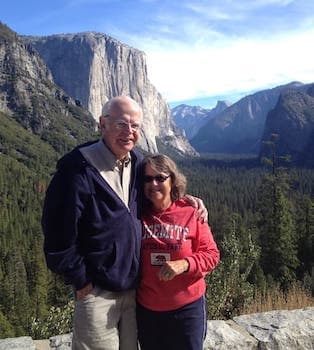
Curated with aloha by
Ted Mooney, P.E. RET
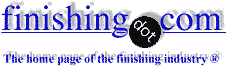
The authoritative public forum
for Metal Finishing 1989-2025
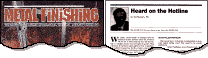
-----
Anodizing's Impact on Fatigue Strength
Q. I understand that Chromic and Hardcoat anodize reduces the fatigue strength of the aluminum. I also realize that Chromic has less of an impact than the Sulfuric Hardcoat. The only information I can find is it ranges from 5-50% decrease in cycles failure. Are there any references to get more exact numbers?
Paul Oppenheimer- Washington, DC
2002
A. I don't think you're going to find what you are looking for wrapped up in the neat package you'd probably prefer. But what is available is numbers for anodizing thickness, and this is what most directly causes the fatigue strength reduction. The thickness of sulfuric acid anodizing is usually several ten thousandths of in inch, while chromic acid anodizing thicknesses are perhaps a tenth of that.
Now, if you have a thin aluminum sheet, and sulfuric acid anodize both sides, it sounds very possible that you could reduce the thickness enough that the fatigue strength could be reduced by 50 percent. Conversely, if you had a heavy casting or extrusion which you chromic acid anodized, it's very possible that you would reduce the thickness so little that the fatigue strength would decline by 5 percent or less.
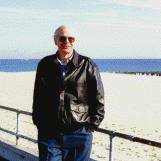
Ted Mooney, P.E.
Striving to live Aloha
finishing.com - Pine Beach, New Jersey
2002
Q. Aside from the loss of substrate thickness reducing the fatigue strength, I look at a hard coated aluminum as a ductile core with a brittle coating. The ductile core will elongate more than the coating. And the coating is not just sitting on the surface, it is metallurgically bonded. So when a part is strained to the point where the coating cracks would not that crack readily propagate into the ductile core. To a certain extent I guess the crack would be blunted by the core material but with most of the energy of fracture going into crack initiation would one not see an overall reduction in fatigue strength which is the time it take a crack to initiate? A more detailed discussion of this phenomena would be appreciated. Is there a stress below which a hard coat anodized part, say 356 aluminum sand casting, should stay below to achieve 10^6 R=-1 cycles. Although the second volume of the finishing handbook shows not difference at 10^6 cycles giving 8 ksi fatigue strength, what happens as stresses that are in the low cycle regime, i.e. 10 ksi or 15 ksi? Do we see the affects of the anodize coating and its role in high stress - low cycle fatigue environments?
Bob Hathaway- Oshkosh, Wisconsin
2006
A. I have never designed a hard coat anodized component, so don't take me as an expert. But hardcoat, and even conventional sulfuric acid anodizing, is not used on really difficult parts like aircraft components. And this is not solely because of the possibility of entrapped corrosives, but also because of fatigue issues. I think one must assume that the anodized layer is cracked at the most critical point and is acting as a stress enhancer, and that you must keep tensile stresses below the level at which a crack can propagate.
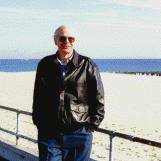
Ted Mooney, P.E.
Striving to live Aloha
finishing.com - Pine Beach, New Jersey
2006
Q. I'm building an ultralight gyroplane out of 6061 -t6 square 2" tube. My question is what kind of anodizing should I use? I read somewhere that proper anodizing does not reduce strength of parts.
