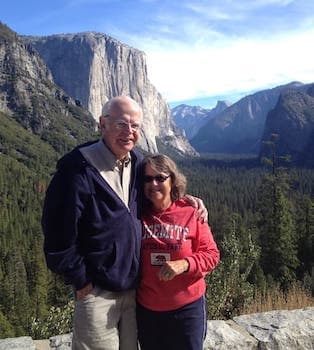
Curated with aloha by
Ted Mooney, P.E. RET
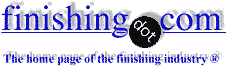
The authoritative public forum
for Metal Finishing 1989-2025
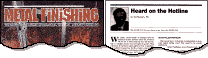
-----
Phosphate coating & part temperature limits
Q. Greetings from Denmark
I would be very grateful if you could supply information about the temperatures phosphate coatings on steel (iron-, zinc, zinc/calcium- and manganese-phosphate) can be heated to in air without getting damaged. The phosphate coatings shall be used as pre-treatment prior to heating in oven and polyethylene-coating in a fluidized bed process.
Looking in the literature is a bit confusing, as the maximum temperatures referred range from 150 °C to 500 °C. However most of the references give a limit of 250-300 °C.
Can you help me out of my confusion. Literature references to new results would be very much appreciated.
Best Regards
Torben Jense, Mc.S, Ph.D- Brøndby, Denmark
1998
2001
Q. Dear Reader:
We are having a dispute in our company as to the maximum temperature (and time) we can have in our dry-off oven without dewatering our lightweight iron phosphate coatings produced in our 6 stage spray washer. We also have another line that uses zinc phosphate for automotive parts, and have disagreed as to the maximum temperature (and time) for that dry-off oven as well - before dewatering of the coating occurs.
Does anyone have a technical article that they can refer me to so I can read it for myself, or, if not, let me know by response to this inquiry in the usual written fashion.
Many Thanks,
Tom Meyer- Milwaukee, Wisconsin, USA
A. Hi,
Stoving times are very flexible. At temps above 150 °C for 20+ mins 2 molecules of water will be driven off from zinc phos. This is NOT detrimental in any way. Above 250 °C complete dehydration will occur and this will most definitely adversely affect performance. Lightweight iron will be less affected. In short you could use powder cure temps for drying and not suffer!
Roger Bridger- Croydon, UK
2001
Multiple threads merged: please forgive chronology errors and repetition 🙂
Q. I recently saw in an Air Force Technical Order that zinc phosphated coating is not to be used on parts exposed to temperatures above 200 °F. Why would this be since zinc phosphate is recommended as a pretreatment by powder coating manufacturers whose coatings are cured at temperatures in excess of this?
Joe Yochum- Warner Robins, Georgia, USA
2002
![]() |
2002
"Preparation of Metals for painting"
by Samuel Spring ![]() on eBay (currently) or AbeBooks (rarely) or Amazon (rarely) (affil links) A. Hi, At 150 °C phosphate will lose 2 molecules of water, which is not harmful and can indeed improve performance. Above 250 °C total dehydration occurs which causes partial destruction of the structure. These figures refer to exposure when uncoated. Curing of the paint film at < 220 °C does not affect coating integrity. Roger Bridger- Croydon, UK A. Zinc phosphate heated above 200 °C gives off water of crystalisation after ~30 minutes at that temperature, which turns the crystal coating into an amorphous layer that reduces corrosion resistance and adhesion. Paint or powder stoving for the recommended time seals the coating and prevent this loss so the crystals stay complete. Robert D Lilley- Singapore 2002 |
Q. What is the decomposition temperature of zinc phosphate coating on steel parts? What is the recommended operating temperature for such parts? Can you please support your data with the resource?
Aida Ratner- Cleveland, Ohio
2005
Multiple threads merged: please forgive chronology errors and repetition 🙂
Q. We have a cylinder application using 4130 steel with zinc phosphate internal finish to store high pressure oxygen. Our customer (US Military) has heard that at above a certain interior or surface temperature, the coating will start to off-gas with possible toxic results. We have reviewed TT-C-490
[from DLA]
but cannot find anything specific to this situation.
Can anyone provide information on what maximum temperature is allowable for zinc phosphate coating before it will start to off-gas? The maximum fill temperature is 125 °F, but we expect the internal temperature may exceed this.
Thanks,
cryogenics - St. Louis, Missouri
2005
A. Hopefully, some company that manufactures it would have that research. If not, try finding the right office at the Rock Island Arsenal. They are or were the OPR for that mil spec and years ago had one of the best knowledge basis of anyplace.
James Watts- Navarre, Florida
2005
Q. What is the behavior of a zinc phosphate film at high temperatures, i.e. above 700 °F - 900 °F? Possibly higher?
Carlos Alvarado- Houston, Texas, USA
March 27, 2013
April 2, 2013
A. Hello Carlos!
Over 300 °F you have phosphate dehydration, so the layer itself tends to decompose, and any sealer you can put on it will not have any effect, the anticorrosive properties are lost and the surface tends to corrode.
