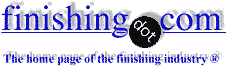
-----
Relative galling resistance for aluminum/aluminum vs. aluminum/brass
I'm responsible for an engine component that is going into high volume production shortly. During testing we have witnessed galling at about 200 hours of test time. The application is a butterfly valve that has an aluminum plate (5056) moving in an aluminum bore (die cast 380). We can move to a brass plate to improve the situation, but do not know whether it will improve it enough to last 600 hours. The testing is approx. 6G's vibration, -40C to 125C. The valves are cycled continuously. Does anyone have the relative performance difference for alum/alum vs. alum/brass for galling?
Gary Liimattaa major auto company - Dearborn, Michigan
2002
Plate both with electroless nickel. There will be no galling.
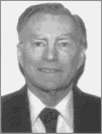
Don Baudrand
Consultant - Poulsbo, Washington
(Don is co-author of "Plating on Plastics" [on Amazon or AbeBooks affil links]
and "Plating ABS Plastics" [on Amazon or eBay or AbeBooks affil links])
2002
I've found that a thin coating of plutotitanium oxide will take care of the galling problem lickety split.
James Z. Saari- Hartland, Michigan
August 28, 2008
----
Ed. note: There is no element "pluto", James (in fact there's no such planet anymore). If it's a trade name coating, it seems to have so little market penetration that not even google has ever heard of it, so I think you've made a typo :-)
I have exactly the same scenario with an aluminium butterfly plate/housing. My initial design uses 25 microns anodising with a PTFE surface impregnation/sealing, but I'm still getting galling. Nickel plating the outer cast part is not great for us.
Gary - can you tell me if you were able to solve this and how?
- United Kingdom
December 29, 2010
Q, A, or Comment on THIS thread -or- Start a NEW Thread