Jan safranekcustomer - monterey, California,usa
May 24, 2009
Treatment &
Finishing of
Aluminium and
Its Alloys"
by Wernick, Pinner
& Sheasby
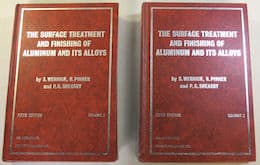
(note: this book is two volumes)
on eBay or
AbeBooks
or Amazon
(affil links)
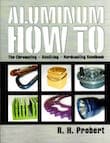
Aluminum How-To
"Chromating - Anodizing - Hardcoating"
by Robert Probert
Also available in Spanish
You'll love this book. Finishing.com has sold almost a thousand copies without a single return request :-)
A. Hi, Jan. Any anodizing always reduces the fatigue strength of aluminum because some portion of the aluminum is converted to a brittle ceramic like oxide, both reducing the thickness of the aluminum and introducing a stress riser situation. But the impact of chromic acid anodizing, which is thin, is less serious than conventional sulfuric acid anodizing.
Regards,
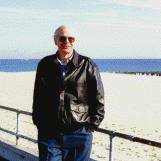
Ted Mooney, P.E.
Striving to live Aloha
finishing.com - Pine Beach, New Jersey
May 25, 2009
May 19, 2010
A. Was just browsing looking for some info on hard/thick anodising and came across this thread. I thought I would offer the following:
In my experience in the Aerospace industry, we find the following to be true:
We almost never use chromic anodising, because we experience it to give a slightly more severe fatigue penalty than sulfuric and because hexavalent chrome is a major health and safety problem in the supply chain (at least in Europe).
These considerations significantly outweigh the advantage of chromic which is that any remnant electrolyte in pores is innocuous. We find that it is possible to control sulfuric anodising sufficiently to prevent the problem impacting the business, but this does mean high levels of process specification/audit, etc., that other industries might not want to put in place.
There is a type of sulfuric anodising - thin film sulfuric - which trades off some corrosion protection in return for an almost undetectably small fatigue penalty.
I don't know anything about hard or thick anodising for wear resistance - we use alternative methods for this that don't impact the fatigue strength of the substrate - so I can't comment on them.
I also can't offer much real insight into why we find the effects I've described, just that a great deal of mechanical testing over many years supports the conclusions. We find that on our parts (which tend to be pretty chunky) that the fatigue debit effect is not so much related to reduction in effective part section it is a genuine material-level effect related to an increased rate of crack initiation in the anodised layer followed by propagation from the anodising into the substrate. Understanding of these effects is mostly empirical rather than theoretical.
Hope this helps.
aerospace - Derby, UK
Thanks, Jon. I hadn't heard of chromic acid anodizing causing a more severe fatigue penalty than sulfuric acid anodizing, but I'm not in that field, and am happy to acknowledge that you could be right. Ultimately, all knowledge is empirical, and your data from testing easily trumps any theoretical constructs I might have learned or mislearned :-)
Regards,
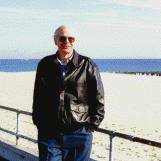
Ted Mooney, P.E.
Striving to live Aloha
finishing.com - Pine Beach, New Jersey
November 2014
October 25, 2011
Q. I am specifying aerospace parts in 2000 series aluminium alloy to be sulfuric acid anodised and dyed black in both 'Hard' and 'Soft' forms. A Filter Bowl (male thread) is hard anodised to prevent thread galling and a Filter Head (female thread) is standard anodised.
I have specified a thicker than normal anodise film in order to get a dense and matched colour black. 0.05 mm (hard anodise) and 0.005 mm (standard anodise) give a dense colouration.
Because the high copper alloy is sensitive to intergranular corrosion, the hard anodise part will be sealed with hot sodium dichromate and the standard anodised part will be sealed with cold Nickel Fluoride solution and hung using aluminium jigs (all to reduce corrosion susceptibility).
I have been researching the internet on anodising effect on fatigue resistance and discover that the thicker the coating, the lower the allowable stress in order to counteract the reduction in fatigue resistance.
Is there a table of 'knock down' stress factors which can be applied to anodise coating thickness? Can anybody help?
