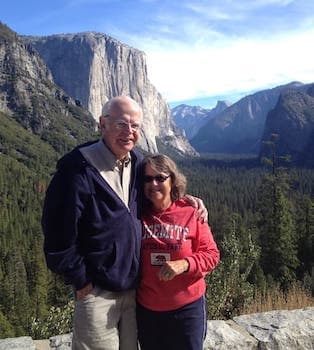
Curated with aloha by
Ted Mooney, P.E. RET
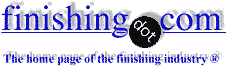
The authoritative public forum
for Metal Finishing 1989-2025
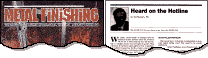
Thread 154/79
Hard chrome plating of work rolls for cold rolling and skin-pass
Q. My steel company intends to install a new state-of-the-art hard chrome plating plant for plating of work rolls of cold rolling and skin-pass mills. Material to be processed: Carbon and alloy steel oiled rolls. In this respect, I'd like to know what is the coating layer applied on the surface of the work roll? What are the techniques/criteria to measure the lifetime of chrome plated work rolls and plain work rolls?
Valery KNYAZIKHIN- Magnitogorsk, Russia
2002
publicly reply to Valery KNYAZIKHIN
A. The coating layer is pure chrome so you will increase the hardness to more or less 1000 Hv.
Chrome is very fragile and on these kind of rolls a thick layer will break down because of the big forces involved in the mill. 10 to 20 microns will be ok in most cases. But thickness will be different depending on the stand and depending on the rolls (hardness, diameter, crown...)
Chrome will extend the life of your rolls between 2 and 5 times depending on the number of incidents you have in the stand. Chrome works OK under wear conditions but will break if you have incidents with big local loads. In the stands that you have a lot of incidents, chrome will not be economically attractive.
One way to measure life extension mainly in skin-pass and temper mills is to measure the evolution of roughness vs. km of strip.
Angel Vidal- Spain
2002
publicly reply to Angel Vidal
Multiple threads merged: please forgive chronology errors and repetition 🙂
2006
Q. Dear All,
I work as a process engineer in a cold rolling company in Egypt. I want to make a trial of chrome plating our work rolls that are used to cold roll carbon steel sheets. I need to know what would be the most suitable thickness of the hard chrome layer for the following operational conditions:
1- Pressure on roll: 1 ton on every 1 mm of the roll surface
2- Tension: 1200 N on the steel sheet
3- Mill type: 4 stands reversible mill
4- Thickness reduction: from 3 mm to 0.3 mm on sevral passes
5- Steel sheet type: Carbon steel DD-11, DD-12 (.04 % carbon)
Roll specifications:
1- Weight: 2.5 tons
2- Size: 460 x 1350 x 3161
3- Material: Forged hardened steel
4- Cr %: 2-4
5- Hardness: 91 HSC
Please give me feed back concerning the hard chrome layer.
- 10th of Ramdan city, Egypt
publicly reply to Amr Aly Mohamed
A. Work rolls are subject to such enormous composite stresses that a perfect balance between internal flexibility, outer hardness and toughness, thermal resistance, wear resistance and thickness of hard layer is essential. This last concept associated with roll life is normally measured in inches (or large fractions of an inch), not thousands, like chrome. From the standpoint of wear resistance, what would be considered a significant thickness of hard chrome plate, will be very close to its adhesion strength limit, thus will easily flake off. Chrome works fine only for low pressure operations where wear is the main factor such as temper mill rolls, skin pass rolls and idle rolls.
Guillermo MarrufoMonterrey, NL, Mexico
2006
publicly reply to Guillermo Marrufo
Oh, the things I never thought about and didn't appreciate :-)
Thanks for the informative postings, Angel and Guillermo.
Regards,
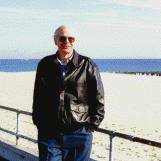
Ted Mooney, P.E.
Striving to live Aloha
finishing.com - Pine Beach, New Jersey
publicly reply to Ted Mooney
Q. Dear friends;
We want to do chrome plating on our skin pass rolls and then our temper and reverse (cold rolling) rolls. At first we want to test our skin pass rolls with roughness. The lifetime of our rolls are about 70 km now.
Is it reasonable to do this process and do it after or before shot basting?
- Iran, Qazvin
July 12, 2014
publicly reply to mohammadreza ourang
Q, A, or Comment on THIS thread -or- Start a NEW Thread