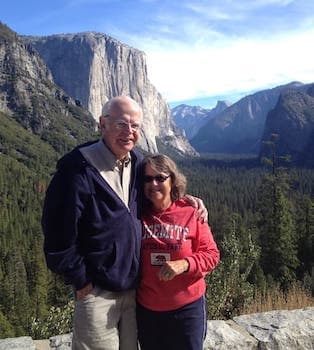
Curated with aloha by
Ted Mooney, P.E. RET
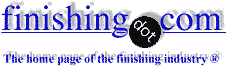
The authoritative public forum
for Metal Finishing 1989-2025
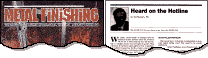
-----
Problems with press fitting gold plated parts
We currently press fit a coax cable with a gold plated copper outer jacket into a nickel/gold plated brass plate. We used to press the cable into a stainless steel plate with an equivalent interference fit. Since we have gone to the nickel/gold plated brass plate, the insertion forces have more than doubled. One difference between the plates is that the holes in the nickel/gold plated brass plate are very smooth when compared to the stainless steel plates, due to the plating build up. Has the smoothness of the hole increased the friction as a result of the increase in contact surface area, or are we experiencing gold on gold galling? Is gold on gold a problem, or is there some other reason the insertion forces have doubled?
Dave Tegliatelecom company - Petaluma, California, USA
2002
First of two simultaneous responses --
Don't take my word for it because I know little about the subject, but ask somebody about 'cold welding' of gold. It is my understanding that if you merely press two clean gold surfaces together under high pressure they will form a good weld. Press fitting two gold surfaces together sounds like it could constitute welding them together--no wonder it's hard to keep the insertion going.
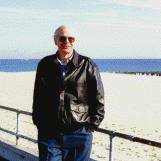
Ted Mooney, P.E.
Striving to live Aloha
finishing.com - Pine Beach, New Jersey
2002
Second of two simultaneous responses --
I suggest "Hard" gold plating over the nickel plated base and hard gold on the insertion part. Hard gold is made hard by co depositing cobalt or nickel in small quantities (sometimes iron) with the gold.
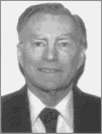
Don Baudrand
Consultant - Poulsbo, Washington
(Don is co-author of "Plating on Plastics" [on Amazon or AbeBooks affil links]
and "Plating ABS Plastics" [on Amazon or eBay or AbeBooks affil links])
2002
With your unplated hole with a rougher surface, your measurement of hole diameter (to assess the interference fit) will be made using the tops of the surface irregularities. When you press coax fitting into place, the bumps can be deformed so that they cold-flow into the hollows of the surface. So your effective final interference fit is a bit less than you thought it would be, as the cold-flow mechanism has the effect of slightly increasing the hole diameter.
If you then change to a smooth plated hole with the same diameter as you measured on the previous rougher surface, there are no longer any hollows for any material to cold-flow into, and your effective final interference fit in this case is what you would expect from the initial inside and outside diameters.
The insertion force is now higher because you are actually using a greater interference than previously.
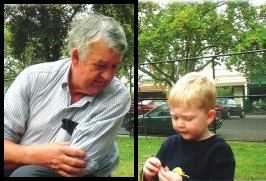
Bill Reynolds [deceased]
consultant metallurgist - Ballarat, Victoria, Australia
We sadly relate the news that Bill passed away on Jan. 29, 2010.
2002
Yes, there is a tendency in soft gold to get cold welded. Hard gold (Nickel/cobalt alloy in small %) is not prone for this property, but at the loss of contact resistance. The contact resistance in soft gold (pure gold plating) is low, this is especially observed in relays where high frequency switching is used. Some times at high frequency switching the contacts may get cold welded if soft gold is used, hard gold doesn't have this problem to the extent soft gold has. SO probably you can try hard gold plated over the nickel surface. If you are more interested in the contact resistance, you can plate Ni followed by Gold followed by rhodium or ruthenium.
Good luck ....
Karthik- Singapore
2002
Q, A, or Comment on THIS thread -or- Start a NEW Thread