It is different if you have a topcoat over the zinc phosphate, then you must read the topcoat technical sheet and look for its maximum operative temperature. We use some topcoats that will behave normally up to 400 ° F, but I don't know if there is any topcoat that can handle 700-900 ° F...
Hope this can answer your question! Regards,
- Cañuelas, Buenos Aires, Argentina
A. Not all of the zinc phosphate will be lost. I have done testing on panels that had zinc phosphate pretreatment; cat-epoxy e-coat; and polyester powder. I burned off the coating at 800 °F. Then ran the panels through pretreatment, e-coat and powder again.
The burn off panels outperform control panels in salt spray and in cyclic testing.
- Horicon, Wisconsin
July 10, 2013
ZnPO4 and heat
Q. My situation: I have a concern for the quality of my zinc phosphate coating after it is cut down to size with a plasma torch. It seems the coating weights are lighter than they should be, raising concern that we are vaporizing the ZnPO4. I know it melts around 1600 °F but I cannot find at what temperature it vaporizes. In addition, I am having trouble knowing what point (distance) from the torch cut is reliable for testing of my crystals and weights.
Unfortunately, we are unable to cut with a bandsaw due to safety concerns. I am struggling to know if my plasma cutter is 'destroying' my zinc phos layer or if my pretreat system is insufficient. Help?
Engineer - Princeton, Indiana
July 6, 2018
A. Hi Shannon. I don't know enough about your situation to say exactly what should be done in your circumstance, but certainly the general rule would be that whether a plasma torch leaves any remnants of the phosphate or not, it will essentially completely destroy its protective value; phosphating is generally done after all metal working is complete, and immediately before painting. Good luck.
Regards,
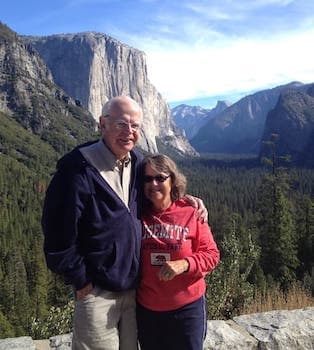
Ted Mooney, P.E. RET
Striving to live Aloha
finishing.com - Pine Beach, New Jersey
July 2018
Q. Let me try again--I am looking to verify my zinc phosphate crystal structure, size and coating weight. To do this I must cut my parts to send samples so they can be checked via SEM. Some of the parts are very large. The question is: will plasma cutting alter the coating weight/area, crystal size, structure etc? What is the temperature limit of the zinc phosphate for cutting? I am trying to determine how far away from the plasma cut I need to further cut my sample say with a band saw.
Shannon Ulewicz [returning]auto manufacturing - Princeton, Indiana USA
July 6, 2018
A. Hello Shannon,
My experience is that with a few seconds of exposure at 300 °F you alter the structure (crystallization water just evaporates and the crystal loses weight and properties), and more than this temperature is harmful to your coating.
As Ted said, this type of conversion coating is applied usually near the end of your process. If your client will put your samples in a SEM microscope, I would go to the band saw as my only viable option.
Good luck!
TEL - N FERRARIS - Cañuelas, Buenos Aires, Argentina
July 10, 2018
A. Hi Shannon,
Maybe I'm missing something here, but why can't you section before phosphating and run the sectioned part concurrently with the production part? This way you have no heat effect from cutting to take into consideration.
Aerospace - Yeovil, Somerset, UK
July 13, 2018
Q. The geometry of the part will affect how the inside coats, etc. If I cut it beforehand, I am no longer representative of what the customer is going to receive. Drain holes, geometry, size, true orientation going through the baths all matter …
Shannon Ulewicz [returning]Auto Manufacturing - Princeton, Indiana USA
July 13, 2018
Hi again Shannon. It's certainly possible that you simply can't take Daniel's or Brian's route. But it's also true that the things you mentioned are not the only things that can effect a coating. It can also vary from one part to the next due to a myriad of factors, or might be out of spec in a microscopically small area on the part which you never test, etc. You can never 100% eliminate all possible butterfly effects and prove that any test is absolutely representative. So it's common to test specific quantities, and to test dummies/coupons rather than the actual parts, etc., even on life-critical aerospace parts.
In the end you may be forced to discard Brian's suggestion, but I definitely wouldn't do so hastily. A properly precut actual part might be quite close to representative; envision a precut part temporarily glued back together as an example :-)
Best. of luck. Regards,
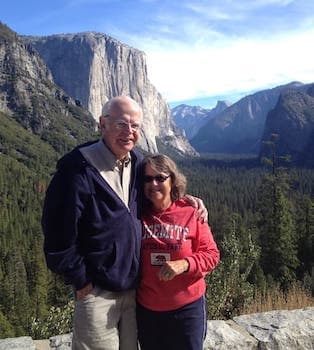
Ted Mooney, P.E. RET
Striving to live Aloha
finishing.com - Pine Beach, New Jersey
July 2018
Q, A, or Comment on THIS thread -or- Start a NEW Thread