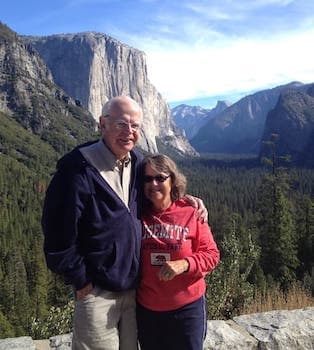
Curated with aloha by
Ted Mooney, P.E. RET
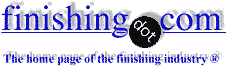
The authoritative public forum
for Metal Finishing 1989-2025
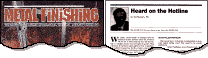
-----
Pitting problem in bright nickel plating bath
Tip: Readers want to learn from Your Situation 🙂
(little can be learned from abstract questions, so many readers skip them)
how to eliminate pitting bright star from satin nickel bath
walia parveenemployee - YAMUNA NAGAR [India]
December 12, 2021
⇩ Related postings, oldest first ⇩
Q. Hi everybody,
We use a bright nickel plating bath with the concentrations below and we have pitting problem in some parts (brass).
Total Ni: 85 gr/lt
Boric acid: 40 g/lt
Nickel chloride:59 gr/lt
All the brightener concentrations are at the optimum value. Surface tension of the nickel bath solution is 31,5 dyne/cm (after the last addition). We have observed the pitting and added anti-pitting agent to the bath but the pitting increased. We continued to plate and observed improvement so we added some more wetting agent but this time the parts started to come out with more pitting. As we go on to plating the pitting is decreasing but not totally disappear! Is there anybody having an idea about the reason and the solution?
Thanks for your kindly help!
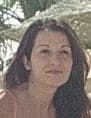
Sevim Topaloglu
- Izmir, Turkey
2002
A. Hi !
If you have pitting problem in your nickel tank, can be several reasons.
1. Check overhead structure on your nickel tank for leaking oil or grease.
2. May be you have compressor air in your nickel tank drawing oil into your tank continuously, would not completely help anti-pit chemical add.you need air blower instead of compressor air.
3. Check your nickel strike or copper strike before bright nickel tank any oil floating.
4. May be your parts are pitted before you plate or Electrocleaner rectifier adjusted too much current for those parts.
5. Check cleaning for those parts for water break test.
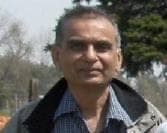
Popatbhai B. Patel
electroplating consultant - Roseville, Michigan
2002
Dear Popat,
Thank you very much for your response. Could you please give me information about this water break test?
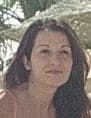
Sevim Topaloglu
- Izmir, Turkey
2002
A. Hi, Sevim. There are ASTM specifications for water-break tests, but what most platers mean by this phrase is that when a part is removed from the rinse after the cleaner tank and the rinse after the acid dip tank, the water must form a perfect sheet on the surface; there must be no breaks or dry areas as this indicates that the parts are not truly clean.
Regards,
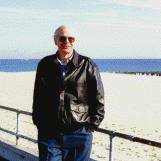
Ted Mooney, P.E.
Striving to live Aloha
finishing.com - Pine Beach, New Jersey
A. Mr Patel's advice is sound, however I would like to add some thoughts. Look at the pits. Are they like small explosions (gas pitting) do they have a tail (oil/grease?) or do they have regular edges (particulates). Is the pitting more pronounced in any one current density area (burning?, excess gassing) or more prevalent on flats (shelf roughness/particulates). Is your water supply "hard"
(high in minerals) if so could be from calcium particulates which redissolve when bath is cooled.
Finally, are you by any chance plating on leaded brass? This would necessitate a special cleaning process.
process supplier - Great Neck, New York
2002
A. Where do you have the pitting, is it all over the parts or only on the shelf ? If it is on the shelf, it means that you have to filter the solution. I assume that you use continuous filtration! The anode bags must be higher than the solution level. Lack of anti pitting is indicated by pits on the high current densities not all over the parts. As for water, you must use d.i.water for the plating solution.


Sara Michaeli
Tel-Aviv-Yafo, Israel
2002
A. Pitting may also occur due to lack of wetting agent.
Mark Camilleri- Malta
2002
A. When operating a nickel plating bath you must constantly use a carbon packed filter to prevent the pits. Pits can come from many different sources, you will have to investigate and see if and where you are introducing "contaminants" into the bath.
