- Do pin holes really come/develop in hard chrome plating? Or it is purely material defects which penetrates through surface of the metal?
3- What is the skip in hard chrome plating and how does it occur; give its solution and precaution.
Please reply to me asap.
Thanks
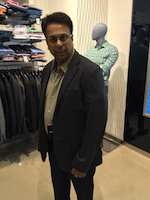
Nitin Doshi
Hard Chrome Plater - Mumbai, Maharashtra, India
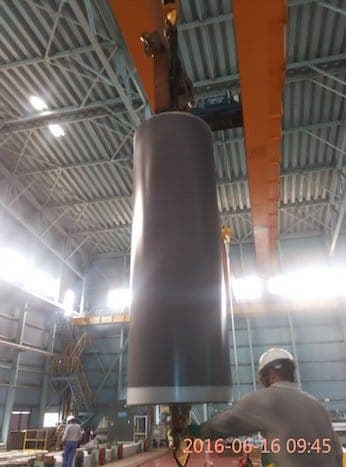
Q. Respected sir
Myself Vishal, I am working in hard chrome coating shop in steel industry. Sir I have a problem regarding coating of Steering Rolls. Sir I faced recently one problem where some portion of the roll is not coated and whole roll portions are not coated.
I recently checked all parameters like concentration of solution, which is 210 gm/L, cleaning of anodes, and activation of solution ... but after than I didn't get the desired Result. Roll material with this problem is SS400.
Sir I am so tired of this problem. I request you please give me valuable solution for this problem as soon as possible.
ThankS & REGARDS.
steel company - Maharashtra, India
June 29, 2016
by Larry Durney
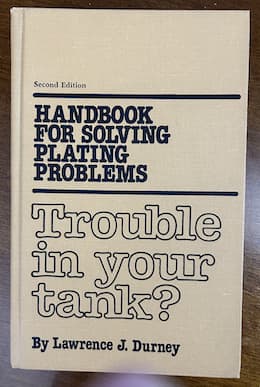
on eBay
(sometimes) or
AbeBooks
(rarely)
or Amazon
(sometimes)
(affil links)
A. Hi Vishal. I can appreciate your frustration that successful hard chrome plating can be very hard and you need to know what is wrong ... but your only options are either to retain a chrome plating consultant to help identify and fix the problems, or to learn enough to effectively troubleshoot the problem yourself. Although people would like to help you, they spent years learning how to chrome plate well, and are unlikely to be able to answer the question of what you are doing wrong that is causing partial coverage in a paragraph or two. But send photos of the problem, and describe what you are achieving and what you are not, and they can at least try. Good luck.
Regards,
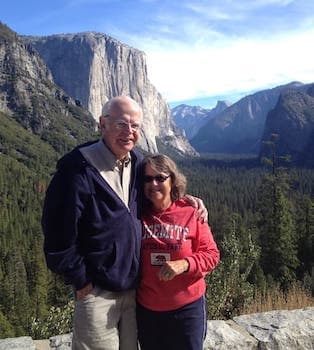
Ted Mooney, P.E. RET
Striving to live Aloha
finishing.com - Pine Beach, New Jersey
June 2016
June 29, 2016
A. How are you cleaning the roll?
How are you activating the roll?
What is your anode material?
What is the tank temp?
What voltage and current density are you using?
What is the anode to cathode distance?
What is your chrome to sulphate ratio?
- Navarre, Florida
A. A quick test for some of the issues your having is a specific gravity test using a common hydrometer. Look up the specific gravity of your plating bath composition then check the solution at the specified temperature and any reading higher than it should be is excess metals and/or trivalent chrome. Once this is known most (but not all) of these can be reduced using a porous pot (look it up) as well as dummying the bath to lower the trivalent chrome. The general rule is 1 oz per gallon MAX other metals (iron, copper, zinc, aluminum, etc.).
Larry SherrerElectroplater - newport, North Carolina USA
August 2, 2016
Eliminating surface defects prior to chrome plating
Q. Hello guys,
I have encountered a problem in our chrome plating process which I thought you can help me with ...
We have some defects on our rod surface before and after chrome plating, I know the main reason for this problem is poor surface treatment prior to plating but it seems that this problem is not occurring during our rod preparation process. After straightening the bars, we peel the surface at least 2 mm in diameter, we do the grinding process 3 times reducing 0.08 mm; and after that we polish the rods to get a complete fine surface which gives us the standard roughness we need after plating.
But it seems that there is a problem in the raw material that we have. Unfortunately we are not able to find a better provider for our raw material, consequently the flaws in the raw material (which might be because of the impurity level in the steel), will remain as very little black spots with 1 to 2 mm^2 area on the rod surface. No matter how much we peel the surface off, this problem remains the same. At average I can say there are 2 to 3 spots on each 6 m rod.
I was wondering if there was any other solution for this problem other than changing the raw material, something like filling the dots with a material prior to plating other than welding or brazing.
Thank you all in advance.
- Iran,Tehran
February 21, 2018
Q, A, or Comment on THIS thread -or- Start a NEW Thread