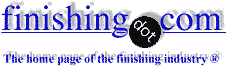
-----
Hcplating high C steel
Dear sir,
We are hard chrome plating rings of high carbon steel material of the following dimensions 150mmID X 180mm OD X20mm thick. The plating is required all over the surface.We are placing the ring for plating with its axis horizontal. The central anode is also placed horizontally and the and plate the ID and faces in the first setting. The rings are subsequently stacked and top of each other to plate other OD To avoid gas trapping on the topside of the ID during the first setting ,but the problem we are facing is that we get a pitted deposit on the bottom of the ID. We thought this was due to suspended impurities which were settling down during plating. As a remedy we tried filtration of the solution as well as solution movement by pumping during plating,but problem has persisted We would like to know the causes of the above problem and the possible remedy.
Thanks and Regards,
Malhar Talim-Thane, India
2002
When you stack the rings for O.D. plating, you have a cylindrical or shaft shaped article to plate, if I'm reading your letter right. I don't think you can plate a cylinder horizontally without rotation. How about plating it vertically?
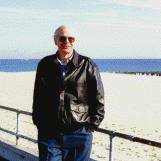
Ted Mooney, P.E.
Striving to live Aloha
finishing.com - Pine Beach, New Jersey
2002
2002
Further to my question I would like your views.
The rings we are plating are small in length (20mm). Since the quantity involved is rather high the orientation of the rings is such that the ID of 5-6 rings are aligned horizontally with a common anode. This is very convenient for higher production rates There is a substantial gap between the successive rings to help the escape of Hydrogen gas liberated during plating and additionally the whole assembly is given sufficient inclination in plating bath In this configuration the ID and the faces are plated in one operation and the thickness distribution over these surface is rather uniform with proper fixturing The problem of pitting is limited to a small region on the bottom side (horizontal portion) of the ID,and we are unable to identify the cause for the same. We have checked the bath for suspended impurities The plating bath is high efficiency non etch bath with new generation catalyst, while the etching is carried in silicofluride catalyst bath.
Can the following be important
1. Metallic or other dissolved impurities in the bath
2. Bath imbalance-High Trivalent or sulphate
3. Some chloride chemical reaction between the catalyst in the bath and the component leaving salt residues Impurities shed by the anode portion lying directly above the plating area
4. Will using a simple conventional chrome plating bath help in any way
Thank you,
Malhar Talim- India
A picture is worth a thousand words; I've tried twice now to picture what you are describing and I'm lost. Please make a sketch.
But one thing that sounds like trouble is etching in a silicofluoride bath. I had always been under the impression that the only bath suitable for etching service is a straight conventional (sulphate only) bath.
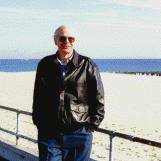
Ted Mooney, P.E.
Striving to live Aloha
finishing.com - Pine Beach, New Jersey
2002
Hello Malhar Talim,
What anode material do you use? If you use a lead-alloy anode the pits come from particles (lead chromate) which originate through anode corrosion. In this case you should use an anode bag (chromium acid ressistant). Another possibilities: - using of platinum-plated titanium anodes - vertical chromium plating.
Best regards,
Michael HekliSwitzerland
2002
Q, A, or Comment on THIS thread -or- Start a NEW Thread