Benny Gumm- City of Industry, California, USA
2002
A. Hi Sevim Topaloglu,
As you are using brass parts for plating,your bath could have copper and zinc contamination. You will have to remove the contamination first to get pit free deposit.
- Kitchener, Ontario, Canada
2002
Clean the filter and put a new fresh carbon pack in it and filter overnight before attempting to plate, also if you are using air agitation be sure the air is coming from a clean source and not contaminated with any lubricant.
Benny Gumm- Apple Valley, California
Q. Preparation for a chemical bath for bright nickel plating using bright nickel salt? as I am an Experimenter, I would like to have advice on how to do bright nickel plating on (steel) small nuts and bolts using bright nickel salts, thank you.
Lloyd Pererahobbyist - Kelaniya, Sri Lanka
2006
A. Hello, Lloyd. This letter that you have posted against includes a nickel plating formulation and some notes about some typical problems and how to address them. But, as you can see, even the parameters for operation of the nickel bath alone -- let alone all the pretreatment steps -- is a very broad topic for an internet posting. Please see our list of "must have books" (I would especially recommend ASM Handbook volume 5, Surface Engineering as it will give you an introduction to the necessary brighteners, carriers, and wetting agents). Then get back to us with your more specific questions. Thanks!
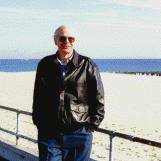
Ted Mooney, P.E.
Striving to live Aloha
finishing.com - Pine Beach, New Jersey
2006
Q. Hi Everyone!
We are also having problems with pitting. We add anti-pitting agent but it does not entirely eliminate pitting.
We plate metal parts for our company's mechanical counters. These parts include covers for the counters. We have two types of cover, one is thicker than the other. The thinner one will either be plain or will contain company logo (which I think is done using press machines).
We encounter more pitting with the thinner cover which contains logo. Also, adding anti-pitting agent helps more with the thicker cover but not on the thinner one. So I'm thinking that thickness somehow affects appearance of pits. I also think that the design on the cover affects the appearance of pits (due to recessed areas).
Am I right with my assumptions? If yes, what can we do about it?
- Rosario, Cavite, Philippines
October 19, 2009
A. Hi, Sieglend. Considering what you have told us, and assuming that you have reviewed the previous responses to this thread without solving the problem, my feeling is that the "stamping process" is embedding oil into the cover that your cleaning process is not able to remove.
Please pull a number of these logo cover plates and scrub them well with powdered pumice
⇦ this on
eBay or
Amazon [affil links] and a tampico brush before racking them for your regular pretreatment and plating, and tell us the result. If the problem goes away on the hand-cleaned parts, you know that you need to improve your cleaning process to deal with the problem. Good luck.
Regards,
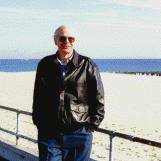
Ted Mooney, P.E.
Striving to live Aloha
finishing.com - Pine Beach, New Jersey
October 19, 2009
July 15, 2010
A. Dear...
Everyone faces this problem so you should follow the steps:
1- you should make chemical analysis to know the concentration of Boric (Boric decrease = pitting)
2- measure pH (should be from 3.5 to 4.5) and the ideal is 4.2 (more acidic = pitting)
3- use DI water
4- make sure about type of anti pitting agent (powder for Trembling [mechanically agitated] bath) (Liquid for blower bath)
5- perfect clean for surfaces
6- anodes bags level must be higher than solution level and must be cleaned in hot water before use if it made from cotton
7- Continual filtration must used.
- Egypt
A. How pitting made?
"During the electrolysis of a water base plating solution, hydrogen is evolved at the cathode surface. Very minute bubbles that form should get quickly detached and escape from the cathode surface towards the open surface of the solution. At a spot, where the bubble has lingered, deposition is reduced and a pit is left."
In addition to above comments,
if pitting is with foggy deposit then possibility of chromium will be a cause.
- Delhi, India
November 27, 2009
A. PLEASE ALSO CHECK CURRENT DENSITY
NICKEL ANODE
SEMI BRIGHT NICKEL TANK
NICKEL CHLORIDE CONCENTRATION
- Lahore, Pakistan
October 21, 2010
Q. Facing pitting in bright nickel, especially when applying a current density @25 amp/sq. ft. Component is cycle handle bar.
At low current density there is no pitting problem.
- Ludhiana Punjab India
May 24, 2013
A. More current more tiny bubbles, more bubbles more tendency to hydrogen cling on surface.
It is just the first thing I have in mind, check wetter.
- Bucaramanga, Colombia
June 15, 2013
Q, A, or Comment on THIS thread -or- Start a NEW Thread