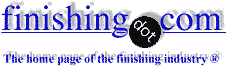
-----
Alternative daguerreotype plate
2002
Firstly I'm an architectural photographer and know little about electroplating and finishing. I'm doing practical research into the daguerreotype process which traditionally involves a highly polished copper or brass plate, electroplated with silver and highly polished to what has been described to me as a "blackness of polish". The problem is in practice this is very difficult to achieve being as the surface of copper or brass plate has fine milled lines and when machine or hand polished these just seem to be replaced with buffing cuts and you end up with a slight ripple finish.
What I'd like to ask is, is there a sheet metal that can be electro-silver plated onto which is produced with a very flat surface to begin with. I was thinking of SS but I've been informed that this needs to be etched before it can be plated onto. I've also been informed of vacuum deposition or splutter deposition of silver onto glass, however the cost of this process rules it out for me. If anyone can help it would be most appreciated.
Thanking you,
Chris Kargotis- Birmingham, UK
Interesting points here. Firstly, I would suggest you refer to Daguerre's original patents, a copy of which can no doubt be found in the Birmingham City library. I would have expected this to describe how he prepared the plates and if you want to replicate true Dageurreotype, you should use the original materials and processes.
Secondly, I agree with you about the problems of polishing brass and copper, but have you tried using Hull Cell ⇦ huh? plates and polishing these? They can be obtained from a very well known chemical supply house in Birmingham. You may find it beneficial to use jewelry polish, so talk to people in the Jewelry Quarter.
Thirdly, you can plate stainless steel with silver, but you may well run into similar problems with the finish. Also you will find to get good adhesion, you will have to use a cyanide based solution; if you are not used to handling cyanides, don't even think about it because you will run the risk of killing yourself and others!
Fourthly, you mention vacuum or sputter coating glass with silver; these techniques are good, but the capital cost can be quite high. It is relatively easy to sputter coat things if you have a glass bell jar, a vacuum pump and a high voltage supply, but you need to know what you are doing. I recall an article about 35 years ago in Scientific American that described exactly this process.... and it worked, because I tried it! However, have you considered silver spraying glass? All you do is have two air spray guns; one discharges ammoniacal silver nitrate and the other discharges a reducing agent such as glucose. The aerosol mists of the two solutions should be focused just above the glass plate and the mist will then condense onto the plate, where the glucose will reduce the silver nitrate to silver - hey presto, you have a silver coating and a mirror to boot! It is essential the glass is spotlessly clean and free from any surface contaminant.
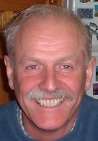
Trevor Crichton
R&D practical scientist
Chesham, Bucks, UK
2002
Thank you for your reply Trevor, you mention hull cell plates. I'd much appreciate it if you could inform me as to what Hull cell plates are.
Thanking you,
Chris Kargotis- Birmingham
2002
They are brass plates made to fit a special piece of electroplating test equipment called a Hull Cell. Birmingham is the home of one of the world's first and bets known electrochemical supply houses, Cannings, but they got taken over by Macdermid a few years ago. They do still operate out of Birmingham and also supply Hull Cell plates, so give them a call.
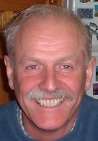
Trevor Crichton
R&D practical scientist
Chesham, Bucks, UK
2002
I too have thought about a possible substitute for the silver plated brass or copper plates required in the Daguerrean process. Since main requirement seems to be one that produces a perfectly flat & polished metallic silver surface, I have often thought that a glass substrate would be just as good as a metallic one. Glass of the float process already comes with a ripple free surface, and is probably already defect free enough to be used with very little additional polishing (using either cerium oxide, or optical rouge). Any of several books on amateur telescope making will give adequate details on polishing. One does not have to be quite as careful for photographic purposes as one does in making astronomical telescope mirrors--therefore one does not have to aim for anything like 1/4 wave surface flatness. Many of the older telescope making books also give details of several different methods of the chemical silvering process (and these methods can also be found on the internet). Possible advantages of glass plates are that are rigidity, easy cut to fit any convenient plate-holder size, can be had with a superbly flat surface, and it doesn't get those impossible to remove bends that thin metal sheets can get in a moment of mishandling.
Thomas B. McHughRetired--amateur experimenter/hobbyist - Broadwater, Nebraska, U. S. A.
2006
Q, A, or Comment on THIS thread -or- Start a NEW Thread