I was interested to read of the sulfuric acid 'thin film anodising' in this thread which is carried out by some processors: does this comply with MIL-A-8625 / MIL-PRF-8625
[⇦ this spec on DLA] or DEF STAN?
As a slight aside, I had some aluminium alloy parts from my Yamaha cruiser polished and then in order to protect the high lustre finish had them 'flash anodised'. This is a 30 second electrolytic treatment in sulfuric acid which doesn't go through the etch process. It doesn't dull the parts like standard anodising. So far, the bike parts look amazing, and have retained their lustre. Has anyone else used this process?
John Grant
Aerospace - Fareham, United Kingdom
Q. 1. What is the effect of anodising in fatigue properties and how much degradation, and the type of anodizing?
2. Aluminum anodizing poses pits on the surface, how deep is the pit before it creates problem as fatigue initiation site?
Thanks,
- Long Beach, California, USA
February 15, 2012
A. Hello Terry,
All anodizing processes always lead to a decrease of the fatigue life limit of the aluminum material but not all in the same proportion.
1- Roughly speaking and for High Cycling Fatigue (i.e., more than 1M cycles ; it will be less at lower cycles) the decrease could be :
- from -15% to -40% for sulfuric acid
- around -50% for hard anodizing
- around -10% for chromic acid
But these values are highly dependent of the pre-treatment conditions (pickling), of the nature and manner of the mechanical stress, of the thickness of the layer...
2- As far as I know, there is a weak link between number of pits and this decrease, but the main reason is internal stresses in the anodized layer.
Regards,
Bernard
- FRANCE
Q. What is the tensile strength of the anodize LAYER?
I say here, the LAYER.
We are making some frangible means out of aluminum. Will the anodize process increase OR decrease the strength of the part? If minimal, we'd still like to know.
Thanks.
- milford, Connecticut usa
November 26, 2014
A. Hi. I don't know what you mean by "frangible means". Might there be a typo?
We have to be careful also about what you mean by "strength of the part". Anodizing is a brittle (less that 0.5% elongation) coating that adds nothing to the tensile strength of the member (consider the tensile strength of the anodize layer to be zero), and reduces rather than increases the allowable load on the aluminum component due to the loss of the aluminum which was converted to aluminum oxide. Readers above have also told us that the coating, being bonded to the substrate, seems to initiate cracks. The effect on the fatigue strength can be significant.
Regards,
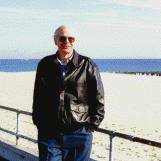
Ted Mooney, P.E.
Striving to live Aloha
finishing.com - Pine Beach, New Jersey
November 2014
May 3, 2016
A. Here you go:
dspace.dsto.defence.gov.au/dspace/bitstream/dsto/10291/1/DSTO-TN-1180%20PR.pdf.
Page 12 shows the reduction in fatigue strength of 7075-T6 after Chromic unsealed, Sulfuric unsealed and Sulfuric sealed.
At thin layers (sub 2 micron) Chromic unsealed and Sulfuric unsealed are essentially the same, with the sealed Sulfuric having a fatigue strength about 20% lower. But beyond 10 microns Chromic dramatically decreases in strength.
If you are anodizing using MIL-A-8625 / MIL-PRF-8625
[⇦ this spec on DLA]
or a similar spec your allowable thickness for Chromic (Type I) is .5 microns to 17.8 microns (Big spread!)
Sulfuric (Type II) is 1.8 microns to 25 microns which is still a huge spread BUT Sulfuric is less affected by greater than normal thicknesses.
Long story short, if you have a fatigue sensitive part, you need to control the anodize thickness, just like controlling the dimensions. (essentially the mechanism, as I understand it, is the hard anodic coating is brittle and forms microcracks over time. The harder & thicker the coating the larger those microcracks and the more likely they are to propagate.)
Pall Corporation - New Port Richey, Florida
----
Ed. note Aug. 2018: Unfortunately that site appears to be off the air, and the page never archived by archive.org. However, finishing.com did archive it: click on the graphic.
Q, A, or Comment on THIS thread -or- Start a NEW Thread