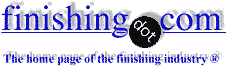
-----
Problems with nickel coatings for electrical contacts
The switches of our electro-surgical products are registering high impedance/unstable readings during production testing. The switch design consists of a Nickel coated SS dome that completes the contact between two printed circuit tracings. The readings become stable if a small current is run through the switch prior to the multimeter reading. Our problem is that we don't know if nickel coatings tend to build some kind of an oxide layer over time (especially after the sterilization cycle of the product which uses high temperature and moisture), or if in fact these parts are actually coated or not. EDX analysis by an outside laboratory shows that there is no coating on the parts, but the dome supplier claims otherwise. Do nickel parts oxidate/tarnish/sulfidate over time? Are there any other sure ways of determining if a nickel coat is present?
Arnold Oyola- Raymond, New Hampshire
2002
First of two simultaneous responses --
Nickel will tarnish over time. Try soaking the part in 5-10% sulfuric acid for a few minutes. Nickel should tarnish, stainless won't. Most people put a flash of gold on top of the nickel to prevent oxidation and electrical breakdown.
Kevin Keating- Rochester, New York
2002
Second of two simultaneous responses --
Arnold,
A droplet of concentrated nitric acid will attack nickel and electroless nickel but not most stainless steeels. The attack will leave a dull surface for conventional nickel and a dark brown for most EN's (high and medium phosphorous).
Guillermo MarrufoMonterrey, NL, Mexico
2002
Q, A, or Comment on THIS thread -or- Start a NEW Thread